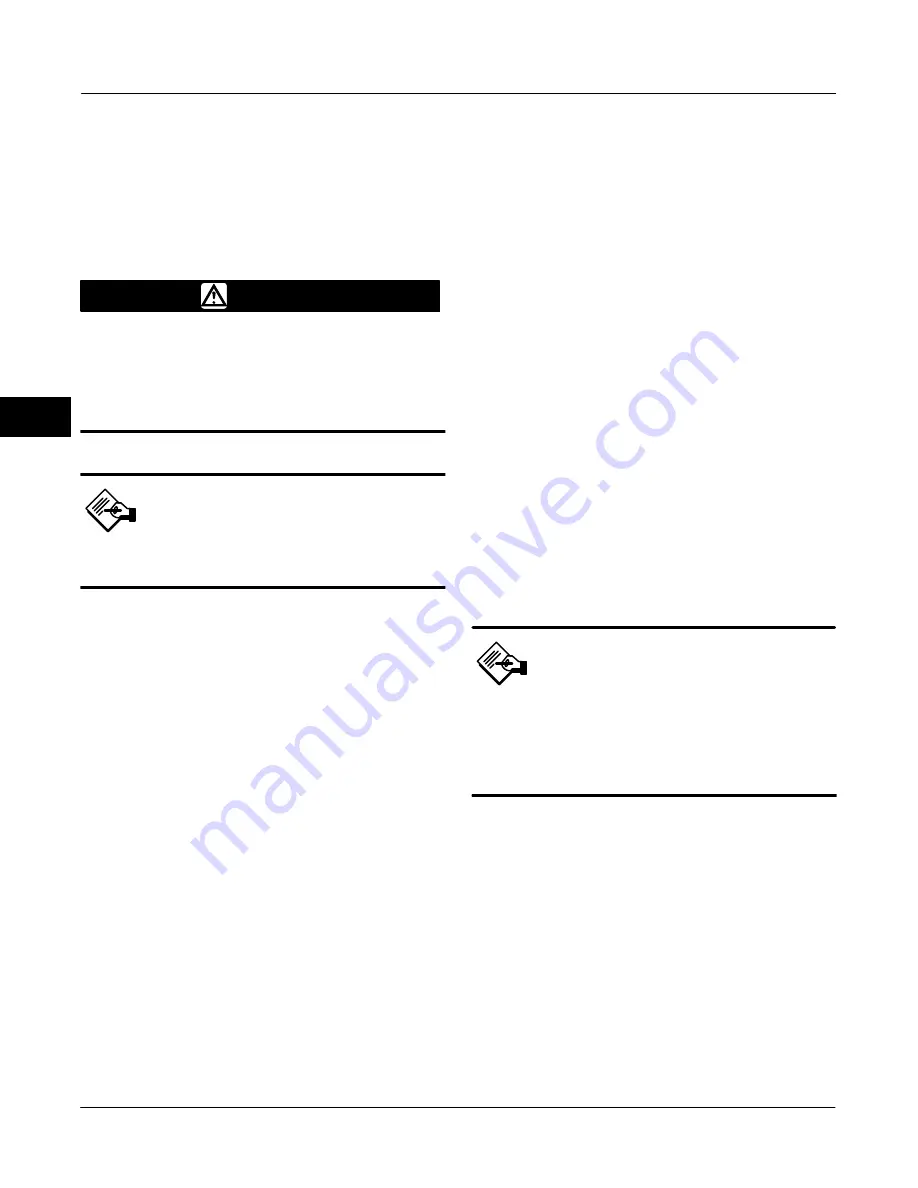
DVC6000f Digital Valve Controllers
December 2009
5-4
7. Place the Transducer Block Mode in Auto and
verify that the travel properly tracks the setpoint
changes.
Manual Calibration
(TB
>
Configure/Setup
>
Calibration
>
Manual
Calibration)
WARNING
During calibration the valve will move
full stroke. To avoid personal injury
and property damage caused by the
release of pressure or process fluid,
provide some temporary means of
control for the process.
