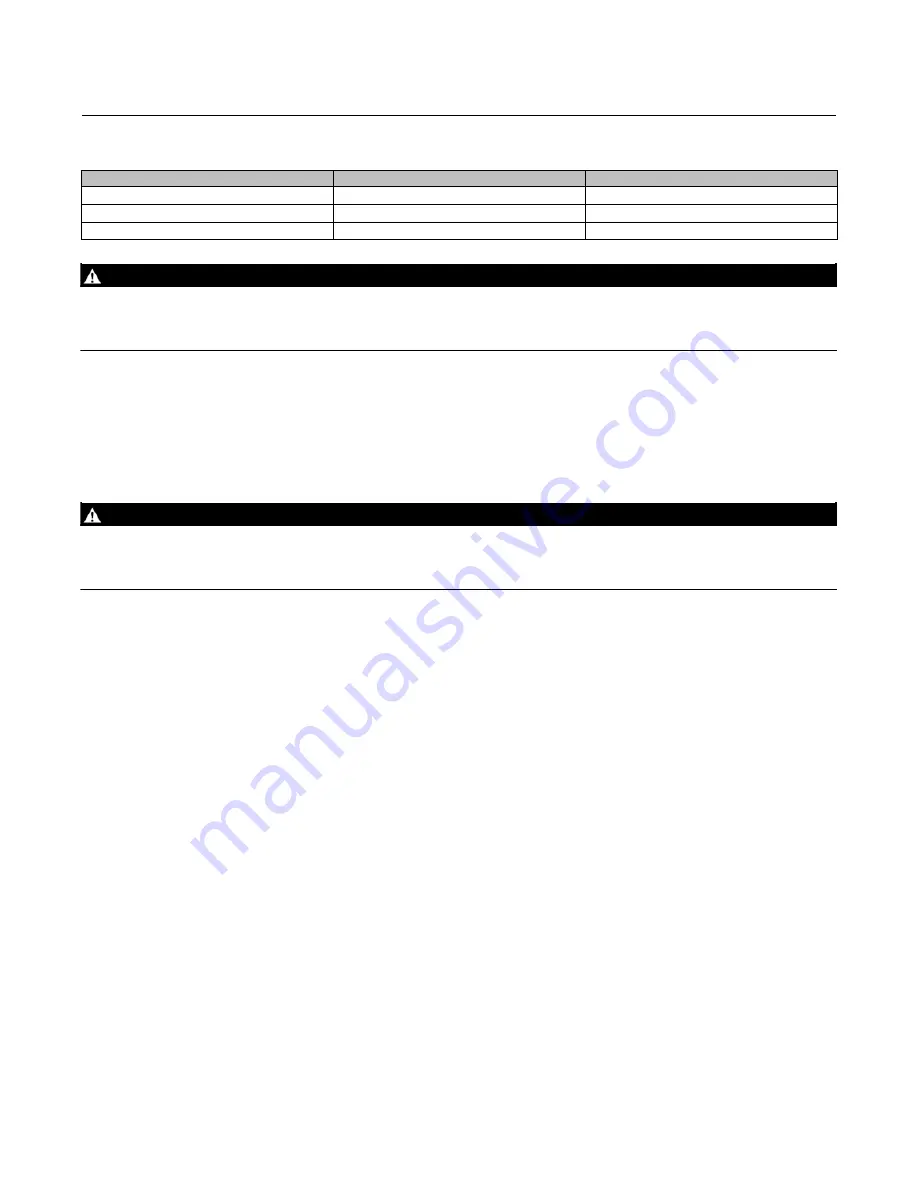
Instruction Manual
D103643X012
DFA Desuperheater
August 2013
5
Table 6. Fisher DFA Minimum Mounting I.D.
MINIMUM BODY FLANGE
NOZZLE MODEL
MINIMUM MOUNTING I.D.
3
DFA- A,B,C
2.624
3
DFA- D, E
2.9
4
DFA- A through H
4
WARNING
When ordered, the desuperheater configuration and construction materials were selected to meet particular pressure,
temperature, pressure drop, and fluid conditions. Do not apply any other conditions to the desuperheater without first
contacting your Emerson Process Management sales office.
1. Mount the DFA desuperheater in a “Tee” piece at the desired location in the pipe, in accordance with standard
piping practice. The nozzle should be positioned in the top quadrant of the pipe (see figure 3 for the proper “T”
length dimension).
2. Clean and flush out the cooling water line before connecting to the desuperheater. Use only clean sources of
cooling water. Use of clean water decreases wear and prevents clogging of the nozzle by solid particles.
WARNING
Personal injury or property damage could result from clogging of the desuperheater. Installation of a strainer and an
isolating valve on the water line between the desuperheater and the water control valve is recommended. Failure to do so
may result in clogging of the desuperheater by solid particles, thus hampering temperature control of the steam.
3. A minimum straight run of pipe is required downstream of the desuperheater to ensure complete vaporization of
cooling water. Consult the desuperheater certified drawing for the required distance of straight pipe.
4. The temperature sensor should be mounted according to the manufacturer's instructions. Typical distance to the
sensor is at least 9.1 meters (30 feet) downstream of the desuperheater. This distance changes with higher velocity
steam flow and the percentage of spraywater required. Consult the desuperheater certified drawing for this
distance.
5. There should be no branching out from or into the steam line to divide the steam flow between the temperature
sensor and the desuperheater.
6. A typical installation is illustrated in figure 6. A temperature sensor element (TE) measures changes in temperature
and transmits a signal to a remote temperature-indicating controller (TC) or distributed control system (DCS). The
output signal from the controller is sent to the positioner on the spraywater control valve. The positioner output
signal is piped to the actuator. The actuator strokes the stem/plug of the spraywater control valve, as required, to
supply the required cooling water to the desuperheater to maintain temperature setpoint.