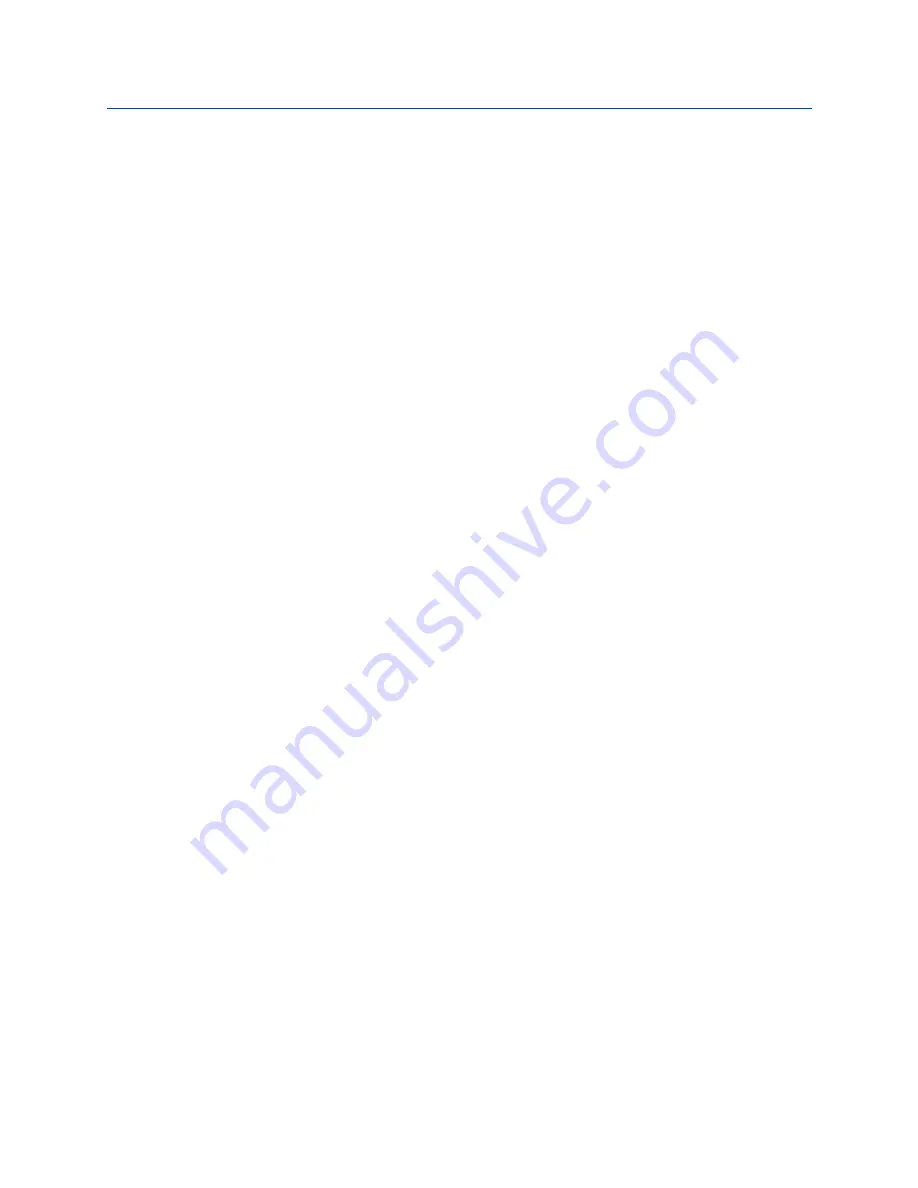
Reference Manual
24625020, Rev AA
March 2017
1
Section 1
Introduction
1.1
Using this manual
The sections in this manual provide information on installing, operating, and maintaining
the Mobrey
™
Hydratect 2462. The sections are organized as follows:
Section 2: Installing the electrodes
contains the procedures for mounting electrodes to a
pipe or manifold.
Section 3: Installing the Electronics Control Unit
contains the mechanical and electrical
installation procedures.
contains procedures to check the operation of the Hydratect 2462
system after installation completion or any configuration change.
Section 5: Electrodes Servicing
describes the electrode servicing procedure that must be
followed to ensure continued and trouble-free operation of the Hydratect 2462 system.
Section 6: Electronics Servicing
contains fault-finding and fault-correction procedures for the
electronics control unit.
Section A: Specifications and Data
contains specifications and other reference data, including
dimensional drawings.
1.2
Product recycling/disposal
Recycling of equipment and packaging should be taken into consideration and disposed of
in accordance with local and national legislation/regulations.
1.3
What the Hydratect 2462 does
The Hydratect 2462 system is the electronic alternative to conventional water level
switches on steam-raising plant. The system contains a compact, two-channel electronic
control unit connected to a pair of electrodes that are mounted in the plant pipe-work
(See
Each of the two channels gives independent indications of the presence of water or steam
that are much more reliable than those obtained with conventional electro-mechanical
devices. The electronics control unit provides a local indication of steam, water, and fault
states, and has configurable fault- and trip-outputs.
Typical applications of the Hydratect 2462 system are:
Drain pots.
Water detection in steam lines.
Low- or high-level water detection.
Wherever it is necessary to detect water or steam.
Summary of Contents for Mobrey Hydratect 2462
Page 2: ......
Page 16: ...10 Reference Manual 24625020 Rev AA Introduction March 2017 Introduction ...
Page 52: ...46 Reference Manual 24625020 Rev AA System Testing March 2017 System Testing ...
Page 62: ...56 Reference Manual 24625020 Rev AA Electronics Servicing March 2017 Electronics Servicing ...
Page 65: ......