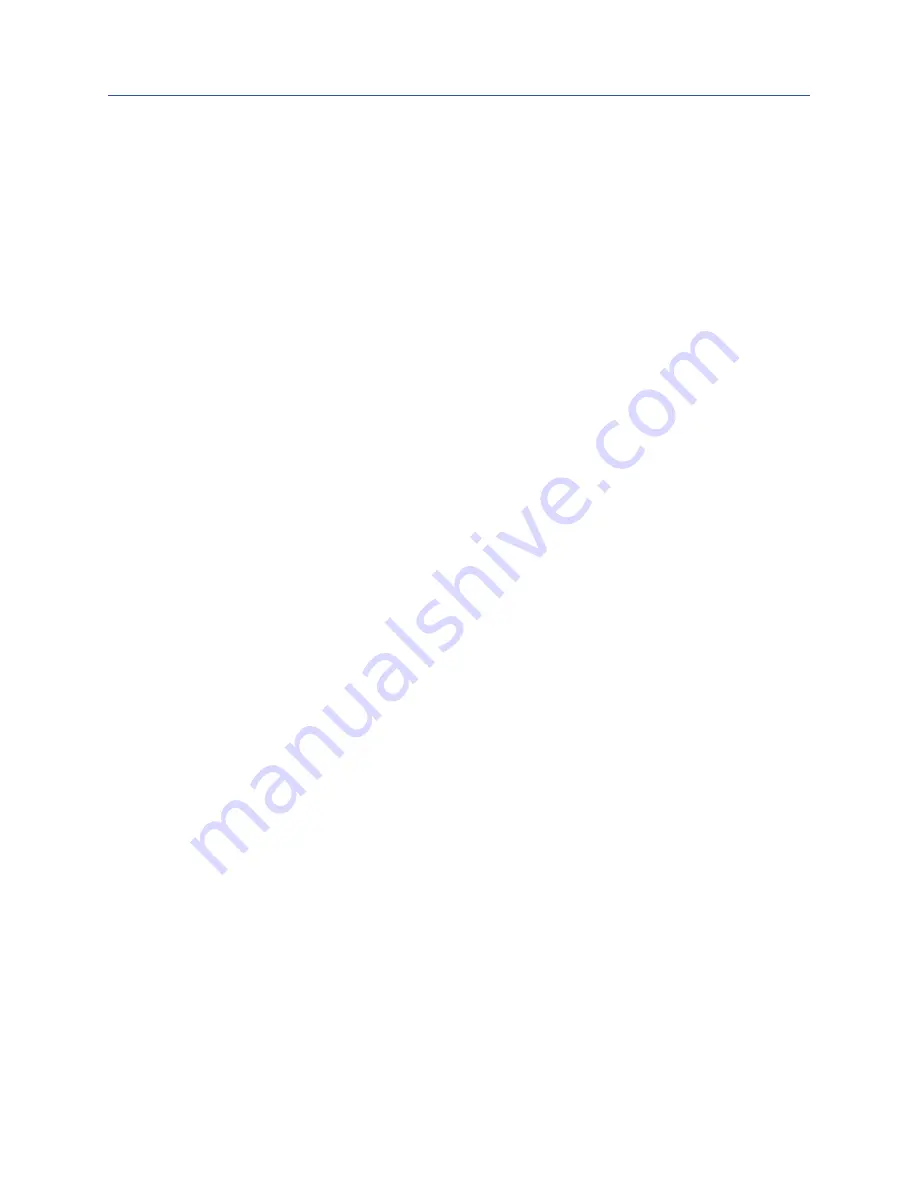
Installation, Operation and Maintenance Manual
MAN-02-10-92-0705-EN Rev. 0
March 2019
4
Section 3: Disassembly Instructions
Disassembly Instructions
Section 4: Disassembly Instructions
4.1
Instructions - WO & WB AWWA Gears
Refer to Figure 1.
1. Remove hex head cap screws (12) and seal washers (15).
2. Remove jam screws (13).
3. Remove stop screws (14) from main housing.
4. Rotate handwheel shaft clockwise until pointer cap (16) stops rotating or until
handwheel shaft can no longer be turned.
5. Remove dial indicator (16) and housing cover (3). Note: WB units have no dial
indicator (16).
6. Remove closed cap (1) and open cap (24).
7. Remove thrust bearing cups (2) from main housing. By rotating worm shaft (18)
in both directions.
8. Pull worm shaft (18) from main housing (4). Caution: Note the assembly
position of the worm shaft for accurate reassembly. Do not remove bearings
from the worm shaft.
9. Once the worm is clear, remove the two thrust bearing cones (5).
10. Remove drive sleeve (19) lifting upward from main housing. Caution: Note
position of drive sleeve in main housing to ensure accurate reassembly. Remesh
gearing during reassembly.
11. Check the condition of all gaskets and o-rings. If torn or damaged, replace.
12. Reassemble the actuator by reverse order of the steps listed above. The end cap
gasket thickness is generally 1 /32" to 1 /64 ° . This is determined by the amount
of axial float in the worm shaft once the bolts on both the end caps (1 & 24)
have been tightened. When properly adjusted, axial float should be almost
eliminated, while still allowing the worm shaft to be easily rotated by hand (larger
WO/WB units require a handwheel or T-bar to rotate input shaft even under no
load conditions).
13. Preset mechanical stops for 90° of rotation by moving the drive sleeve (worm gear)
to its approximate center point (mid travel). From this midpoint, estimate 45 ° travel
in the open direction. Insert stop screw (14) and adjust accordingly. Repeat this step
for the closed direction (90° from open or 45° from center). Before reinstallation of
the housing cover (3), fill the housing with recommended lubrication (Texaco EP-0 or
equal) to approximately 3/4 full (check that worm shaft and bearings are covered).
Refer to lubrication instructions for additional details.
Once the actuator is installed on the valve, it will be necessary to final adjust the stop
screws to suit the actual valve movement required. (Refer to installation procedure,
stop setting).