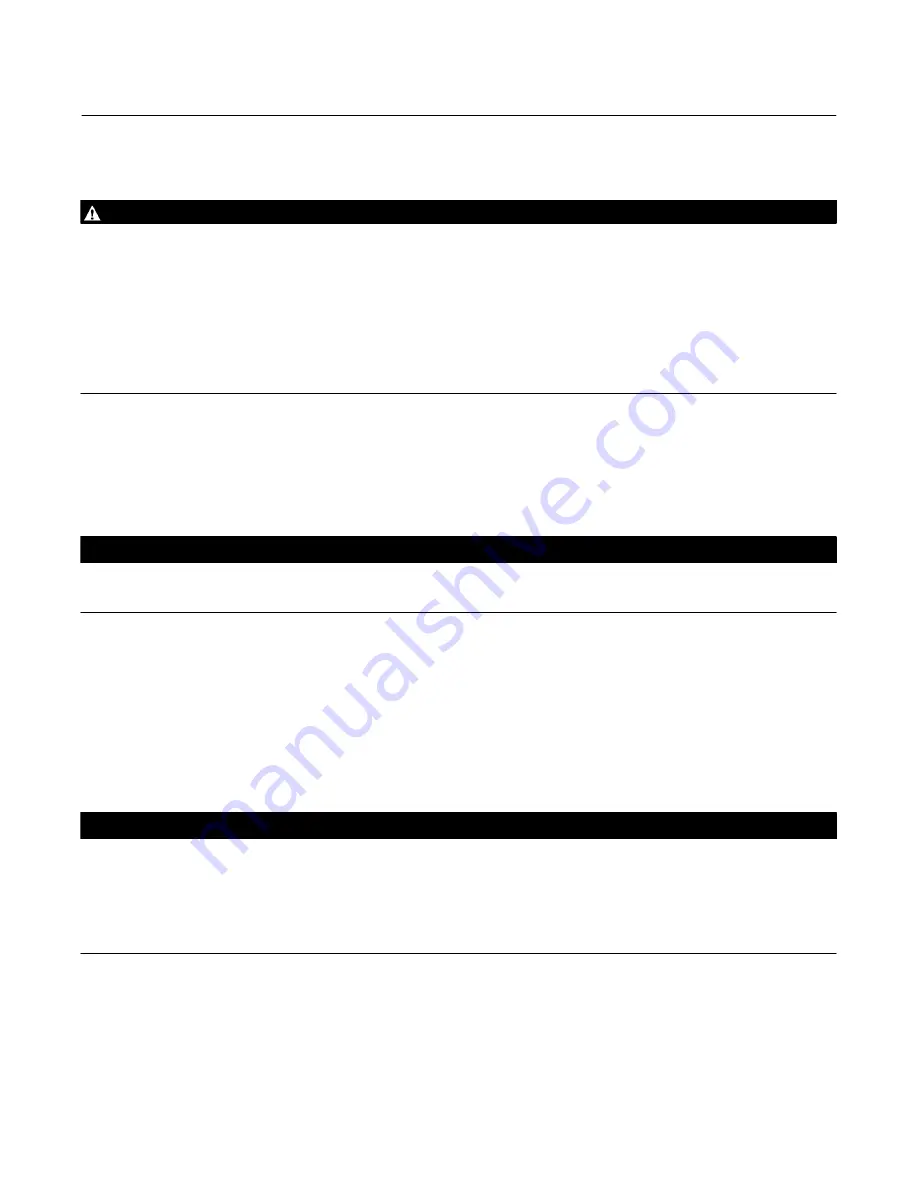
Instruction Manual
D100333X012
1069 Actuator
April 2018
3
the valve body, or if it is necessary to change actuator mounting positions, perform the actuator mounting
procedures.
WARNING
To avoid personal injury or property damage caused by bursting of pressure‐retaining parts, be certain the cylinder
pressure does not exceed the cylinder pressure limits listed in table 1. Use pressure‐limiting or pressure‐relieving devices to
prevent the cylinder pressure from exceeding these limits.
Always wear protective gloves, clothing, and eyewear when performing any installation operations to avoid personal
injury.
Check with your process or safety engineer for any additional measures that must be taken to protect against process
media.
If installing into an existing application, also refer to the WARNING at the beginning of the Maintenance section in this
instruction manual.
Actuator Mounting
Use the following steps to connect a valve body and actuator that have been ordered separately. This procedure can
also be performed to change actuator mounting positions. Key numbers used in this procedure are shown in figure 4.
CAUTION
To avoid possible damage to the travel stop screws (key 35 and, if used, key 9), make sure the travel stop screws are turned
all the way into the housing (key 15) before setting the housing on its support legs.
1. Remove the cap screws and washers (keys 25 and 38) and then remove the cover (key 24). If a manual operator is
used, it is removed with the cover.
2. Remove the cap screws and anti‐rotator assemblies (keys 8 and 42).
3. If the lever (key 19) is attached to the valve shaft, loosen the cap screws (key 20) and rotate the set screw (key 41)
clockwise slightly to spread the split portion of the lever. Then, remove the lever through the openings in the
housing (key 15). For an 8510 valve body, the disk must be open approximately 20 degrees to allow enough
clearance for lever removal. For a V250 valve body, the ball must be open approximately 70 degrees to allow
enough clearance for lever removal. Consult the valve body instruction manual for assistance during this step.
CAUTION
Do not use a hammer or similar tool to drive the lever (key 19) off the valve shaft. Driving the lever could damage internal
valve parts. On some valve bodies, driving the lever could move the valve disk and bearings away from the centered
position, causing subsequent damage to valve parts as the valve is operated.
If necessary, use a wheel puller to remove the lever. It is okay to tap the wheel puller screw lightly to loosen the lever, but
hitting the screw with excessive force could also damage valve parts or disrupt the centered position of the valve disk and
bearings.
4. If the housing was removed from the mounting yoke (key 17), secure it to the mounting yoke with the cap screws
(key 18).
in a horizontal pipeline. If changing actuator mounting positions, unscrew the cap screws (key 18) and rotate the
housing (key 15) to the desired position.