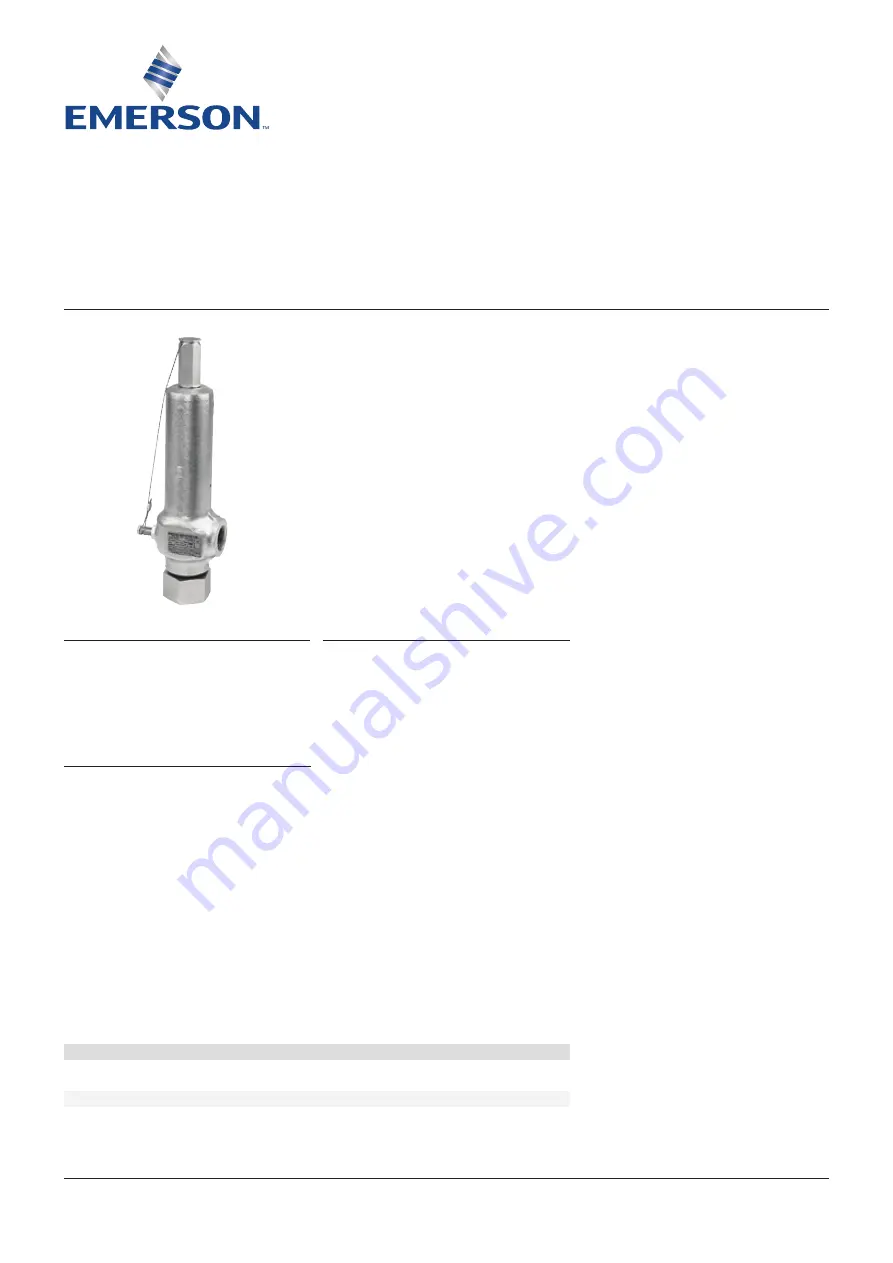
ANDERSON GREENWOOD
TYPE 81P DSO PRESSURE RELIEF VALVES
MAINTENANCE INSTRUCTIONS
1 GENERAL
The Anderson Greenwood Type 81P Direct
Spring Operated (DSO) Relief Valve is a direct
acting spring loaded valve for liquid service and
uses a plastic seat and O-ring seals.
The intent of these instructions is to acquaint
the user with the maintenance of this product.
Please read these instructions carefully. This
product should only be used in accordance
with the applicable operating instructions and
within the application specifications of the
original purchase order. The installation and
Operational Safety Instructions (available at
www.valves.emerson.com) should be fully read
and understood before returning this product to
service after maintenance.
2 VALVE REPAIR (-4, -8 ORIFICE)
Refer to Figure 1
2.1 Disassembly
2.1.1 Relieve spring tension by turning the
pressure adjusting screw counter-
clockwise.
2.1.2 Remove inlet bushing, bushing seal and
valve internals.
2.1.3 Separate nozzle from guide by hitting
top of spindle on soft surface. Remove
spindle seals.
2.2 Repair
2.2.1 Hold spindle by skirt O.D. in soft jaw vise
and replace seat.
2.2.2 Examine nozzle and polish out any
scratches or nicks. Replace if necessary.
2.2.3 To obtain better seat seal with PTFE at
low set pressures, burnish seat against
nozzle by chucking spindle in lathe and
holding nozzle against spindle. Burnish
with small force and for short time as
PTFE deforms easily.
LUBRICANTS
Part
Set pressure
Lubricant
Spindle seals
50-1000 psig (3.4 - 69.0 barg)
Dow Corning FS3451
Above 1000 psig (69.0 barg)
Desco 600
Thread and adjusting bolt tip
All
Dow Corning 33
Engineering Doc. #05.9040.072 Rev. K
Before installation these instructions must be fully read and understood
WARNING
An attempt to repair this product by unauthorized
or unqualified persons voids the product warranty
and may cause damage to equipment and serious
injury or death to persons.
The product is a safety related component
intended for use in critical applications.
The improper application, installation or
maintenance of the product or the use of parts
or components not manufactured by Anderson
Greenwood may result in a failure of the product.
Any installation, maintenance, adjustment, test,
etc. performed on the product must be done
in accordance with the requirements of all
applicable Anderson Greenwood procedures and
instructions as well as applicable National and
International codes and standards.
VCIOM-01056-EN 16/12
TABLE OF CONTENTS
1. General ........................................................... 1
2. Valve repair (-4, -8 orifice) ............................ 1
3. Valve repair (G, J orifice) ............................... 3
4. Valve adjustment ........................................... 4
5. Seat leakage .................................................. 5
2.3 Assembly
Assemble in reverse order of
disassembly. Lubricate the parts listed
below with the specified lubricant. Make
sure the nozzle is fully and squarely
seated in guide.
Emerson.com/FinalControl
© 2017 Emerson. All rights reserved.