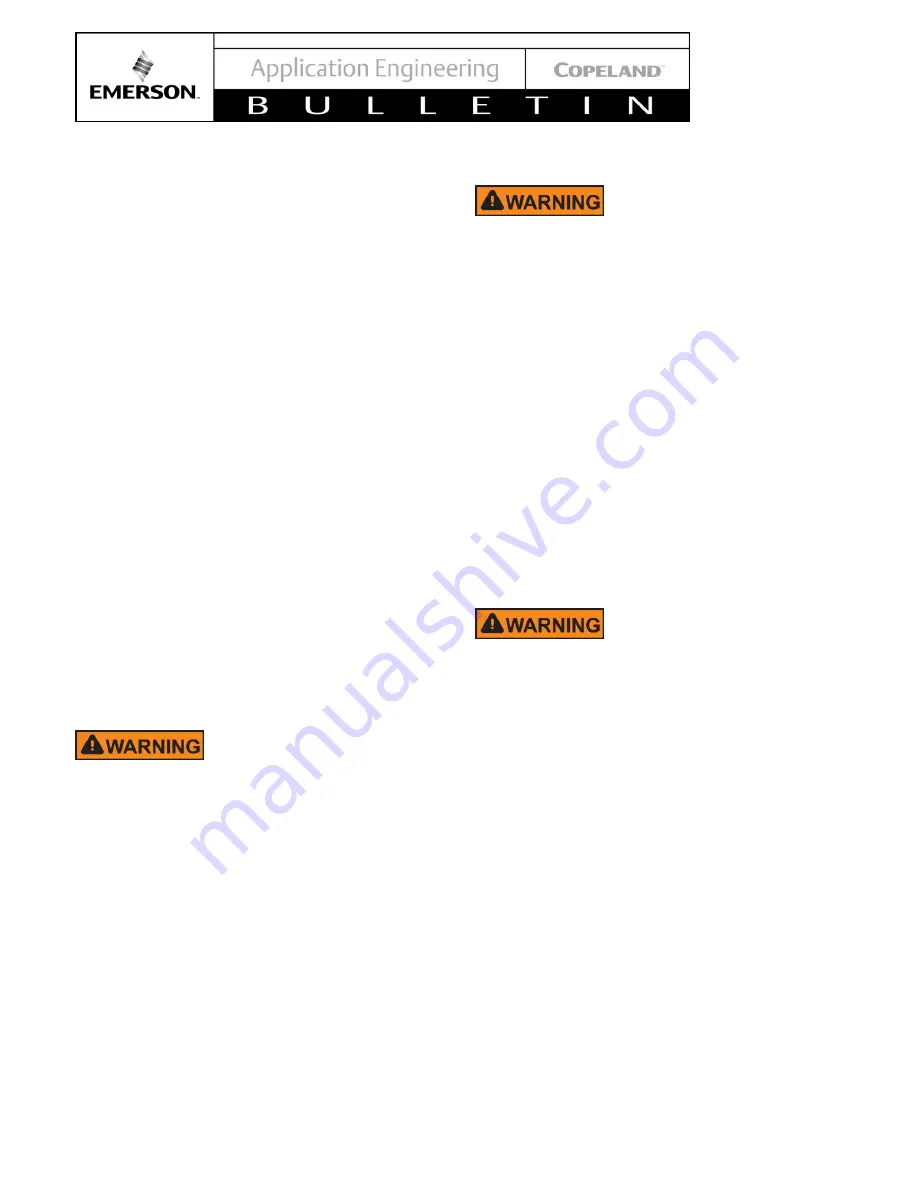
© 2017 Emerson Climate Technologies, Inc.
11
AE4-1414
APPLICATION TESTS
New system designs should be evaluated throughout
the entire expected operating range of the unit to
ensure the system will perform reliably throughout the
life of the product. Test data, taken throughout the
operating range of the unit, should be closely
scrutinized to help identify gross errors in system
design that may produce conditions that could lead to
compressor failure.
