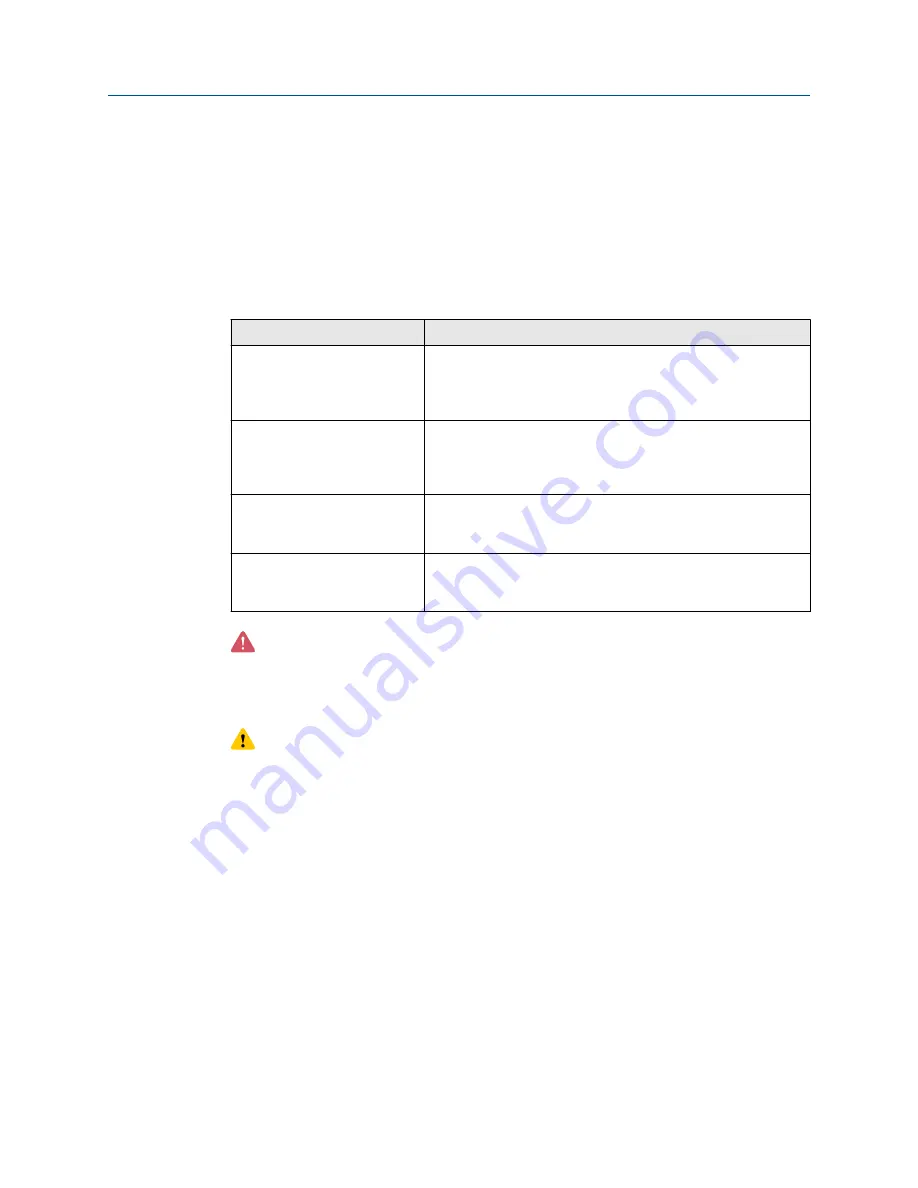
3
Transmitter power and I/O wiring
3.1
Options for wiring
The wiring procedure you follow depends on which electronics option you have.
Table 3-1: Wiring procedures by electronics option
Electronics option
Wiring procedure
Integral transmitter
The transmitter is already connected to the sensor. No wiring is
required between sensor and transmitter. See the transmitter
installation manual for wiring the power and signal cable to the
transmitter.
Extended electronics
The electronics are separated from the sensor by an extender and
must be attached as described in
Attach extended electronics
.
There is no wiring required because the physical connection
includes the electrical connection.
MVD
™
Direct Connect
™
There is no transmitter to wire. See the
Micro Motion MVD Direct
Connect Meters
manual for wiring the power and signal cable
between the sensor and the direct host.
Integral core processor with
remote transmitter
The core processor is already connected to the sensor. Connect a
4-wire cable between the core processor and transmitter. Refer
to
Connect 4-wire cable
.
DANGER
Make sure the hazardous area specified on the sensor approval tag is suitable for the
environment in which the sensor will be installed. Failure to comply with the
requirements for intrinsic safety in a hazardous area could result in an explosion.
CAUTION
Fully close and tighten all housing covers and conduit openings. Improperly sealed
housings can expose electronics to moisture, which can cause measurement error or
flowmeter failure. Inspect and grease all gaskets and O-rings.
3.2
Connect 4-wire cable
3.2.1
4-wire cable types and usage
Micro Motion offers two types of 4-wire cable: shielded and armored. Both types contain
shield drain wires.
The cable supplied by Micro Motion consists of one pair of red and black 18 AWG
(0.823 mm
²
) wires for the VDC connection, and one pair of white and green 22 AWG
(0.326 mm
²
) wires for the RS-485 connection.
User-supplied cable must meet the following requirements:
Installation Manual
Transmitter power and I/O wiring
20002346
January 2019
Installation Manual
13
Summary of Contents for Micro Motion H Series
Page 4: ...Contents Installation Manual January 2019 20002346 4 Micro Motion H Series ...
Page 12: ...Mounting Installation Manual January 2019 20002346 12 Micro Motion H Series ...
Page 20: ...Grounding Installation Manual January 2019 20002346 20 Micro Motion H Series ...
Page 23: ...Installation Manual 20002346 January 2019 Installation Manual 23 ...