Note
0% Travel = Valve Closed
100% Travel = Valve Open
1. From the adjustment menu, select the direction and
size of change required to adjust the output until the
valve is near mid-travel (50%). Selecting large,
medium, and small adjustments causes changes of
approximately 10.0
°
, 1.0
°
, and 0.1
°
, respectively, to
the feedback arm rotation. Selecting Next will
implement the adjustment.
If another adjustment is required, repeat step 1.
Otherwise, select Done and go to step 2.
2. If the feedback connection is SStem Roller Pot, go
to step 4.
If the feedback connection is SStem Pot, adjust the
feedback arm to the crossover point by pressing OK to
get to the adjustment menu. Continue on with step 3.
3. From the adjustment menu, select the method of
crossover; manual, last value or default. Manual
adjustment is recommended.
If you select Last Value, the crossover setting
currently stored in the instrument is used and there
are no further user interactions with the
auto-calibration routine (go to step 4). If you select
Default, an approximate value for the crossover is sent
to the instrument and there are no further user
interactions with the calibration routine (go to step 4).
If you select Manual, the Field Communicator prompts
you to adjust the arm until the feedback arm is 90
°
to
the actuator stem, as shown in figure 5-1.
If another adjustment is required, repeat step 3.
Otherwise, select Done and go to step 4.
4. From the adjustment menu, select the direction and
size of change required to set the travel to 0% (move
the valve to close).
If another adjustment is required, repeat step 4.
Otherwise, select Done and go to step 5.
5. From the adjustment menu, select the direction and
size of change required to set the travel to 100%
(move the valve to open).
If another adjustment is required, repeat step 5.
Otherwise, select Done and go to step 6.
6. Enter the name of the person performing the
calibration procedure.
7. Enter the location of the calibration procedure.
8. Enter the date of the calibration procedure.
9. Place the Transducer Block Mode in Manual and
verify that the travel properly tracks the setpoint
changes.
Relay
(TB
>
Configure/Setup
>
Calibration
>
Relay)
Note
Relay B and C are not user-adjustable.
For relay A it is recommended that you
check the relay adjustment for
double-acting installations before
proceeding with travel calibration.
Double-Acting Relay
The double-acting relay is designated by “Relay A” on
a label affixed to the relay itself. For double-acting
actuators, the valve must be near mid-travel to
properly adjust the relay. The Field Communicator will
automatically position the valve when Relay Adjust is
selected.
Rotate the adjustment disc, shown in figure 5-2, until
the output pressure displayed on the Field
Communicator is between 50 and 70% of supply
pressure. This adjustment is very sensitive. Be sure to
allow the pressure reading to stabilize before making
another adjustment (stabilization may take up to 30
seconds or more for large actuators).
5
Summary of Contents for Fisher FIELDVUE DVC6000f
Page 54: ...DVC6000f Digital Valve Controllers December 2009 2 30 2 ...
Page 62: ...DVC6000f Digital Valve Controllers December 2009 4 2 4 ...
Page 127: ...Transducer Block December 2009 4 67 4 ...
Page 141: ...AO Function Block December 2009 4 81 4 ...
Page 207: ...MAI Function Block December 2009 4 147 4 ...
Page 219: ...DO Function Block December 2009 4 159 4 ...
Page 231: ...DI Function Block December 2009 4 171 4 ...
Page 302: ...DVC6000f Digital Valve Controllers December 2009 8 16 8 ...
Page 306: ...DVC6000f Digital Valve Controllers December 2009 A 4 A ...
Page 350: ...DVC6000f Digital Valve Controllers December 2009 E 6 E ...
Page 368: ...DVC6000f Digital Valve Controllers December 2009 F 18 F ...
Page 372: ...DVC6000f Digital Valve Controllers December 2009 Glossary 4 Notes G Glossary ...
Page 382: ...DVC6000f Digital Valve Controllers December 2009 Index 10 F Index ...