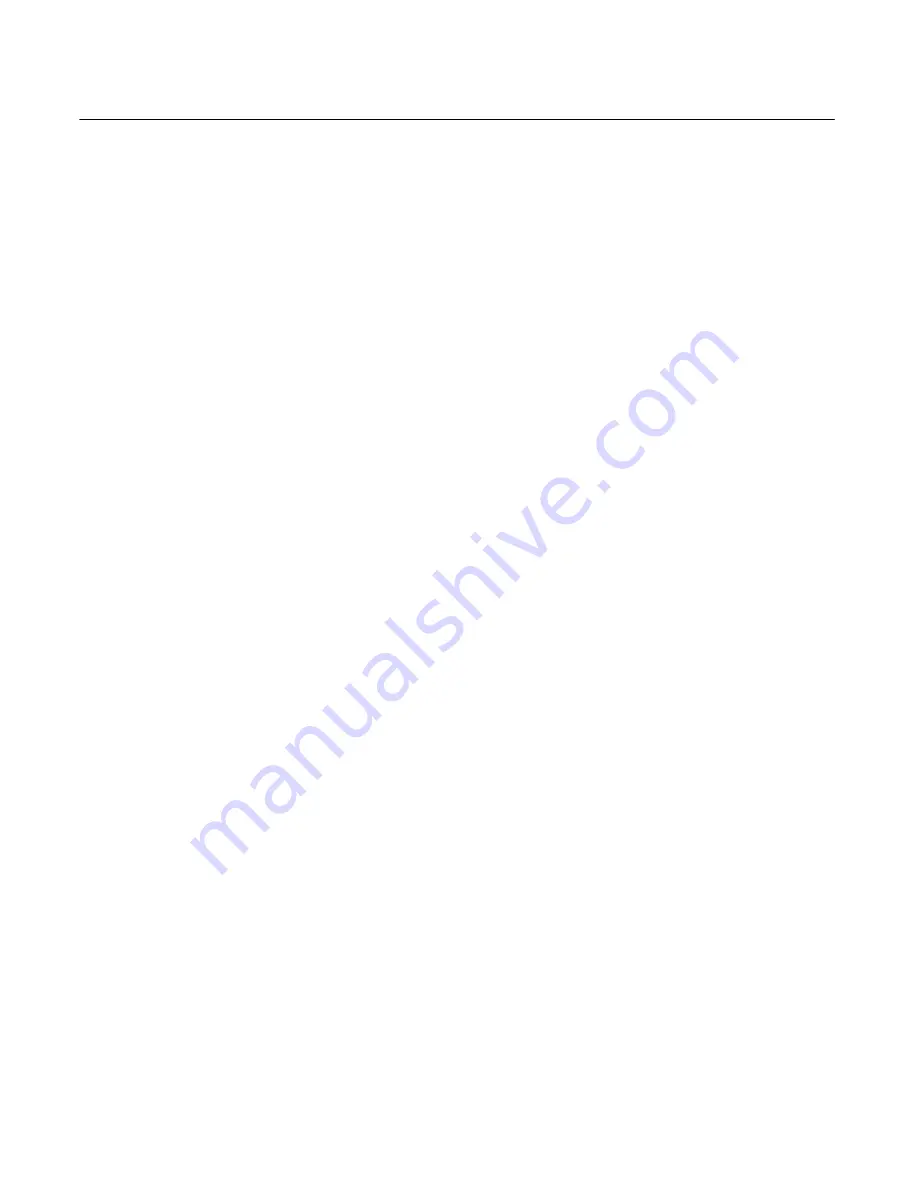
4200 Series Transmitters
Instruction Manual
Form 5596
November 2006
13
must be with a meter approved for
hazardous areas.
Refer to figure 5 for component locations.
1. Remove power from the instrument.
2. Connect the digital voltmeter (DVM) leads as
follows:
a. For all transmitters (except a Type 4212 or
4222) connect between TP3 (+) and TP4 (
−
) on
the printed wiring board.
b. For a Type 4212 or 4222 transmitter, connect
the DVM between TP5 (+) and TP6 (
−
).
3. Loosen the appropriate set screw connecting the
potentiometer shaft to the linkage:
a. For sliding stem applications, loosen the set
screw (key 26, figure 15) in the operating arm
(key 30) on the potentiometer shaft.
b. For rotary actuator applications, loosen the set
screw in the coupling (key 50, figure 19) on the
potentiometer shaft.
c. For long stroke applications, leave the coupler
(key 100E) rigidly attached to the potentiometer
shaft. Loosen only the coupling screw (key 100F,
figures 22 and 23) in the coupler (key 100E) on
the transducer shaft.
4. Stroke the actuator or other device to the
mid-stroke position.
Note
On units with position switches, the
(R) terminal on TB3 must be connected
to the power supply negative (
−
)
terminal as shown in figure 9 to attain
correct potentiometer alignment.
5. Apply power to the instrument.
6. While the device is in mid-stroke position, insert a
screwdriver blade into the slot in the end of the
potentiometer shaft (see figure 15), or turn the
coupler (key 52, figure 19 or key 100E, figures 22
and 23) to turn the potentiometer shaft until the DVM
reads 1.25
±
0.05 volts dc. This establishes the
electrical center of the potentiometer.
7. Tighten the appropriate set screw. Check that the
DVM reading has remained at 1.25
±
0.05 volts dc.
Note
For sliding stem applications, tighten
the set screw (key 26, figure 15) in the
operating arm (key 30) to a torque of
3.39 to 3.95 N
S
m (30 to 35 lbf
S
in).
8. Remove the power from the transmitter power
supply.
9. Remove the DVM leads from TP3 and TP4
(transmitter signal) or TP5 and TP6 (position switch
signal).
10. Refer to the direct or reverse action procedures.
Direct or Reverse Action
Direct action means, when looking at the slotted end
of the potentiometer shaft, a clockwise rotation of the
shaft produces an increasing output signal from the
transmitter.
Reverse action means, when looking at the slotted
end of the potentiometer shaft, a clockwise rotation
of the shaft produces a decreasing output signal
from the transmitter.
The transmitter produces a direct or reverse action
output signal depending on the location of the
potentiometer wires inserted in terminal block
number 1 (TB1) mounted on the transmitter printed
wiring board. Refer to figure 6 for the location of the
wires and the wire color sequence for direct action.
For reverse action, exchange the positions of the
brown and red wires.
Arrange wires on the terminal block (TB1) for either
direct or reverse action to match the application
requirements; then repeat the potentiometer
alignment procedures.
Refer to the Calibration section to adjust the zero
and span of the transmitter and/or position switch
circuits.
Operating Information
Initial Considerations
If the transmitter is ordered with an actuator, the
transmitter is factory calibrated to the length of travel
specified on the order. If the transmitter is ordered
separately, adjust the zero and span as described in
the Calibration section so that the transmitter
operates properly in your specific application.