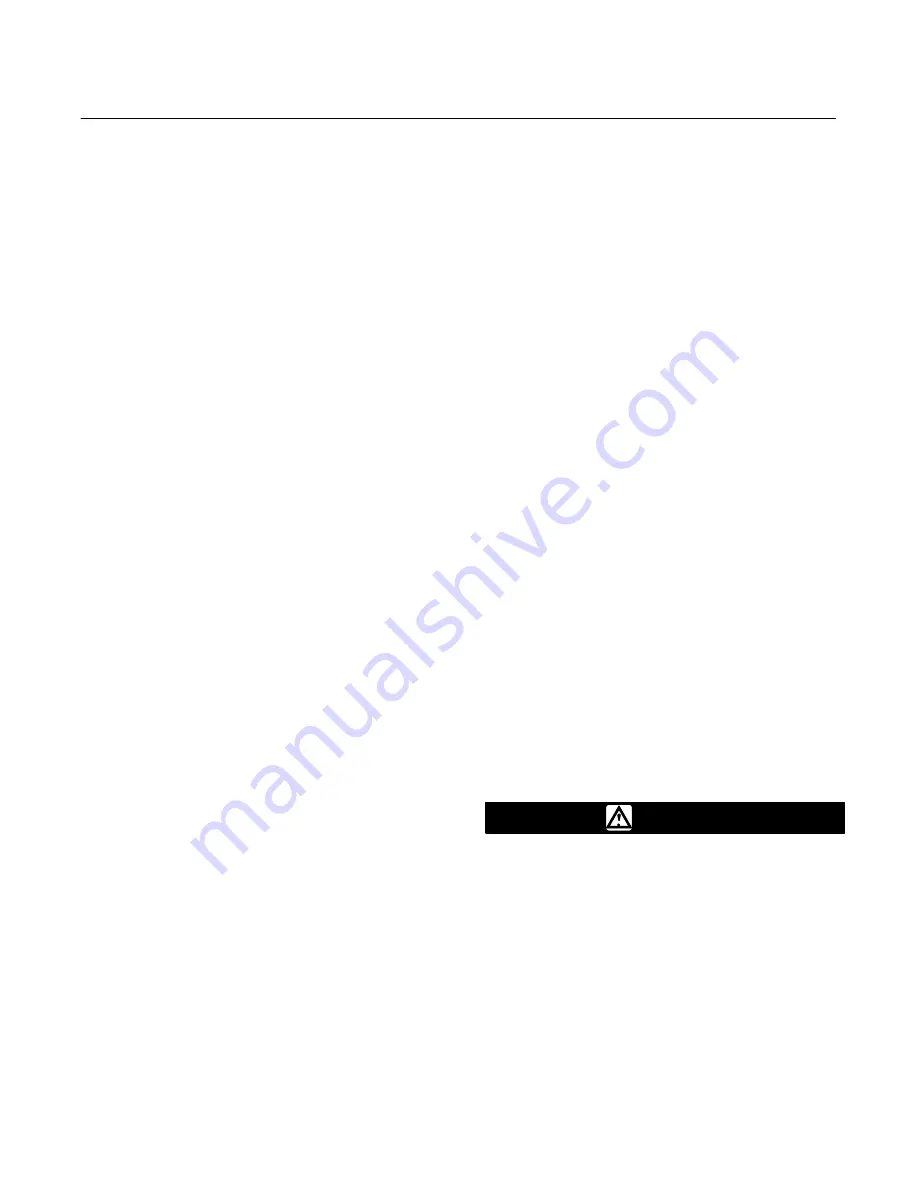
4660 Pressure Pilot
Instruction Manual
Form 5200
September 2004
6
Actuator Mounting
Pilots specified for mounting on a control valve
actuator are normally mounted at the factory. If the
pilot is ordered separately for installation on a control
valve actuator, mount the unit as described in the
appropriate portion of this section.
To yoke-mount the pilot to an actuator, attach the
two-holed side of the yoke mounting plate (key 75,
not shown) to the spring barrel of the actuator with
cap screws and lockwashers (keys 84 and 85, not
shown). Then attach the three-bossed side of the
pilot case (key 2) to the three-holed side of the yoke
mounting plate with the remaining cap screws and
lock washers.
To mount the pilot to the diaphragm casing of an
actuator, attach the two-holed side of the casing
mounting plate (key 75, not shown) to the diaphragm
casing of the actuator with the actuator cap screws
and nuts. Then attach the three-bossed side of the
pilot case (key 2) to the three-holed side of the
casing mounting plate with cap screws and lock
washers (keys 84 and 85, not shown).
Panel Mounting
If the pilot is not already equipped with a panel
mounting plate (key 75), remove the cover screws
(key 6), the cover (key 4), and the screws (key 21).
For pilots without set point indication, loosen the set
screws and remove the knobs (key 67), the locking
disks (key 69), and the front plate (key 74). Insert the
panel mounting plate, and reattach the front plate,
the locking disks, the knobs, the cable assembly
(key 12), the screws, the cover, and the cover
screws.
For pilots with set point indication, loosen the
module set screws, and remove the modules and
the front plate (key 74). Insert the panel mounting
plate, and reattach the front plate, the modules, the
cable assembly (key 12), the screws, the cover, and
the cover screws.
Choose the panel mounting style required to allow
for either front or rear removal of the pilot from the
panel. Cut a hole in the panel surface and drill
mounting screw holes using the dimensions shown
in figure 3.
Note
For either mounting style, the process,
output, and supply pressure fittings
may be attached to the pilot prior to
sliding the pilot into the cutout. Also,
these fittings do not need to be
detached from the pilot when
removing the pilot from the panel.
Peel off the backing on the panel mount gasket.
Apply pressure to the gasket surface to adhere the
gasket to the face of the panel. Slide the pilot into
the cutout from the front or rear side of the panel and
attach the panel mounting plate to the panel.
Pipestand Mounting
Pipestand mounting parts are available to mount the
pilot to a 2-inch (nominal) horizontal or vertical pipe.
Attach the three-bossed side of the pilot case (key 2)
to the three-holed side of the pipestand mounting
plate (key 75, not shown) with cap screws and lock
washers (keys 84 and 85, not shown). Then attach
two pipe clamps (key 86, not shown) to the
pipestand mounting plate, and fasten the pilot to the
pipe.
Pressure Connections
Standard pressure connections on the Type 4660
pilot are 0.25 inch NPT female. Use 0.25 or
0.375 inch pipe or tubing for process, output, and
supply pressure piping. The locations of pressure
connections are shown in figure 4. The vent location
is shown in figure 8.
Supply Pressure
WARNING
Severe personal injury or property
damage may occur from an
uncontrolled process if the instrument
supply medium is not clean, dry,
oil-free and non-corrosive. While use
and regular maintenance of a filter that
removes particles larger than 40
microns in diameter will suffice in
most applications, check with a Fisher
Field office and Industry Instrument air
quality standards for use with
corrosive gas or if you are unsure
about the proper amount or method of
air filtration or filter maintenance.