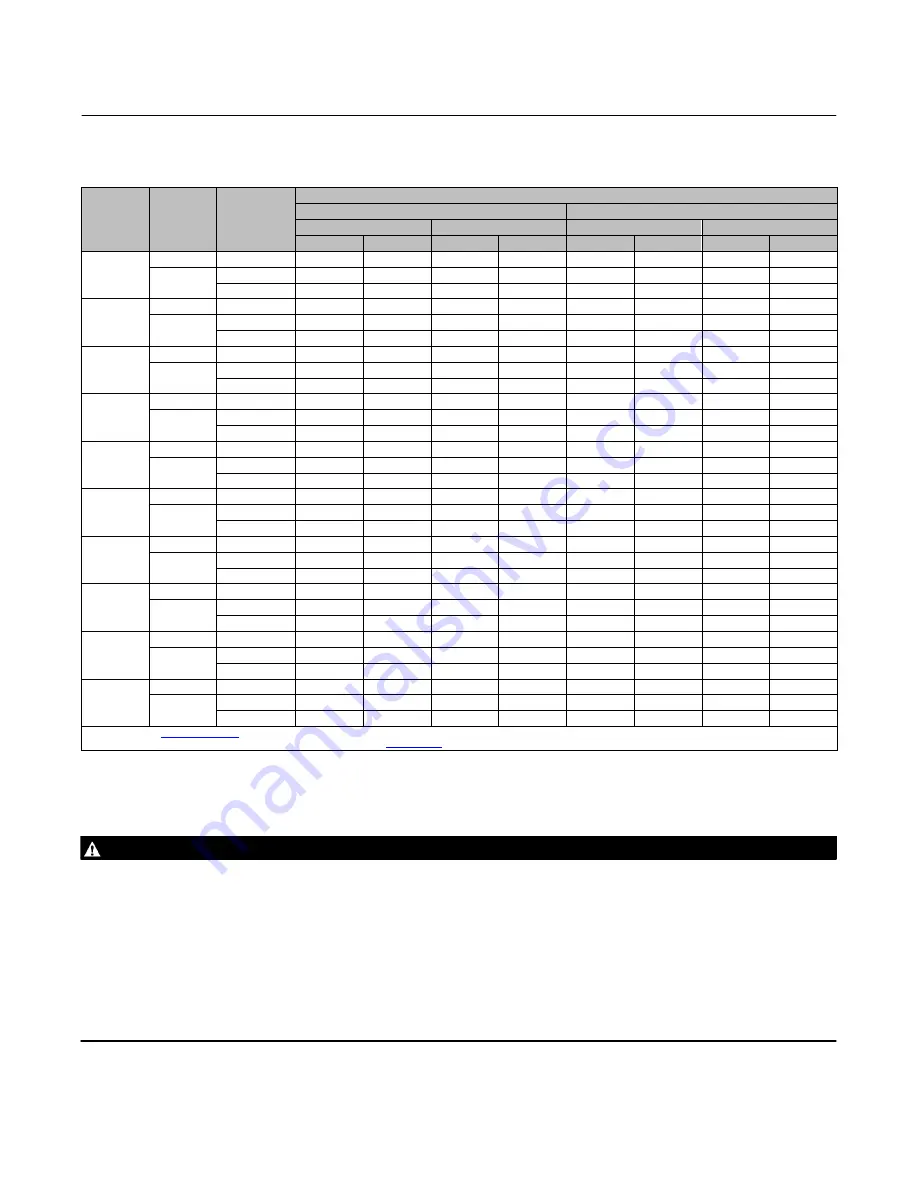
Instruction Manual
D103553X012
Large ET and ED Valves
July 2017
4
Table 2. Approximate Weights
VALVE
SIZE,
NPS
PRESSURE
CLASS
END
CONNECTION
TYPE
APPROXIMATE WEIGHT
ED/EWD and ET/EWT
ET-C/EWT-C
Short Neck
(2)
Long Neck
(2)
Short Neck
(2)
Long Neck
(2)
Kg
Lb
Kg
Lb
Kg
Lb
Kg
Lb
12
CL150-300
Flanged
950
2100
1090
2400
982
2170
1122
2470
CL600
Flanged
1270
2800
1410
3100
1302
2870
1442
3170
Buttwelding
1130
2500
1270
2800
1162
2570
1302
2870
14
CL150-300
Flanged
1130
2500
1230
2700
1162
2570
1262
2770
CL600
Flanged
1410
3100
1590
3500
1442
3170
1622
3570
Buttwelding
1180
2600
1360
3000
1212
2670
1392
3070
16x12
CL150-300
Flanged
1320
2900
1450
3200
1352
2970
1482
3270
CL600
Flanged
1680
3700
1810
4000
1712
3770
1842
4070
Buttwelding
1410
3100
1540
3400
1442
3170
1572
3470
16
CL150-300
Flanged
1720
3800
2040
4500
1752
3870
2072
4570
CL600
Flanged
2310
5100
2590
5700
2342
5170
2622
5770
Buttwelding
2090
4600
2360
5200
2122
4670
2392
5270
18
CL150-300
Flanged
2310
5100
2500
5500
2342
5170
2532
5570
CL600
Flanged
2900
6400
3130
6900
2932
6470
3162
6970
Buttwelding
2540
5600
2770
6100
2572
5670
2802
6170
20x16
CL150-300
Flanged
2500
5500
2680
5900
2532
5570
2712
5970
CL600
Flanged
3180
7000
3360
7400
3212
7070
3392
7470
Buttwelding
2770
6100
2990
6600
2802
6170
3022
6670
24x16
CL150-300
Flanged
3360
7400
3810
8400
3392
7470
3842
8470
CL600
Flanged
4260
9400
4810
10600
4292
9470
4842
10670
Buttwelding
3770
8300
4220
9300
3802
8370
4252
9370
20
CL150-300
Flanged
4122
9088
4526
9978
(1)
(1)
(1)
(1)
600
Flanged
4736
10442
5112
11269
(1)
(1)
(1)
(1)
Buttwelding
4583
10104
4808
10600
(1)
(1)
(1)
(1)
24x20
CL150-300
Flanged
5507
12140
5856
12910
(1)
(1)
(1)
(1)
600
Flanged
6796
14982
7172
15811
(1)
(1)
(1)
(1)
Buttwelding
6327
13949
6549
14437
(1)
(1)
(1)
(1)
30
CL150-300
Flanged
7390
16300
8350
18400
7535
16620
18545
18720
CL600
Flanged
(1)
(1)
(1)
(1)
(1)
(1)
(1)
(1)
Buttwelding
(1)
(1)
(1)
(1)
(1)
(1)
(1)
(1)
1. Contact your
Emerson sales office
or Local Business Partner for these weights.
2. Dependent on valve travel, refer to product bulletin 51.1:ET/ED (Large) (
D103554X012
) for addition details.
Installation
WARNING
Always wear protective gloves, clothing, and eyewear when performing any installation operations to avoid personal
injury.
Personal injury or equipment damage caused by the sudden release of pressure may result if the valve assembly is installed
where service conditions could exceed the limits given in table 1 or on the appropriate nameplates. To avoid such injury or
damage, provide a relief valve for over-pressure protection as required by government or accepted industry codes and
good engineering practices.
Check with your process or safety engineer for any additional measures that must be taken to protect against process
media.
If installing into an existing application, also refer to the WARNING at the beginning of the Maintenance section in this
instruction manual.