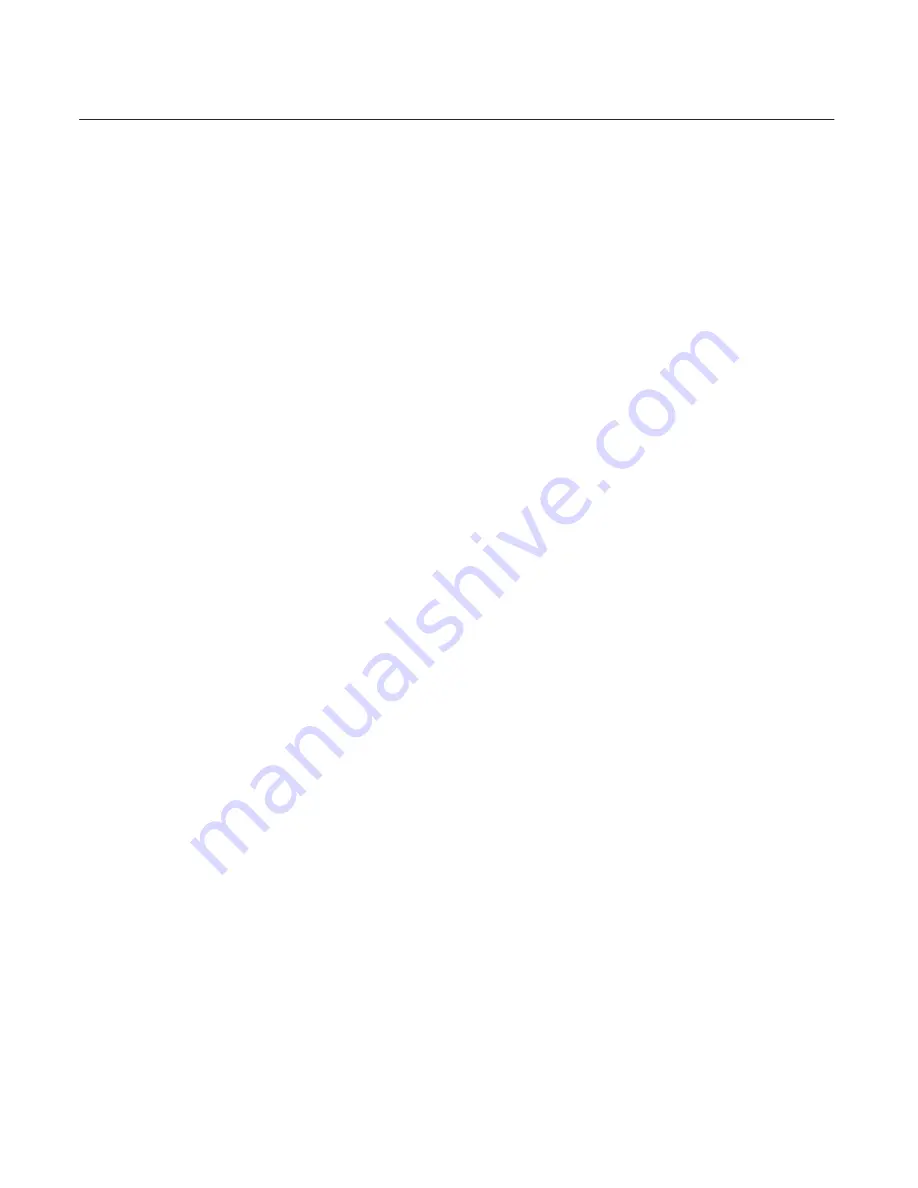
i2P-100 Transducer
Instruction Manual
Form 5777
September 2004
11
in this manual. Improper techniques
can cause poor quality repairs and
impair the safety features of the
device.
The converter module and the
electronics module are non-repairable.
If troubleshooting or alignment
attempts indicate a faulty converter or
electronics module, replace the
module or return the transducer to
your Fisher sales office for repair.
Troubleshooting
Electrical
The following procedures require taking the control
valve/actuator assembly out of service. Provide
some temporary means of process control before
taking the control valve out of service.
1. Ensure terminal lug connections from the control
device to the transducer are of the correct polarity
(refer to the electrical connection procedures in the
Installation section of this manual).
2. At the transducer, ensure that the milliampere dc
signal is applied, and ensure that it is within the 4 to
20 milliampere range.
3. Check switches and ensure that they are properly
set. Refer to figure 10.
4. If the problem has not been resolved, see
Electronics Module Replacement in this manual.
Pneumatic
Provide a 4 to 30 milliampere dc current source,
supply pressure, and a gauge to monitor the output
pressure when checking transducer operation. Refer
to figure 13 for key number locations.
1. Ensure that supply pressure to the transducer
meets your requirements [0.3 bar (5 psi) higher than
upper range limit of output signal, with a maximum of
3.4 bar (50 psi)].
2. Ensure that the filter (key 11) and restrictor
(key 10) are open and clean. Remove the two
screws (key 14), the filter cap (key 13) and the
O-ring (key 12) to access the filter and restrictor.
3. If a filter/regulator is used, ensure that it is
working correctly. If not, ensure the dripwell is not
plugged because of excessive moisture
accumulation. If necessary, drain off any moisture,
and clean or replace the filter element.
4. Force the converter module to maximum output
pressure with a 30 milliampere dc signal. Output
pressure should build up to the approximate value of
the supply pressure [maximum of 3.4 bar (50 psi)].
5. When the input current is removed, the
transducer output pressure should drop to less than
0.14 bar (2 psig). If it does not, check to ensure the
vent and exhaust air passageway is free from
foreign material.
6. To inspect the relay assembly, refer to the Relay
Maintenance procedures in this manual.
7. If the problem has not been resolved, see
Converter Module Replacement in this manual.
Converter Module Replacement
Removal
Refer to figure 13 for key number locations.
1. Remove the housing cap (key 2) (the cap farthest
away from the conduit). Note that the two set screws
(key 8) need to be loosened to remove the cap.
2. Unscrew the two captive screws (key 52) and
remove the converter module from the housing.
3. Inspect the O-ring (key 55) and replace if
necessary.
Replacement
1. Lubricate the O-ring (key 55) with a lubricating
compound such as Dow Corning III before replacing
the converter module in the housing.
2. Insert the converter module into position in the
housing (key 1). Replace the two screws (key 52)
and tighten them.
3. Replace the housing cap (key 2), making sure to
re-tighten the two set screws (key 8).
4. Electrically calibrate the unit using the procedure
in the Calibration section of this manual.
Electronics Module Replacement
Removal
Refer to figure 13 for key number locations.
1. Remove the housing cap (key 2) (the cap closest
to the conduit). Note that the two set screws (key 8)
need to be loosened to remove the cap.
2. Note the location of the wires, then remove the
electrical wiring from the terminal block.