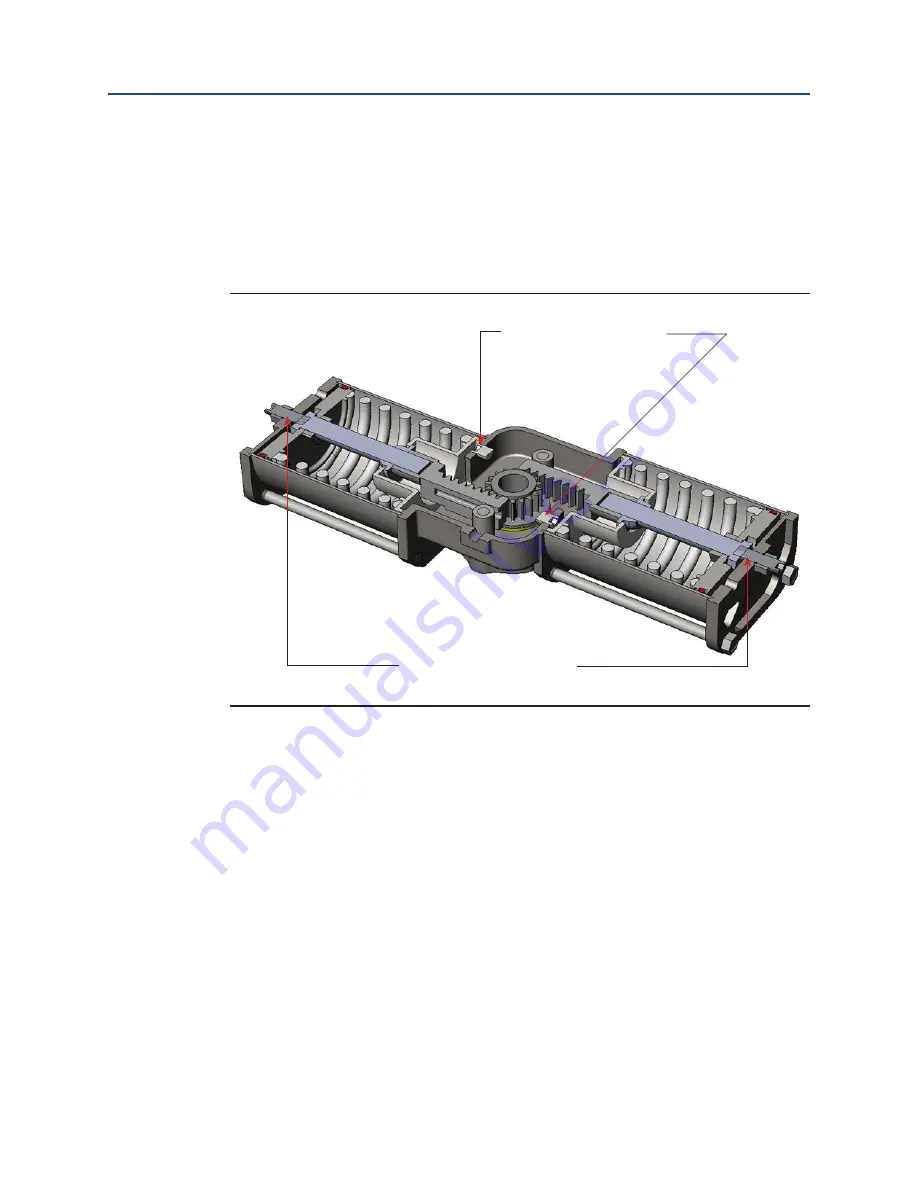
Installation, Operation and Maintenance Manual
RGS011110-1 Rev. 0
September 2015
8
Section 4: Travel Adjustment
Travel Adjustment
4�4
Inward Travel Adjustment
•
Removal of both cylinders is required and multiple adjustments may be required
- for this reason we recommend against attempting to adjust inward motion,
preferring to achieve adjustment via bracket motion, followed by resetting the
end cap travel screws.
Figure 13
Outward and Inward Travel Adjustment Screws
Inward Travel Adjustment Screws
- One For Each Cylinder
Outward Travel Adjustment Screws
- One For Each Cylinder