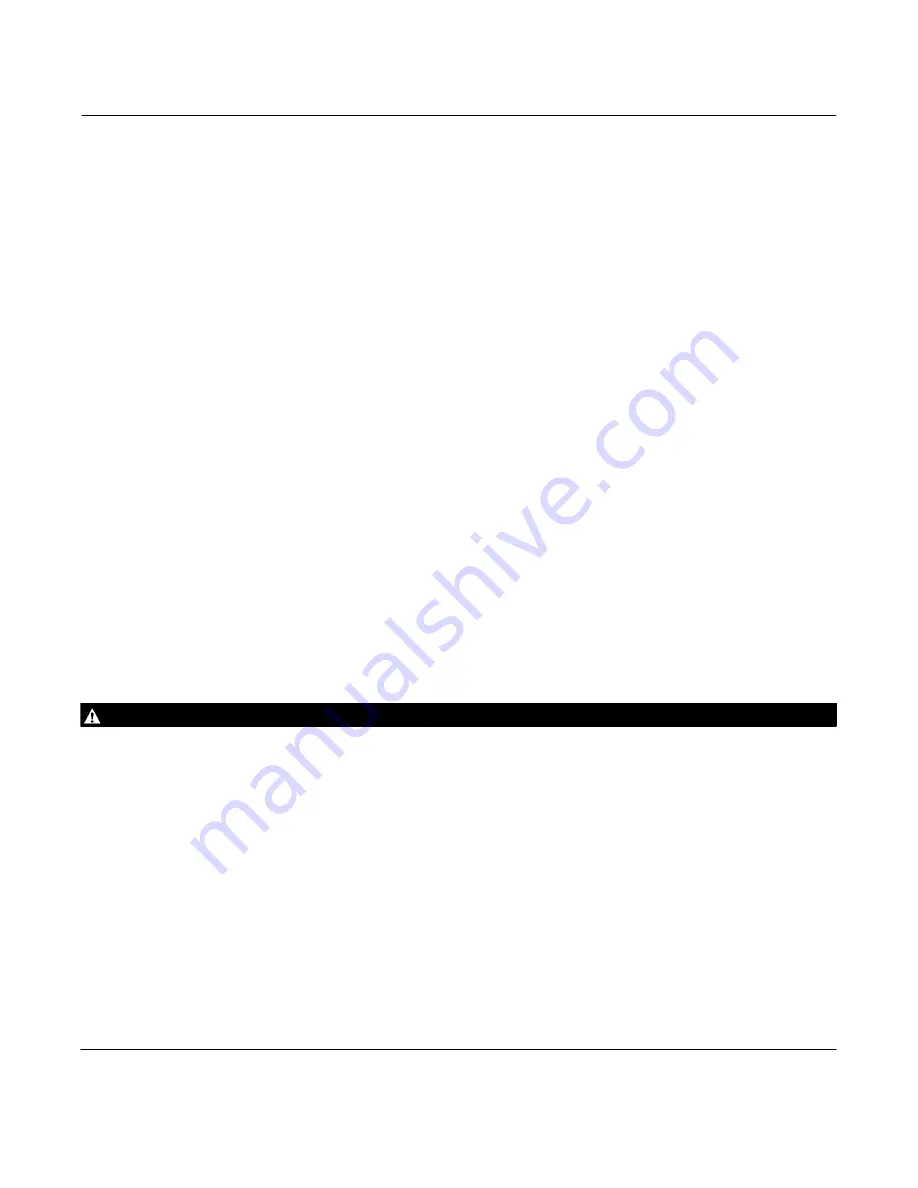
Instruction Manual
D100333X012
1069 Actuator
April 2018
8
3. When either position is obtained, rotate the appropriate travel stop screw into the housing (key 15) until contact
with the lever (key 19) is felt. Make sure the travel stop screw is snug against the lever.
4. Tighten the appropriate hex nut to lock the travel stop screw in position.
5. To complete the adjustment, repeat this procedure on the remaining travel stop screw.
Principle of Operation
Individual piston movement is accomplished by loading air pressure on one side of the piston and unloading air
pressure from the other side of the piston. In the 1069 actuator, one piston moves upward while the other piston
moves downward, or vice versa, to provide a rotary torque output that either opens or closes the valve body.
If a positioner is not used with the control valve assembly, a loading device such as a four‐way switching valve must be
provided. The loading device is not furnished with the actuator.
If a positioner is used with the control valve assembly, only one positioner is required to control both actuator pistons.
The positioner should be connected in series to both actuator cylinders. Consult the positioner instruction manual for
actuator principle of operation with positioner.
Maintenance
Actuator parts are subject to normal wear and must be inspected and replaced as necessary. The frequency of
inspection and replacement depends upon the severity of service conditions. This section provides procedures for
both disassembly and assembly of parts. Key numbers referenced in these procedures are shown in figure 4, unless
otherwise specified.
WARNING
Sudden release of pressure or uncontrolled process fluid can occur when repair work is done. To avoid personal injury or
damage to the process system, perform the following before starting maintenance operations:
D
Do not remove the actuator from the valve while the valve is still pressurized.
D
Always wear protective gloves, clothing, and eyewear when performing any maintenance operations to avoid personal
injury.
D
Disconnect any operating lines providing air pressure, electric power, or a control signal to the actuator. Be sure the
actuator cannot suddenly open or close the valve.
D
Use bypass valves or completely shut off the process to isolate the valve from process pressure. Relieve process pressure
on both sides of the valve. Drain the process media from both sides of the valve.
D
Vent the power actuator loading pressure and relieve any actuator spring precompression.
D
Use lock‐out procedures to be sure that the above measures stay in effect while you work on the equipment.
D
The valve packing box may contain process fluids that are pressurized,
even when the valve has been removed from the
pipeline.
Process fluids may spray out under pressure when removing the packing hardware or packing rings, or when
loosening the packing box pipe plug.
D
Check with your process or safety engineer for any additional measures that must be taken to protect against process
media.