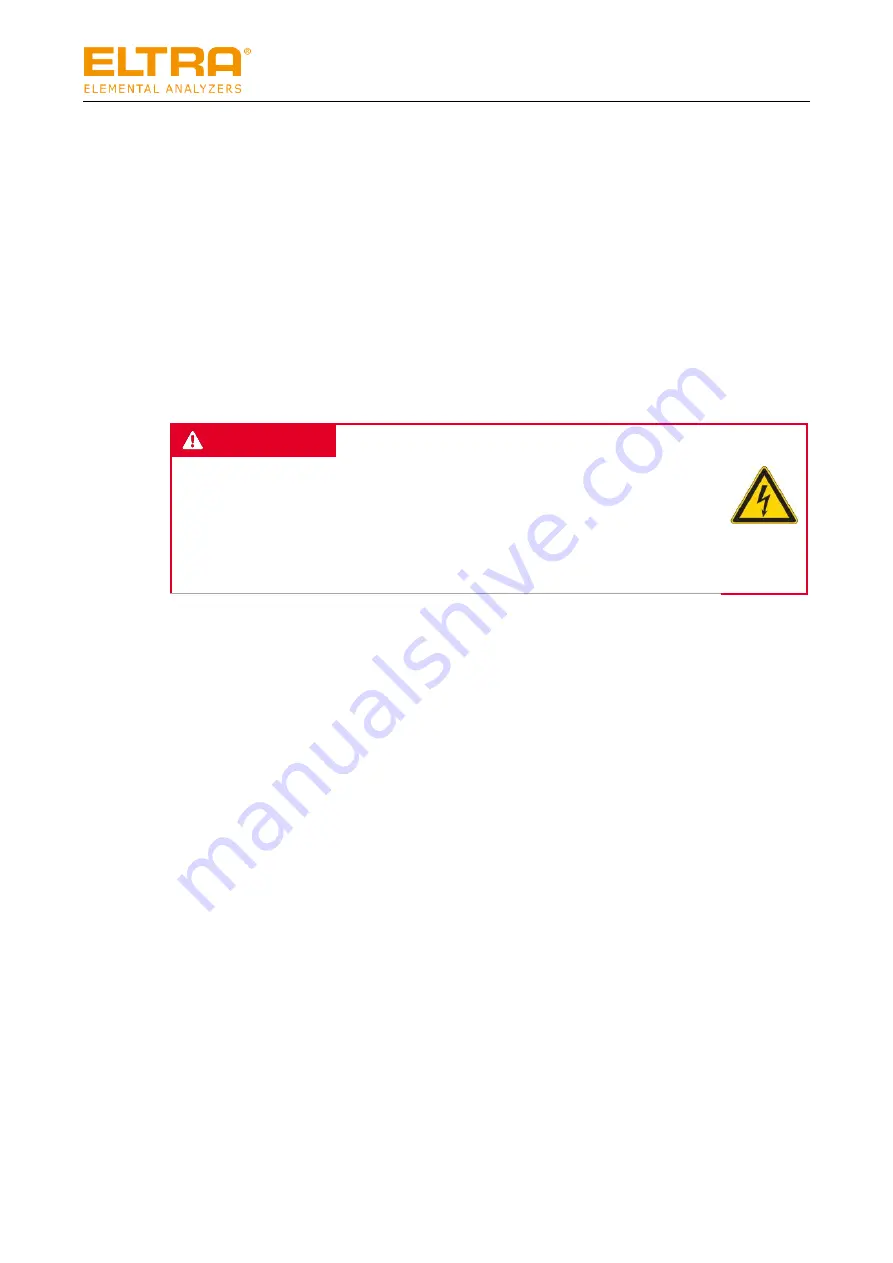
Spare parts
104
Attention!
Important information!
The information in the following section is purely informative and is not a call to action.
All work on the components described must be performed by appropriately qualified service
personnel. The voltage range is 10 kV.
A special tool (Part No.: 1101-2005) is required to discharge the oscillating circuit.
ELTRA Service must be contacted before opening the right-hand side of the machine to work
on this side.
DANGER
D7.0005
Risk to life caused by an electric shock
Exposed power contacts
– high voltage
•
An electric shock can cause serious injuries in the form of burns, cardiac
arrhythmia, respiratory failure or cardiac arrest.
•
Set the mains switch on the analyzer to position 0 and unplug the
mains plug from the socket.