General Application Tests
In addition to the tests outlined above, off-cycle
migration tests are recommended if the system
charge amount exceeds 11 pounds (7 kg) and less
than 100 watts of the stator heat option is selected.
The purpose of the off-cycle migration test is to
ensure that stator heat is great enough to minimize
off-cycle migration after long compressor 'off' periods.
System faults, such as low or loss of indoor air-flow,
loss
of
outdoor
air-flow,
and
low/overcharge
conditions should all be evaluated to ensure the
compressor and service technician are protected
against any adverse condition.
NOTICE The tests outlined above are for common
applications of compressors in this family. Please
consult
with
Application
Engineering
on
applications outside of those outlined above for
the appropriate application tests.
ASSEMBLY LINE PROCEDURES
Installing the Compressor
Use care and the appropriate material handling
equipment when lifting and moving compressors.
Personal safety equipment must be used.
Copeland Scroll compressors leave the factory
dehydrated, with a dry air holding charge. If
compressors are stored in a cold ambient (i.e. outside
during the winter), the suction and discharge plugs
should not be removed until the compressor has had
sufficient time to warm up to the plant ambient
temperature. The suggested warm up time is one
hour per 4°F (2°C) difference between outdoor and
indoor temperature. It is suggested that the larger
suction plug be removed first to relieve the internal
pressure. Removing the smaller discharge plug could
result in a spray of oil out of this fitting since some oil
accumulates in the head of the compressor after
Emerson’s run test. The inside of both fittings should
be wiped with a lint free cloth to remove residual oil
prior to brazing. A compressor containing POE oil
should never be left open longer than 20 minutes.
Assembly Line Brazing Procedure
Personal safety equipment must be used during
brazing operation. Heat shields should be used to
prevent overheating or burning nearby
temperature sensitive parts. Fire extinguishing
equipment should be accessible in the event of a
fire.
Figure 4
discusses the proper procedures for brazing
the suction and discharge lines to a scroll
compressor.
NOTICE It is important to flow nitrogen through
the system while brazing all joints during the
system assembly process.
Nitrogen displaces the
air and prevents the formation of copper oxides in the
system. If allowed to form, the copper oxide flakes
can later be swept through the system and block
screens such as those protecting capillary tubes,
expansion valves, and accumulator oil return holes.
Any blockage of oil or refrigerant may damage the
compressor resulting in failure.
Pressure Testing
Never pressurize the compressor to more than 475
psig (33 bar) for leak checking purposes. Never
pressurize the compressor from a nitrogen
cylinder or other pressure source without an
appropriately sized pressure regulating and relief
valve.
The pressure used on the line to meet the U.L. burst
pressure requirement must not be higher than 475 psig
(33 bar). Higher pressure may result in permanent
deformation of the compressor shell and possible
misalignment or bottom cover distortion.
Assembly Line System Charging Procedure
Systems should be charged with liquid on the high side
to the extent possible. The majority of the charge
should be pumped in the high side of the system to
prevent low voltage starting difficulties, hipot failures,
and bearing washout during the first-time start on the
assembly line. If additional charge is needed, it should
be added as
liquid
to the low side of the system with
the compressor operating. Pre-charging on the high
side and adding liquid on the low side of the system
are both meant to protect the compressor from
operating with abnormally low suction pressures during
charging.
NOTICE:
Do not operate the compressor
without enough system charge to maintain at least
55 psig (3.8 bar) suction pressure. Do not operate
Summary of Contents for Copeland Scroll ZPV066
Page 14: ... 2017 Emerson Climate Technologies Inc 14 AE4 1414 ...
Page 15: ... 2017 Emerson Climate Technologies Inc 15 AE4 1414 ...
Page 17: ... 2017 Emerson Climate Technologies Inc 17 AE4 1414 ...
Page 18: ... 2017 Emerson Climate Technologies Inc 18 AE4 1414 ...
Page 19: ... 2017 Emerson Climate Technologies Inc 19 AE4 1414 ...