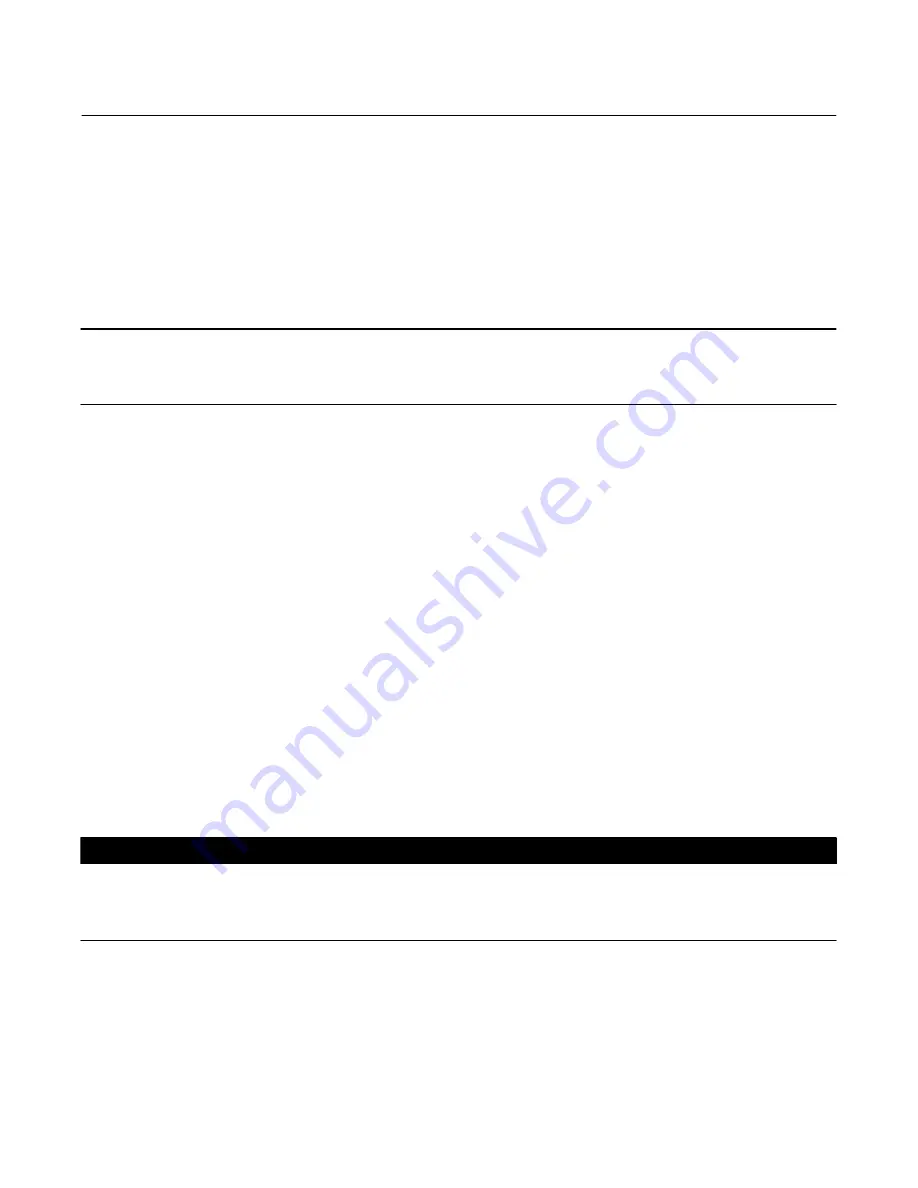
Instruction Manual
D104727X012
DSV1000 Valve
June 2022
9
3. Mark parts as necessary to allow them to be returned to the same position during re‐assembly.
4. Refer to the appropriate actuator instruction manual for information on removal. Loosen the actuator mounting
screws, bolts, or nuts while properly supporting the actuator then separate the actuator and mounting bracket
from the valve. When valve maintenance is complete, refer to the Mounting Actuator procedure in this manual to
reinstall the actuator on the valve.
5. Provide a clean soft working surface to protect the tailpiece‐flange serrated surface. Lift the valve and place it on
either tailpiece flange face. Be sure the valve is in a stable, upright position before releasing the hoist connection.
Note
If the packing is in good condition, it is possible to remove and replace the seal assembly without removing the packing box
assembly. However, the packing box assembly must be removed to remove the ball (key 3) from the valve body.
6. Remove the packing box housing socket head cap screws (key 10).
a. If necessary, two packing box housing cap screws can be used as jack bolts to assist with separating the packing
box housing assembly from the valve.
b. Remove the two plastic plugs (key 39) from the packing box housing and install two packing box housing cap
screws until contact with the body occurs. Alternately and evenly, turn each fastener clockwise until the packing
box housing assembly is adequately separated from the valve body. Remove the packing box housing assembly
from the valve body. The packing box housing assembly includes all packing parts, drive shaft (key 4), O‐ring seal
(key 14), drive shaft bushing (key 8), and thrust washer (key 9). The two straight pins (key 7) may stay attached
to the packing box.
c. If necessary, use a punch and drive each straight pin towards the valve side of the packing box to remove.
7. If it is desired to separate the packing box assembly parts, loosen or remove the packing components and slide the
shaft down and out the valve side of the packing box. Inspect the drive shaft bushing (key 8) and the thrust washer
(key 9). If necessary, replace worn components.
8. Remove the heavy hex nuts (key 21) from the studs, if applicable, remove base brackets (key 25), and lift the upper
tailpiece from the body. If studs (key 19 and 20) are removed from the valve body, mark installed locations of long
studs (key 20) in valve body.
NOTICE
While lifting the tailpiece (key 2) from the valve body, check to see if the seal (key 5) is lifting with the tailpiece. If so, use
caution in case the seal falls out and protect the ball's spherical surface. An additional strap can be employed to ensure the
seal stays in place.
9. Turn the tailpiece assembly over so the seal is facing up, and place it on a clean soft surface to protect the flange
serrated surface. Note the tailpiece O-ring (key 13).
10. Lift the seal out of the tailpiece. Note the seal O-ring and back up ring (keys 15 and 16) and the multitude of springs
(key 18). Ensure all springs and the bearing plate dowel pins (key 22) are accounted for. Clean and protect all sealing
surfaces.