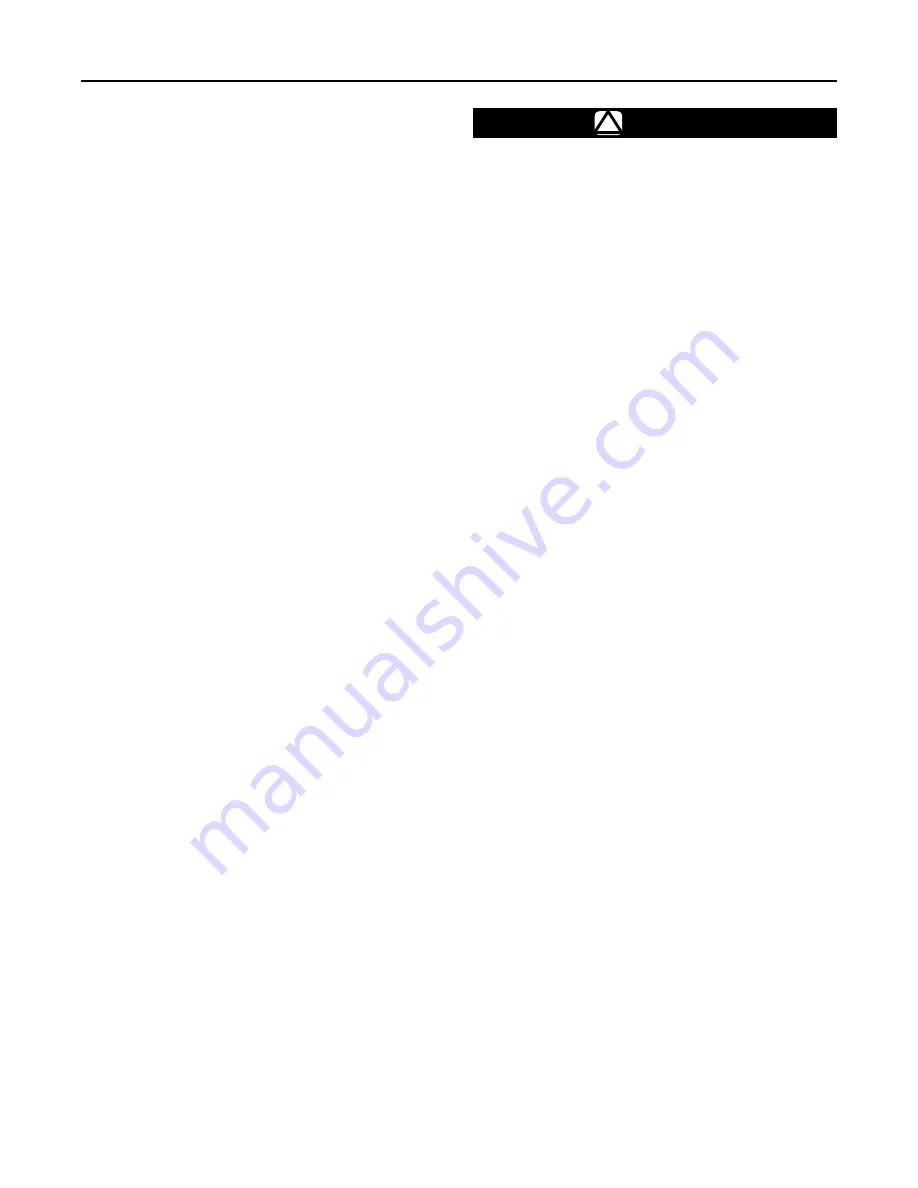
Type MR105
16
16.
Place the lower spring seat (key 54) and Belleville
spring washer (key 49) over the actuator stem
(key 40) and on top of the diaphragm (key 56).
The raised inner diameter of the spring washer
should be pointing toward the threaded end of the
actuator stem.
17.
Lubricate the threads of the actuator stem (key 40)
and thread the two jam nuts (key 48) onto it. Using
wrench flats, hold the stem and torque the two jam
nuts individually. Tighten to a torque of
12 to 14 ft-lbs / 16 to 19 N•m.
18.
Install the upper diaphragm casing (key 63)
while aligning the bolt circle holes in the upper
diaphragm casing, diaphragm (key 56) and lower
diaphragm casing (key 62).
Note
Exercise care to ensure that the
diaphragm (key 56) is not pinched,
twisted or wrinkled while compressing
between the upper and lower diaphragm
casings (keys 62 and 63).
19.
Lubricate the cap screws (key 57) and nuts (key 58)
and carefully insert through holes in the outer flange
of the diaphragm casings (keys 62 and 63) and
diaphragm (key 56). Tighten the cap screws to
the hex nuts to a final torque value of 45 to
55 ft-lbs / 61 to 75 N•m.
20.
Place the control spring (key 68) inside the hole in
the upper diaphragm casing (key 63) and over the
lower spring seat (key 54). The spring should be
sitting on top of the lower spring seat.
21.
Lubricate the bore on the top of the upper spring
seat (key 69) where the adjusting screw (key 73)
will make contact. Place the upper spring seat on
top of the control spring (key 68).
22.
Install the spring case (key 70) over the control
spring (key 68) and upper spring seat (key 69) and
on top of the upper diaphragm casing (key 63).
Align the holes in the spring case with the holes in
the upper casing while ensuring the vent assembly
(key 26) is aligned with valve body inlet.
23.
Lubricate cap screws (key 67) and use them
to secure the spring case (key 70) to the upper
diaphragm casing (key 63). Tighten the cap
screws to a final torque of 25 to 28 ft-lbs / 34 to
38 N•m.
!
WARNINg
Personal injury, equipment damage or
leakage due to escaping fluid may result
if adjusting screw (key 73) and jam nut
(key 72) are not installed properly. Also,
spring (key 68) may go solid resulting in
regulator not locking up if jam nut is not
installed and adjusting screw is adjusted
completely down.
24.
Lubricate the adjusting screw (key 73) and thread on
the jam nut (key 72). If pressure-loaded actuator is
used, install the sealing washer (key 71). Lubricate
the adjusting screw and place it into the spring case
(key 70). Thread the adjusting screw using a hand
wrench (not an impact gun) until it touches the
upper spring seat (key 69). Set the regulator to the
desired outlet pressure according to the procedure in
Adjustment section.
Regulator Reassembly
As indicated by the square callouts in Figure 6, it is
recommended that a good quality pipe thread sealant
be applied to pressure connections and fittings and a
good quality lubricant be applied to O-rings. Also apply
an anti-seize compound to the adjusting screw threads
and other areas as needed.
After repair, the regulator should be tested for proper
operation before being put back into service.
Parts Ordering
When corresponding with your local Sales Office about
this regulator, always reference the equipment serial
number or FS number found on the nameplate.
When ordering replacement parts, reference the key
number of each needed part as found in the following
parts list. Separate kits containing all recommended
spare parts are available.
Parts List
Note
In this parts list, parts marked NACE are
intended for corrosion-resistant service
as detailed in the NACE International
Standard MR0175-2003 and MR0103.