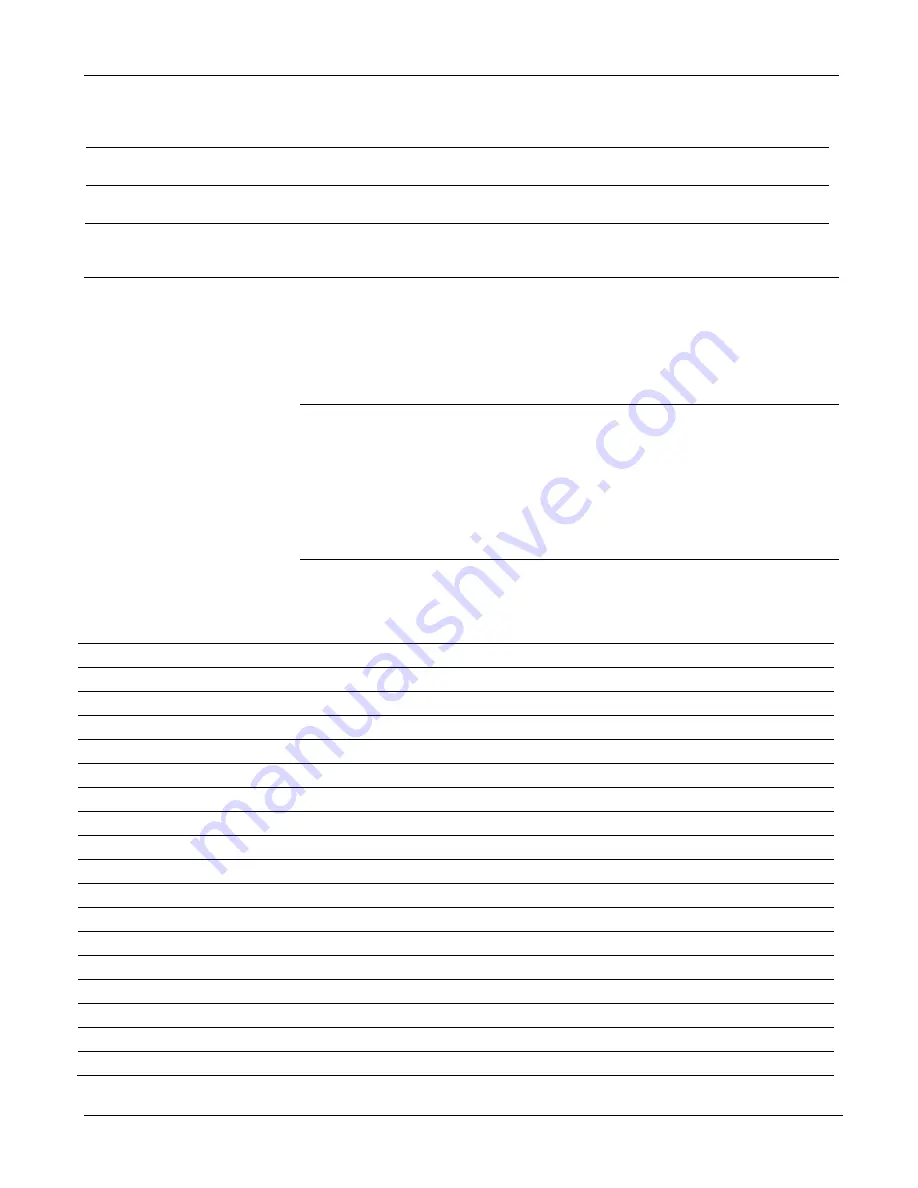
FloBoss 107 Instruction Manual
Revised June-2017
Power Connections
3-3
Table 3-1. Input Terminal Block Connections
Terminal Blocks
Definition
Volts DC
PWR (IN + / IN
–)
Accepts up to 28 Volts dc nominal from an AC/DC converter
or other 28 volts dc supply.
8 to 30 Volts dc
LOOP and GND
Supplies 10 Volts dc or 24 Volts dc source voltage to
external field devices. Current limit protected.
10 Volts dc or 24 Volts
dc
3.2
Determining Power Consumption
Use
Table 3-1
to identify and
Table
3-2
to calculate the power
requirements for the configuration of your FB107. If the power input is
not sufficient, you must either provide an alternative power supply for
external devices or reduce power demands. See
Table 3-3
for an example
of a completed power consumption worksheet.
Note:
The worksheet shown in
Table 3-2
is available to registered users
as a Microsoft Excel
®
spreadsheet on the Remote Automation
Solutions SupportNet
™
website. Access
www.EmersonProcess.com/Remote/Support/Support_login.html
and look for
FB107_Power_Wksht.xls
under
Downloads.
Download the spreadsheet to calculate—and manage—variations
on your particular power requirements.
Table 3-2. Estimated Power Consumption by Module
Valid Slots
Module Description
Base Idle
(No Load)
Max Active
(Full Load)
Loading
Factor
Module Power
2
in mW
0
CPU Non-Isolated
360
360
100%
360
0
CPU Non-Isolated with I/O
396
476
100%
476
0
CPU Isolated
540
540
100%
540
0
CPU Isolated with I/O
576
656
100%
656
1,2
RS-232 Module
21
50
100%
50
1,2
RS-485 Module
27
35
100%
35
1,2
Enhanced Comm Module
450
610
100%
610
1,2
Dial-up Modem Module
1
2
100%
2
1 through 7
1
6-Point I/O Module
180
260
100%
260
1 through 7
1
DO Relay Module
180
270
100%
270
1 through 7
1
8-Point AI/DI Module
145
3900
100%
3900
1 through 7
1
6-Channel AO/DO Module
320
2900
100%
2900
1 through 7
1
3-Channel RTD Module
220
225
100%
225
1 through 7
HART Module
210
410
100%
410
1 through 7
MVS Interface Module
150
200
100%
200
1 through 7
APP 485 Application Module
150
160
100%
160
1 through 7
IEC 62591 Module
1080
1440
100%
1440
1,2
Network Radio Module
288
720
100%
720