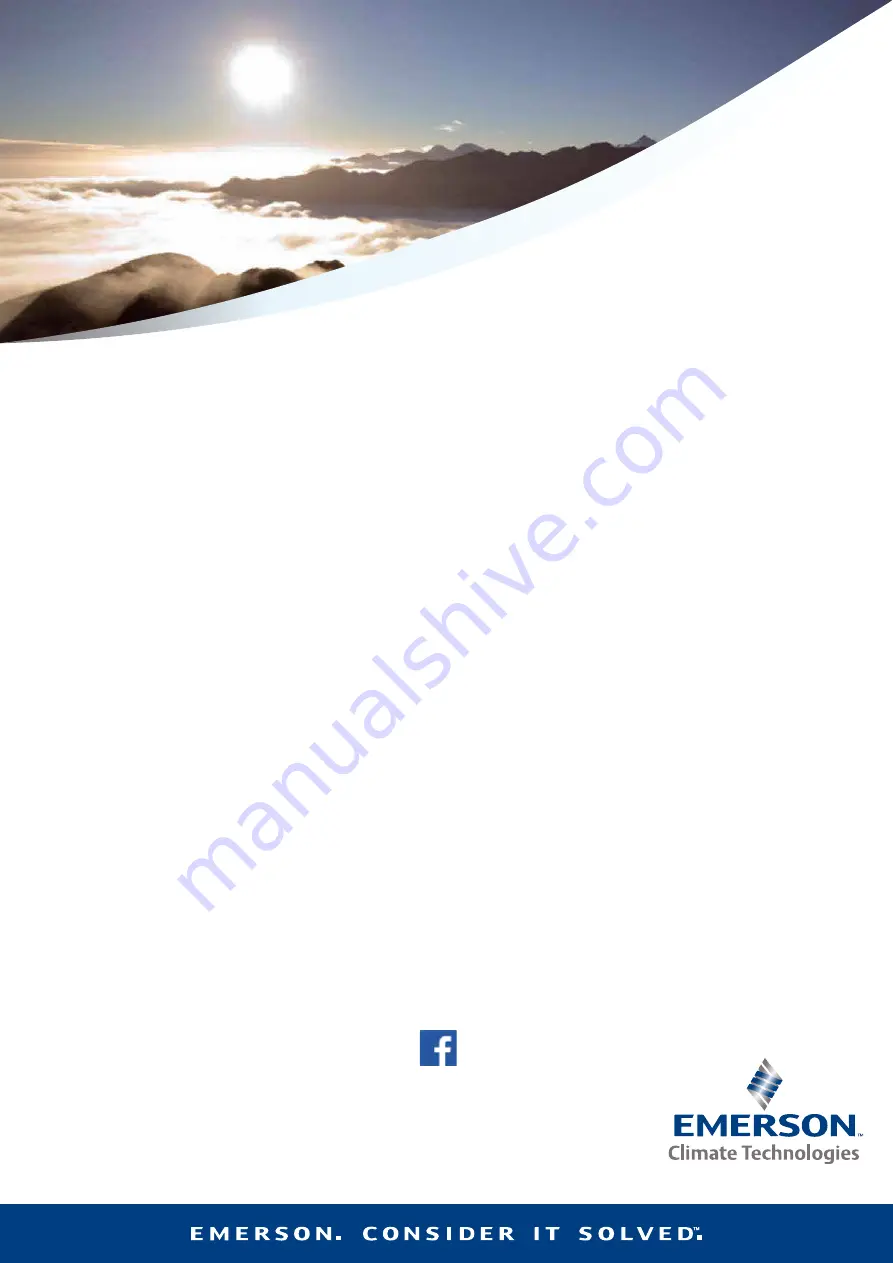
D6.3.4/0715-0716/E
BENELUX
Josephinastraat 19
NL-6462 EL Kerkrade
Tel.
+31 77 324 02 34
Fax
+31 77 324 02 35
UK & IRELAND
Unit 17, Theale Lakes Business Park
Reading, Berkshire RG7 4GB
Tel:
+44 1189 83 80 00
Fax:
+44 1189 83 80 01
BALKAN
Selska cesta 93
HR-10 000 Zagreb
Tel.
+385 1 560 38 75
Fax
+385 1 560 38 79
GERMANY, AUSTRIA & SWITZERLAND
Senefelder Str. 3
DE-63477 Maintal
Tel.
+49 6109 605 90
Fax
+49 6109 60 59 40
SWEDEN, DENMARK, NORWAY & FINLAND
Norra Koxåsvägen 7
SW-443 38 Lerum
Tel.
+46 725 386486
FRANCE, GREECE & MAGHREB
8, Allée du Moulin Berger
FR-69134 Ecully Cédex
Tel.
+33 4 78 66 85 70
Fax
+33 4 78 66 85 71
EASTERN EUROPE & TURKEY
Pascalstr. 65
DE-52076 Aachen
Tel.
+49 2408 929 0
Fax
+49 2408 929 525
T
Tel.
Fax
+852 2866 3108
+852 2520 6227
ITALY
Via Ramazzotti, 26
IT-21047 Saronno (VA)
Tel.
+39 02 96 17 81
Fax
+39 02 96 17 88 88
POLAND
Szturmowa 2
PL-02678 Warsaw
Tel.
+48 22 458 92 05
Fax
+48 22 458 92 55
MIDDLE EAST & AFRICA
PO Box 26382
Jebel Ali Free Zone - South, Dubai - UAE
Tel.
+971 4 811 81 00
Fax
+971 4 886 54 65
ASIA PACIFIC
Suite 2503-8, 25/F, Exchange Tower
33 Wang Chiu Road, Kowloon Bay
Kowloon, Hong Kong
SPAIN & PORTUGAL
C/ Pujades, 51-55 Box 53
ES-08005 Barcelona
Tel.
+34 93 412 37 52
Fax
+34 93 412 42 15
RUSSIA & CIS
Emerson LLC
Dubininskaya str. 53, build. 5, 4th floor
115054 Moscow, Russia
Phone: +7 (495) 995 95 59
Fax:
+7 (495) 424 88 50
ROMANIA
el.
+40 374 13 23 50
Fax
+40 374 13 28 11
Emerson Climate Technologies - European Headquarters
- Pascalstrasse 65 - 52076 Aachen, Germany
Tel. +49 (0) 2408 929 0 - Fax: +49 (0) 2408 929 570 - Internet: www.emersonclimate.eu
The Emerson Climate Technologies logo is a trademark and service mark of Emerson Electric Co. Emerson Climate Technologies Inc. is a subsidiary of Emerson Electric Co.
Copeland is a registered trademark and Copeland Scroll is a trademark of Emerson Climate Technologies Inc.. All other trademarks are property of their respective owners.
Emerson Climate Technologies GmbH shall not be liable for errors in the stated capacities, dimensions, etc., as well as typographic errors. Products, specifications, designs
and technical data contained in this document are subject to modification by us without prior notice. Illustrations are not binding.
© 2015 Emerson Climate Technologies, Inc.
For more details, see www.emersonclimate.eu
Connect with us: facebook.com/EmersonClimateEurope