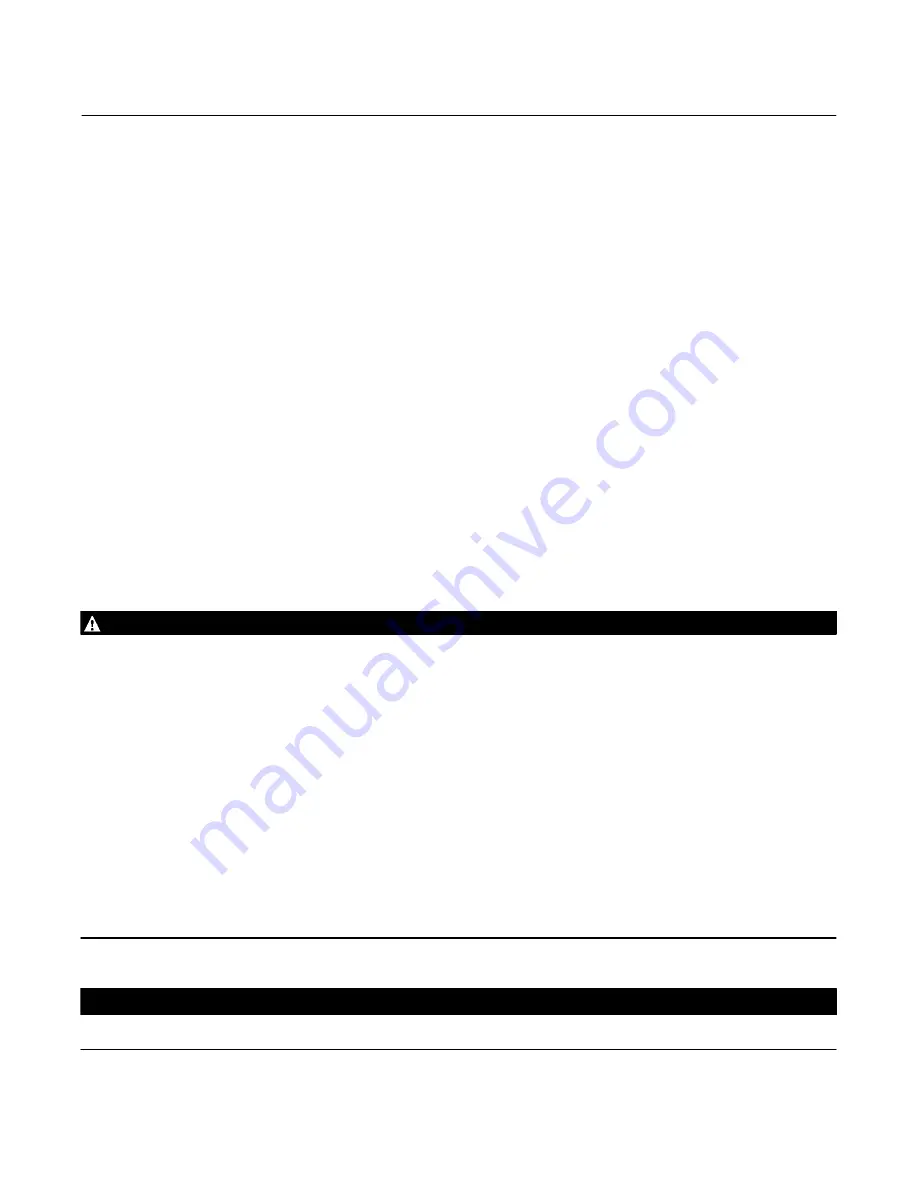
Instruction Manual
D100399X012
EW Valve
July 2017
7
2. Provide adequate support to the bonnet while removing the bonnet nuts.
3. Be aware that the bonnet/plug/cage may tip over as they are lowered from the valve body. Make provision to
prevent tipping.
4. Be aware that the cage and seat ring may not come out with the bonnet and plug/stem assembly. If this occurs,
make provision to support these parts, as they may fall out unexpectedly.
Assembly
1. Start this assembly procedure with the plug/stem assembly already installed in the bonnet.
2. Put the gaskets and cage onto the bonnet and plug.
3. Place the seat ring with the seat ring gasket onto the cage, if applicable with the valve design.
4. Raise this bonnet/plug/cage assembly up into the valve body. Make provision to prevent tipping of these parts as
they are being raised into the valve body.
5. Torque the bonnet nuts.
6. Mount the actuator.
Maintenance
Valve parts are subject to normal wear and must be inspected and replaced as necessary. Inspection and maintenance
frequency depends on the severity of service conditions. This section includes instructions for packing lubrication,
packing maintenance, trim maintenance, lapping metal seats, and ENVIRO‐SEAL bellows seal bonnet replacement. All
maintenance operations may be performed with the valve in the line.
WARNING
Avoid personal injury or property damage from sudden release of process pressure. Before performing any maintenance
operations:
D
Do not remove the actuator from the valve while the valve is still pressurized.
D
Always wear protective gloves, clothing, and eyewear when performing any maintenance operations to avoid personal
injury.
D
Disconnect any operating lines providing air pressure, electric power, or a control signal to the actuator. Be sure the
actuator cannot suddenly open or close the valve.
D
Use bypass valves or completely shut off the process to isolate the valve from process pressure. Relieve process pressure
on both sides of the valve. Drain the process media from both sides of the valve.
D
Vent the pneumatic actuator loading pressure and relieve any actuator spring precompression.
D
Use lock‐out procedures to be sure that the above measures stay in effect while you work on the equipment.
D
The valve packing box may contain process fluids that are pressurized,
even when the valve has been removed from the
pipeline.
Process fluids may spray out under pressure when removing the packing hardware or packing rings, or when
loosening the packing box pipe plug.
D
Check with your process or safety engineer for any additional measures that must be taken to protect against process
media.
CAUTION
Follow instructions carefully to avoid damaging the product surfaces, which could result in damage to the product.