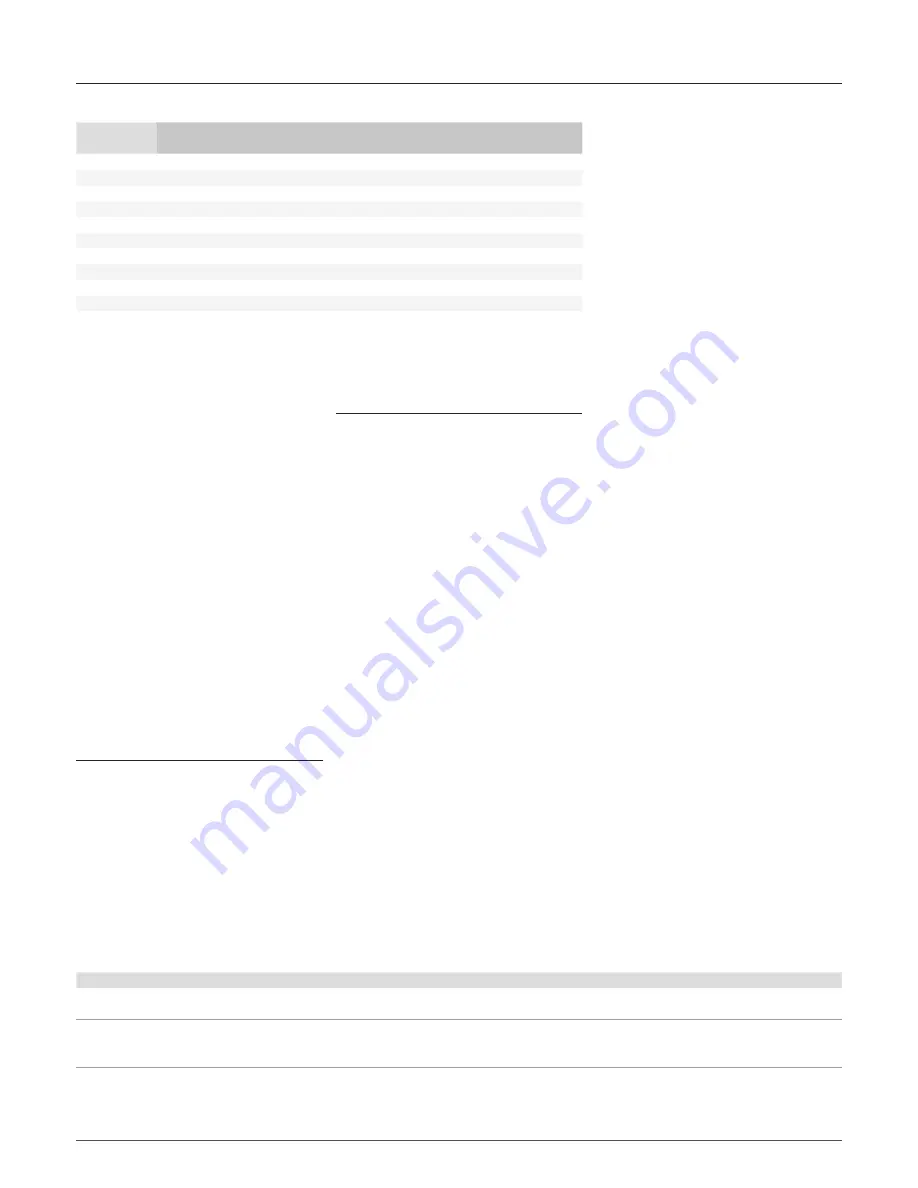
3
1.5
130/
450
/550
180/
500
/625
180/
500
/625
130/
450
/550
2
130/
450
/550
180/
500
/625
180/
500
/625
180/
500
/625
2.5
180/
500
/625
270/
800
/975
270/
800
/975
270/
800
//975
3
270/
800
/975
180/
500
/625
180/
500
/625
270/
800
/975
4
350/
1100
/1400
270/
800
/975
270/
800
/975
270/
800
/975
5
350/
1100
/1400
350/
1100
/1400
350/
1100
/1400
350/
1100
/1400
6
350/
1100
/1400
450/
1500
/1800
450/
1500
/1800
450/
1500
/1800
8
450/
1500
/1800
550/
2125
/2650
450/
1500
/1800
550/
2125
/2650
10
450/
1500
/1800
550/
2125
/2650
625/
2125
/2650
625/
2125
/2650
12
550/
1500
/1800
625/
2125
/2650
700/
2125
/2650
700/
2125
/2650
Keystone
ComPoSeAL butteRfLy vALveS, wAfeR StyLe
InstallatIon and MaIntenance InstructIons
table 1
size
Minimum / recommended / Maximum flange bolt torque [lbs in]
[nPs]
Pn 6
Pn 10
Pn 16
asMe 150
notes
bolt specifications: minimum class 8.8, coarse thread, friction thread and nut-flange friction: 0.14
2.3.2 new system
1. with the disc in near-closed position, center
each mating flange with the valve body. fix
the body with some flange bolts and tighten
the bolts (do not exceed the maximum
tightening moments, see table 1).
2. use the flange-valve-flange assembly for
fit-up and centering to the pipe.
3. tack-weld the flanges to the pipe.
4. Remove the bolting and remove the valve
from between the flanges.
5. finish-weld the flanges to the pipe and
allow the flanges to cool completely.
6. install the valve according the procedure for
installing in the existing system.
iMPortant
Do not finish-weld the flanges to the pipe with the
valve bolted between the flanges as this will result
in serious heat-damage to the composite body
and the flange sealing rubber O-ring.
2.6 troublesHooting guide
symptom
Possible cause
resolution
valve would not rotate
Actuator has failed
Replace or repair
valve packed with debris
flush or clean valve to remove debris
valve leaking
valve not fully closed
Close valve
debris trapped in valve
Cycle and flush (with valve open) to remove debris
Seat is damaged
Replace valve
Jerky operation
debris trapped in valve
Cycle and flush (with valve open) to remove debris
Air supply actuator inadequate
increase air supply pressure and/or volume
2.4 valve veriFication
Check the operation of the valve by operating it
from ‘fully open’ to ‘completely closed’ position.
to verify the valve operation, the disc position
indicator on the actuator or the handle should
rotate between the ‘fully open’ and ‘completely
closed’ indicators on the actuator or throttling
plate. generally the valve disc travels clockwise
to close.
2.5 sources oF Possible danger
2.5.1 Mechanical
when manual operators are used, available
space should be checked to prevent the risk of
jamming hands.
iMPortant
Use pliers to snap-off the nibs and wear eye
protection to prevent hand and eye injuries.
2.5.2 electrical
the composite material can be electro
statically charged by a fluid passing on the in-
and/or outside of the valve. when discharging
a spark might rise. behavior of the valve is not
different from plastic piping.
2.5.3 thermal
A) if the valve is used in applications with a
fluid temperature greater than 104ºf or
less than -4°f precautions should be taken
to prevent injury from touching the valve
outer surface. Also, the handle or operator
of the valve might be extreme hot or cold.
Personnel should use proper personal
protection equipment to prevent injuries.
for example: protection gloves.
b) hot surfaces can be a potential source of
ignition of the environment.
2.5.4 operational
A) Closing a valve too fast may result in
water hammer in the upstream part of the
pipeline. water hammer results in excessive
stresses in the valve and will cause severe
damage. water hammer should be avoided
in all circumstances.
b) A fluid passing the disc of a butterfly
valve has the tendency to close the valve
disc. take care when unlatching the valve
operating mechanism.