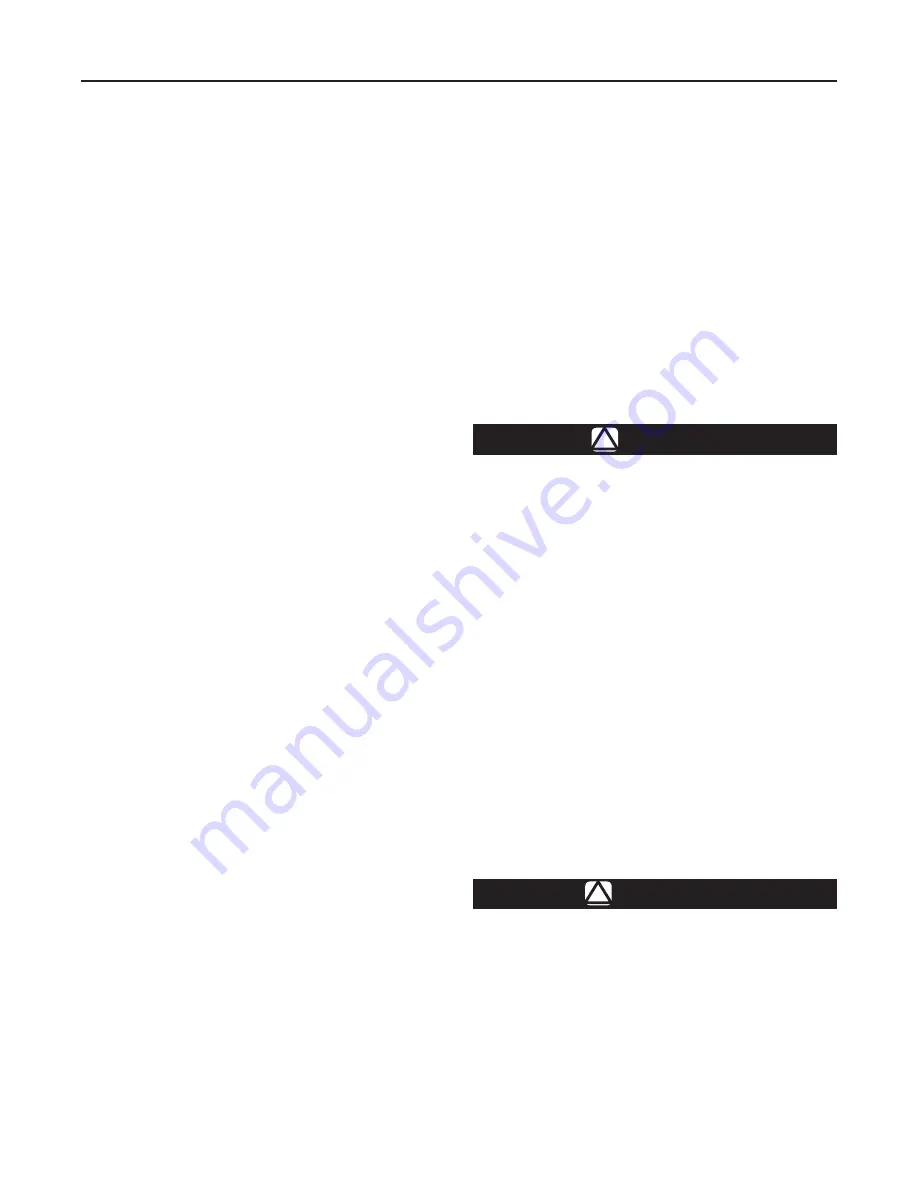
299H Series
10
Note
The regulator body may remain in the
pipeline during maintenance procedures.
Main Actuator Diaphragm
Follow this procedure to change the actuator
diaphragm or to inspect, clean or replace any other
parts in the main actuator. Part key numbers are
referenced in Figures 5 and 6.
1. Cut the wire seal (key 68) (being careful not to
lose the warning tag) and remove the closing cap
(key 3). Inspect the O-ring (key 9) and replace
if necessary.
2. Carefully loosen and remove the double nuts
(key 5) on the actuator diaphragm post (key 10).
When removing the adjusting nuts, do not twist
or unscrew the diaphragm post, as this action will
loosen the joint between the diaphragm post and
the pusher post (keys 10 and 11).
3. Remove the spring seat (key 4) and closing spring
(key 6).
4. Remove the eight hex head cap screws (key 23)
and lift off the upper casing (key 2).
5. Remove the diaphragm assembly (key 8) by
tipping it so that the lever (key 26) slips out of the
pusher post (key 11).
6. Separate the diaphragm assembly by unscrewing
the diaphragm post (key 10) from the pusher
post (key 11) and remove the diaphragm post,
pressure equalization spring (key 7), diaphragm
head (key 81), diaphragm (key 8), the second
diaphragm head (key 81) and diaphragm pad
(key 80). Inspect the diaphragm parts for damage
and replace if necessary.
7. Inspect the lever (key 26) and replace if necessary.
To replace the valve stem (key 16), also perform
Main Body Valve Disk and Orifice maintenance
procedure steps 1, 2 and 3, remove disk (key 13)
and pull the stem out of the lower casing assembly
(key 1). Lightly lubricate the replacement stem
O-ring (key 14) and install it on the valve stem.
Reinstall the valve stem into the lower casing
assembly. Reinstall the body (key 17) or continue
with the reassembly of the diaphragm.
Note
When assembling the diaphragm assembly
(keys 8, 80 and 81), lubricate the actuator
diaphragm post (key 10) threads.
8. Loosely reassemble the diaphragm and diaphragm
post parts so that the bolt holes in the diaphragm
align with the corresponding holes in the lower
casing (key 1) when the lever (key 26) is fitted
properly into the pusher post. When this orientation
is made, tighten the diaphragm post into the pusher
post (keys 10 and 11).
9. Reinstall the diaphragm assembly using the
reverse order of step 5.
10. Install the upper casing (key 2) and secure it to the
lower casing (key 1) with the eight hex head screws
(key 23). Tighten the hex head screws evenly using
a crisscross pattern to avoid placing an uneven
strain on the regulator. Tighten the screws to a final
bolt torque of 10 to 13 foot-pounds / 13 to 17 N•m
to avoid crushing the diaphragm.
CAUTION
In step 11, the spring seat (key 4) is
under spring pressure. Use constant
hand pressure to hold the spring down
when installing the hex nuts (key 5), see
Figure 5.
11. Install the closing spring (key 6) and the spring seat
(key 4). Push and hold down on the spring seat,
cocking it to one side until the seat catches onto the
threads of the diaphragm post (key 10). Then, pull
up on the diaphragm post allowing access to the
post threads so that the two adjusting hex nuts
(key 5) can be installed. Install the adjusting hex
nuts as shown in Figure 5. The closing spring must
be adjusted down to a depth of 1/2-inch / 13 mm
from the top of the upper case opening to the top
of the spring seat. When tightening the two hex
nuts, use care not to rotate the diaphragm post,
which may damage the post.
12. Lightly lubricate the O-ring (key 9) on the closing
cap and reinstall the closing cap (key 3).
WARNING
!
The wire seal and warning tag (keys 68
and 69) contain important safety
information, make sure they are attached
when maintenance is completed.
13. Install the wire seal and warning tag (keys 68
and 69).