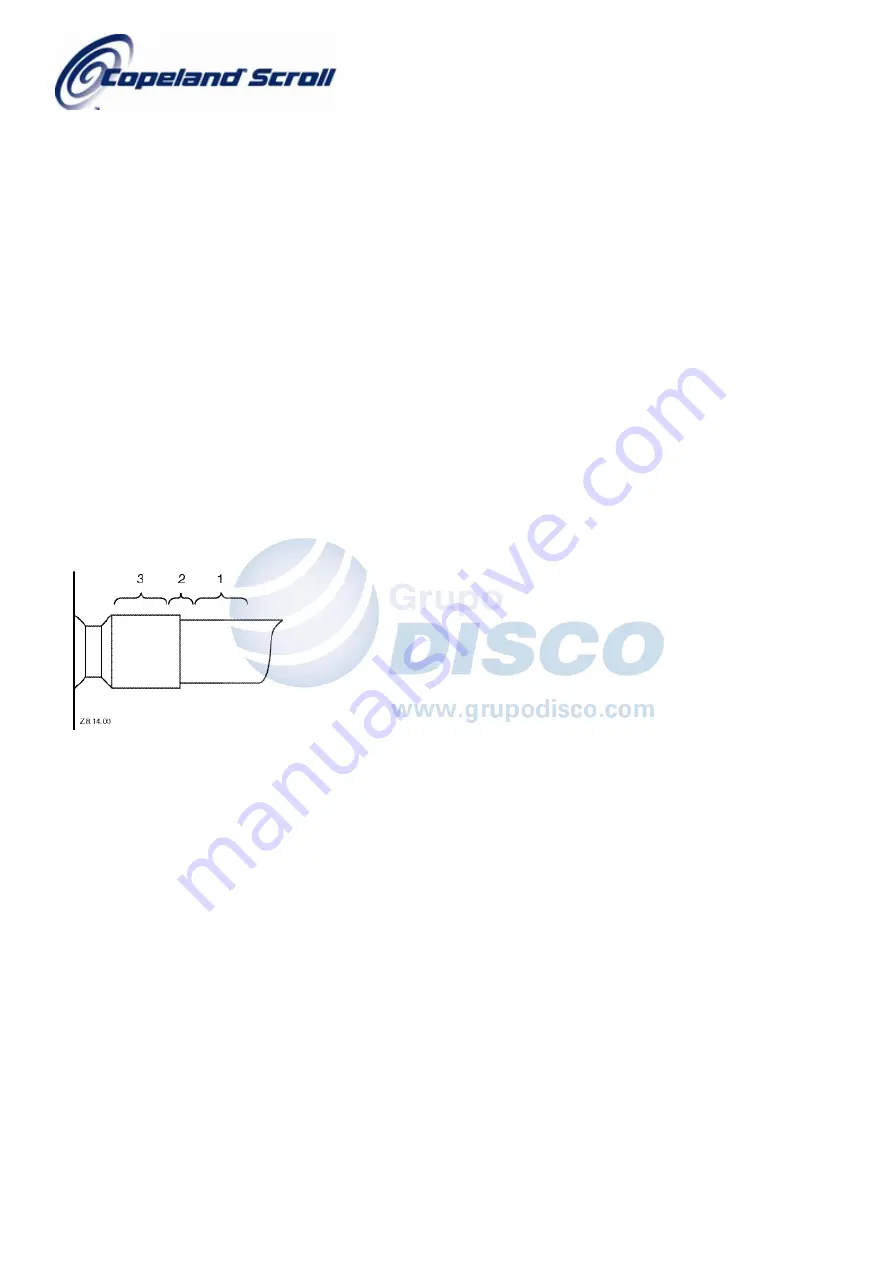
22 Service
Copeland Scroll compressors have copper plated steel suction and discharge tubes. These tubes are far more robust
and less prone to leaks than copper tubes used on other compressors. Due to the different thermal properties of steel
and copper, brazing procedures may have to be changed from those commonly used. For brazing of the tubes see
Figure 11 and the following procedures. Since the discharge stub contains a check valve, care must be taken not to
overheat it as well as to prevent brazing material from flowing into it.
23 New
Installations
The copper-coated steel tubes on scroll compressors can be brazed in approximately the same manner as
any copper tube. Recommended brazing materials: Any silfos material is recommended, preferably with a
minimum of 5% silver. However, 0% silver is acceptable.
Be sure tube fitting inner diameter and tube outer diameter are clean prior to assembly.
Using a double-tipped torch apply heat in area
As the tube approaches brazing temperature, move the torch flame to area 2.
Heat area 2 until braze temperature is attained, moving the torch up and down and rotating around the tube
as necessary to heat the tube evenly. Add braze material to the joint while moving the torch around the joint
to flow braze material around the circumference.
After the braze-material flows around the joint, move the torch to heat area 3. This will draw the braze-
material down into the joint. The time spent heating area 3 should be minimal.
As with any brazed joint, overheating may be detrimental to the final result.
Figure 11: Suction tube brazing
24 Field
Service
To disconnect:
Heat joint areas 2 and 3 slowly and uniformly until the braze material softens and the tube can be pulled out
of the fitting.
To reconnect:
Recommended brazing-materials: Silfos with minimum 5% silver or silver braze used on other compressors.
Due to the different thermal properties of steel and copper, brazing procedures may have to be changed from
those commonly used. For brazing of the tubes see Figure 11 and the following procedures.
Since the discharge stub contains a check valve, care must be taken not to overheat it as well as to prevent
brazing material to flow into it.
C6.2.9/0203-1004/E 10