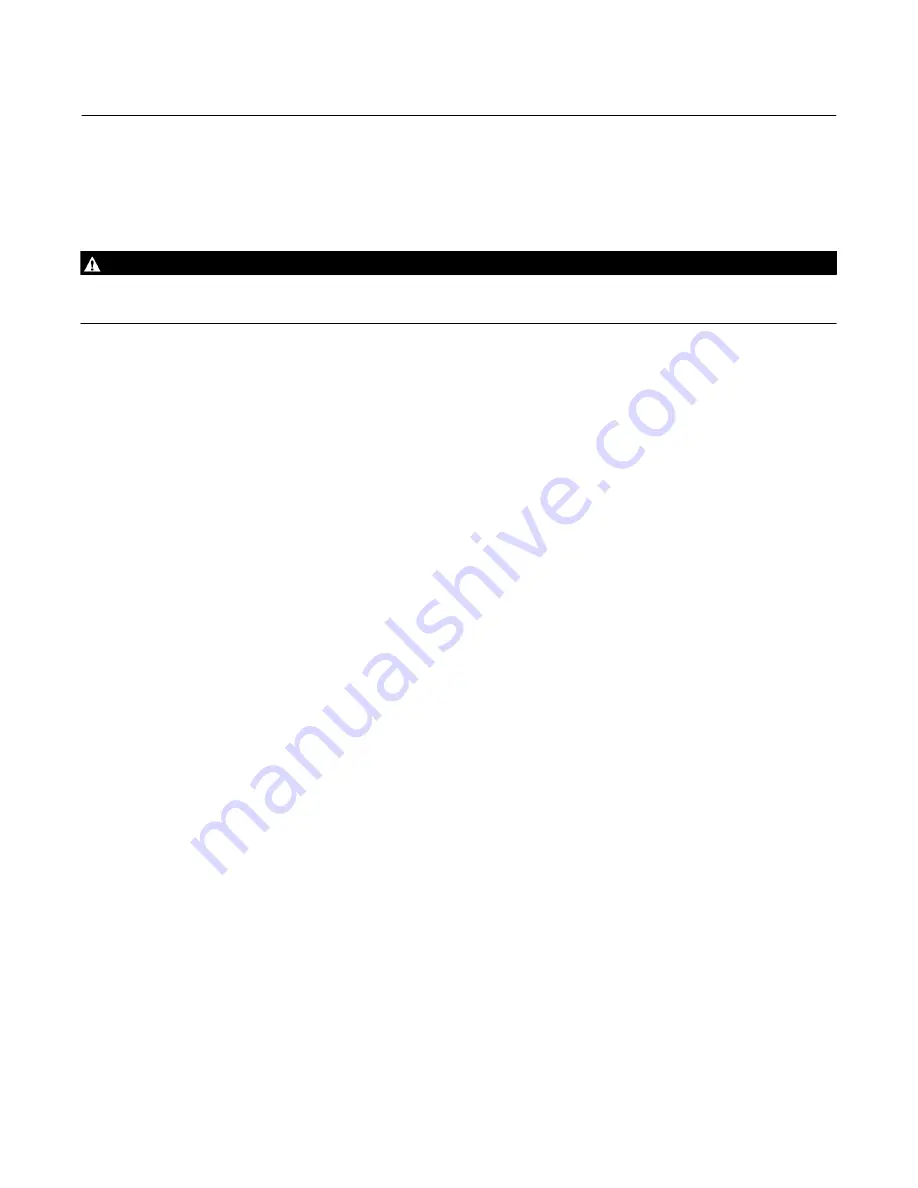
Instruction Manual
D104425X012
V280 Valve
August 2019
12
10. Lubricate (key 33) the half-dovetail groove on the tailpiece (key 2) and install the O‐rings (key 12) in both tailpieces.
11. If necessary, install the grooved end of the groove pins (key 23) into the bearing plate (key 8) as far as they will go.
12. Install new bushings (key 9) in the bearing plates (key 8) by aligning the split in the bushing towards the longer side
of the bearing plate (see figure 4).
WARNING
When lifting the ball, ensure the bearing plates (key 8) are secure on the ball trunnions to prevent parts from falling which
may cause personal injury or property damage.
13. Use an approved lifting sling through the ball bore to lift the ball (key 3). Orient the ball so the port and trunnions
are parallel with the ground.
14. Lubricate and install the thrust washers (key 10) and bearing plates on both ball trunnions.
15. Install the ball and bearing plates assembly onto the lower tailpiece. While lowering the ball, guide the groove pins
in the bearing plates into their proper location in the tailpiece pin holes.
16. Place the body (key 1) on an appropriate work surface.
17. Install the grooved end of the groove pins (key 22) into the body. Take care to not bend the pins during assembly.
18. If studs (keys 4) were removed from valve body during disassembly, apply anti-seize lubricant (key 45) to the
threads of the studs and holes and install in both sides of the body with the material identifier facing outward.
19. Lubricate (key 33) the tailpiece O-ring sealing surface of the body and lower the body over the ball and onto the
tailpiece, guiding the body over the ball and aligning the pin holes on the tailpiece with the groove pins (key 22)
installed in the body. Make sure that the body shaft bore is aligned to the same side as the tang slot on the ball.
20. Apply anti-seize lubricant (key 45) to the face and threads of the nuts (key 18). Install the nuts on the studs by hand
with the material identifier facing outward. Use an appropriate torque device to apply the final torque specification
(see table 3).
21. Repeat step 19 before installing the upper tailpiece.
22. Install the upper tailpiece from steps 1 through 10 over the studs (key 4) and pins (key 22) installed in the body.
23. Repeat step 20 once the upper tailpiece has been installed on the body.
24. Insert the drive shaft (key 20) through the body shaft bore to engage the shaft tang with the ball tang slot. Install
the shaft thrust washer (key 11) onto the shaft.
25. Install the drive shaft bushing (key 7) in the packing box housing from the end that engages the body.
26. Lubricate (key 33) and install the O-ring (key 13) and back-up ring (key 16) on the packing box housing.
27. Lubricate the packing box housing studs (key19) with an anti-seize lubricant (key 45) and install in the valve body.
28. After lubricating (key 33) the body shaft bore, position the packing box housing assembly over the drive shaft and
slide into place ensuring the O-ring (key 7) properly engages the body shaft bore. Make sure to orient the length of
the packing box housing perpendicular to the bore of the valve body (see figure 4).
29. Install the packing components as detailed in the Packing Maintenance section of this manual.
30. Apply anti-seize lubricant to the packing box housing nuts (key 21) and torque to the required specifications (see
31. For keyed shafts, install the valve shaft key (key 38), flat washer (key 39) and hex head bolt (key 40). The purpose of
the washer and hex bolt is to prevent the key from migrating axially out of the keyway in-service.
32. If the base bracket was removed from the body during disassembly, place it on the body flats that correspond with
the desired shaft orientation (horizontal or vertical). Lubricate the two socket head cap screws with an anti-seize
lubricant (key 45), place a washer (key 41) over each screw, and install into the body. Torque to the required
specifications (see table 4).