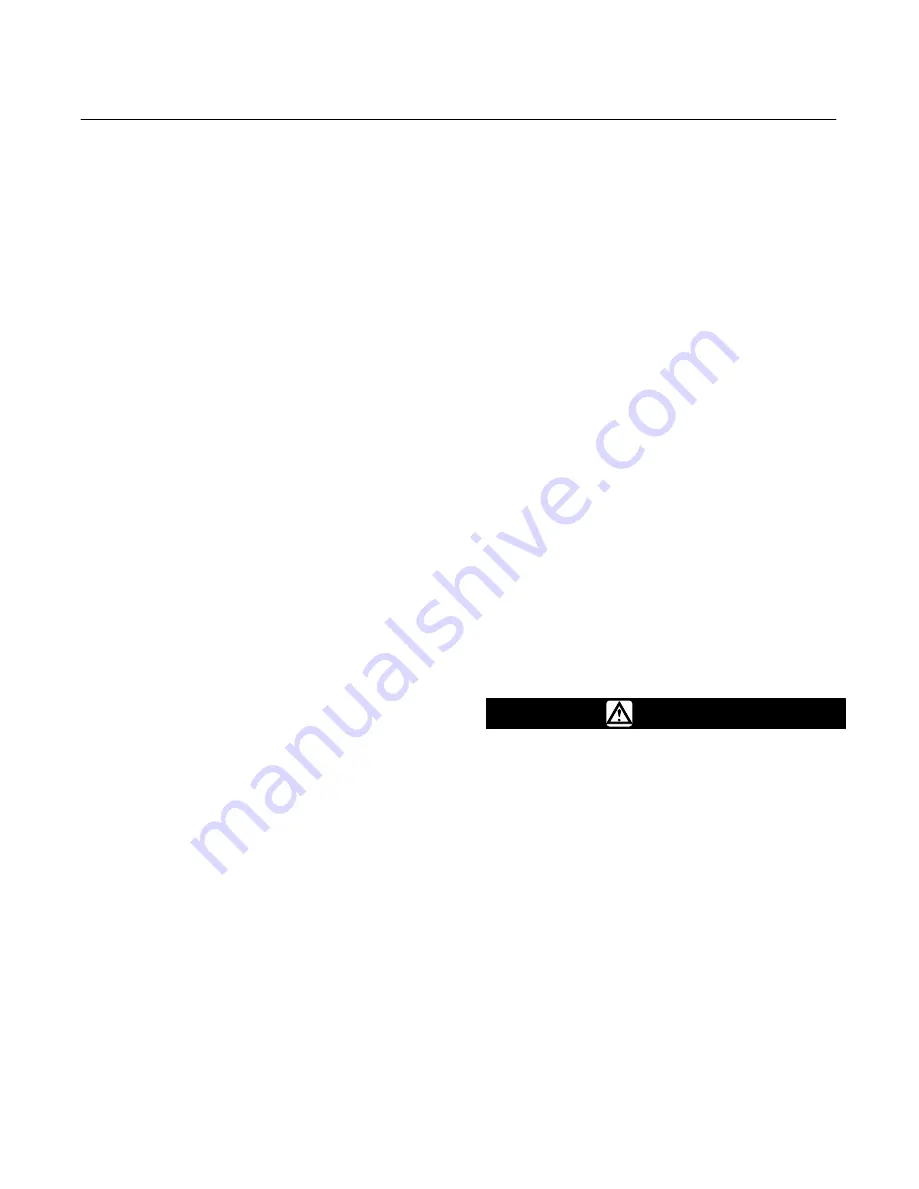
2502 Series Controllers
Instruction Manual
Form 1446
November 2006
12
Differential Relief Adjustment
The differential relief valve protrudes from the back
of the controller case on a construction with an F in
the type number. Although normally factory-set to
relieve when the differential between the
proportional and reset bellows reaches 5 psi, the
differential may be reduced down to 2 psi by turning
the adjustment screw clockwise or increased up to 7
psi by turning the screw counterclockwise. The
minimum differential setting will yield the minimum
set point overshoot during startup.
Depending on the characteristics of the process, the
relief valve can be positioned so that the arrow cast
on the case points either to the letters RE (reset) or
to the letter P (proportional) on the back of the
manifold. To reposition the arrow, see figure 9.
Remove the mounting screws. Reposition the
differential relief valve to RE or P and reinstall the
mounting screws.
Calibration
Precalibration Requirements
Note
Calibration of a unit with a displacer
designed for interface or density
control must be conducted with the
displacer completely submerged in a
liquid of the specific gravity for which
the unit was designed.
To calibrate a controller, it is necessary to place the
device into operation. This may be done on the
vessel with the actual service liquid. It may also be
done in the shop, but other means of obtaining a
displacement force change must be provided. It
must be done in the shop if the process variable is
not available for calibration or if the process cannot
be varied for calibration. There are two methods of
adapting the calibration procedure to shop
calibration: wet and dry.
Wet Calibration
Remove the entire controller and sensor assembly
from the vessel. For caged sensors, pour the liquid
into the cage. For cageless sensors, suspend the
displacer to an appropriate depth in a liquid having a
specific gravity equal to that of the process liquid.
If necessary, use water for wet calibration in the
shop. However, this procedure requires
compensation for the difference between the specific
gravity of the water and that of the process liquids.
For example, assume that the process liquid has a
specific gravity of 0.7 and that wet calibration with
water (specific gravity of 1.0) is desired. To simulate
a process level of 50 percent of the input span, a
water level of 35 percent is required (0.7/1.0 x 50
percent = 35 percent).
Dry Calibration
Remove the controller and torque tube arm, as a
single unit, from the cage or vessel. Then, wherever
the standard calibration instructions in this manual
require a specific process variable for input to the
sensor, simulate that variable by suspending the
proper weight (such as a can of sand) from the end
of the displacer rod. Complete the following
Controller and Torque Tube Arm Disassembly and
the Determining Suspended Weight for Calibration
sections before proceeding to the calibration
procedure.
Controller and Torque Tube Arm
Disassembly
WARNING
To avoid personal injury from contact
with the process liquid, lower the
vessel level below the sensor torque
tube arm, or shut off the cage
equalizing valves and drain the cage
before proceeding. For closed vessels,
release any pressure that may be in
the vessel before removing the sensor
assembly.
When removing the displacer from the displacer rod
or removing the controller and torque tube arm from
the cage or vessel, refer to the appropriate sensor
instruction manual for assistance. The method of
removing the displacer or torque tube arm and
attached controller will vary with the type of sensor.
For a caged sensor with top equalizing connection, it
may be appropriate to remove the entire cage from
the vessel before disassembling.