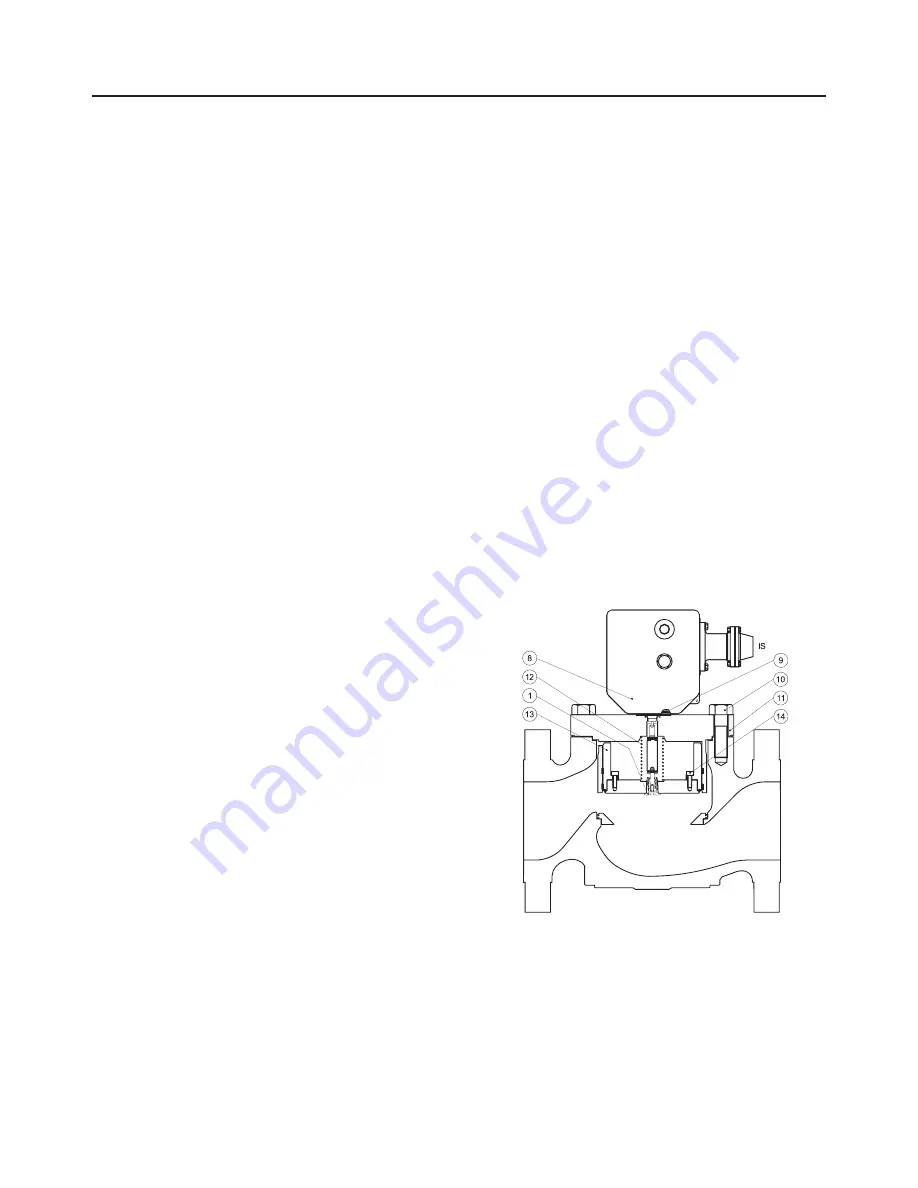
Type OSE
6
C57
Figure 7.
Type OSE - Commissioning Schematic
Commissioning
(max. only or max. & min.)
•
Inlet valve
→
Open slowly
•
Slam-shut bypass
→
Open slowly (stage 2)
•
Regulator
→
Put into operation (see corresponding manual)
•
1
st
release relay stage
→
Set (Stage 1)
•
Slam shut valve plug
→
Open (Stage 3)
•
Outlet valve
→
Open slowly
The equipment is commissioned
After checking and commissioning the release relay it is
recommended to seal it
MaiNTENaNCE
Servicing Check
recommended frequency:
•
Twice yearly minimum
Verification:
•
Tripping and tripping value
•
Slam-shut tightness
Departure positions
•
Inlet valve
→
Open
•
Outlet valve
→
Open
•
Slam-shut
→
Open
•
Regulator
→
In operation
Inlet and outlet sides of regulator under pressure
Tripping verification
•
Inlet valve
→
Closed
•
Outlet valve
→
Closed
•
Regulator
Increase setpoint to reach tripping
(without exceeding the outlet limits)
Disassembly
recommended frequency
:
•
Every 4 to 6 years (or less depending on
operating conditions)
•
In the case of BMS 162 or 071, it is highly recommended to
check the condition of the diaphragm once yearly
Verification
:
•
Condition of O-rings, diaphragm, and lubrication
replacement
:
•
O-rings, diaphragm
Tools
:
•
Spanners 10, 13, six-sided wrench 6
•
Spanners According to DN size
•
Emerson spanner ref. 197125 (bypass and pin disassembly)
• Valve plug closed
•
Close inlet and outlet valves
•
bleed off outlet pressure
•
bleed off inlet pressure
•
Unscrew impulse connection
iS
•
Remove BM cover (key 8)
•
Unscrew fastening screw (key 9)
•
Remove cap
•
Remove BM
•
Unscrew screws (key 10)
•
Remove bonnet (key 11)
•
Remove spring (rep. 12) and slam-shut valve plug (key 13)
•
Unscrew bypass (key 1)
•
Unscrew screws (key 14) (DN 100 and 150)
The removal of the orifice (not recommended) requires a
special extraction tool
reassembly
•
Perform the above operations in reverse order (respect
tightening torques)
•
Replace O-rings at each disassembly
•
The valve plug should be maintained in an upright position
using the packing gland to facilitate it’s removal
•
Precaution should be taken when removing or replacing
the valve plug to avoid damaging the segments