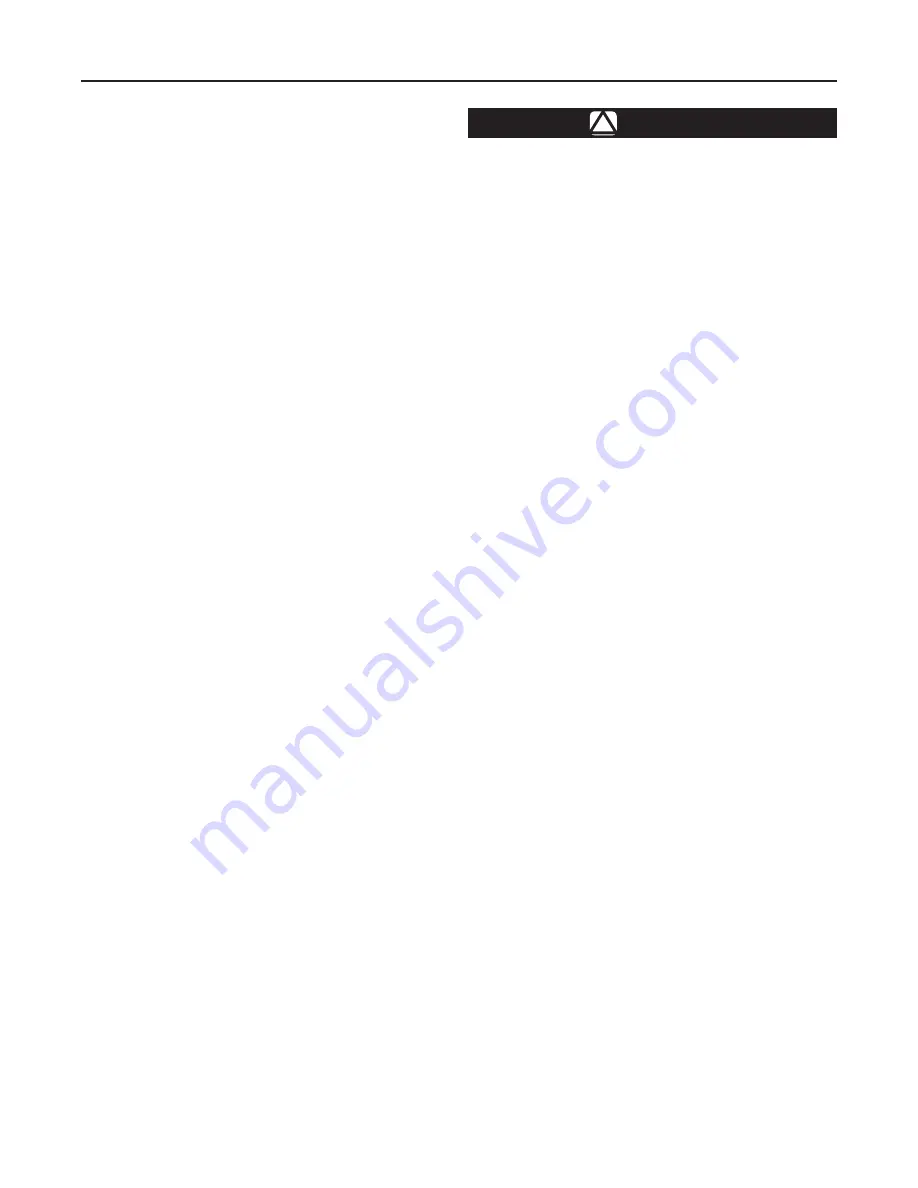
67D Series
5
Inspect the vent hole regularly to make sure it is
not plugged. Spring case vent hole orientation may
be changed by rotating the spring case with
respect to the body. A 1/4 NPT spring case vent
may be remotely vented by installing obstruction-
free tubing or piping into the vent. Protect the
remote vent by installing a screened vent cap on
the remote end of the vent pipe.
5. For use in regulator shutdown, install upstream
block and vent valves and downstream block
and vent valves (if required), or provide some
other suitable means of properly venting the
regulator inlet and outlet pressures. Install a
pressure gauge to monitor instruments on startup.
6. Apply a good grade of pipe compound to the external
pipe threads before making connections, making sure
not to get the pipe compound inside the regulator.
7. Install tubing fitting or piping into the 1/2 NPT
inlet connection on the body (key 1) and into the
1/2 NPT body outlet connection.
8. The two 1/4 NPT outlets can be used for a gauge
or other use. If not used, they must be plugged.
overpressure Protection
The 67D Series regulators have maximum outlet
pressure ratings that are lower than their maximum
inlet pressure ratings. A pressure-relieving or pressure-
limiting device is needed if inlet pressure can exceed
the maximum outlet pressure rating.
Types 67DR, 67DSR, 67DFR, and 67DFSR have
a low capacity internal relief valve for minor seat
leakage only. Other overpressure protection must be
provided if the maximum inlet pressure can exceed
the maximum pressure rating of the downstream
equipment or exceeds the maximum outlet pressure
rating of the regulator.
Startup and adjustment
Key numbers are referenced in Figures 3 through 8.
1. With proper installation completed and downstream
equipment properly adjusted, slowly open the
upstream and downstream block valve (when
used) while using pressure gauges to monitor pressure.
!
WaRning
To avoid personal injury, property
damage, or equipment damage caused
by bursting of pressure-containing parts
or explosion of accumulated gas, never
adjust the control spring to produce an
outlet pressure higher than the upper
limit of the outlet pressure range for that
particular spring. if the desired outlet
pressure is not within the range of the
control spring, install a spring of the
proper range according to the diaphragm
parts maintenance procedure.
2. If outlet pressure adjustment is necessary,
monitor outlet pressure with a gauge during the
adjustment procedure. The regulator is adjusted
by loosening the locknut (key 19), if used, and
turning the adjusting screw or handwheel (key 18)
clockwise to increase or counterclockwise to
decrease the outlet pressure setting. Retighten the
locknut to maintain the adjustment position.
Shutdown
First, close the nearest upstream block valve and
then close the nearest downstream block valve
(when used). Next, open the downstream vent valve.
Since the regulator remains open in response to the
decreasing downstream pressure, pressure between
the closed block valves will be released through the
open vent valve.
Maintenance
Regulator parts are subject to normal wear and
must be inspected and replaced as necessary. The
frequency of inspection and replacement of parts
depends on the severity of service conditions and
applicable codes and government regulations. Open
the Type 67DF, 67DFR, 67DFS, or 67DFSR drain valve
(key 2) regularly to empty accumulated liquid from the
dripwell (key 5).
note
if sufficient clearance exists, the body
(key 1) may remain mounted on other
equipment or in a line or panel during
maintenance unless the entire regulator
will be replaced.