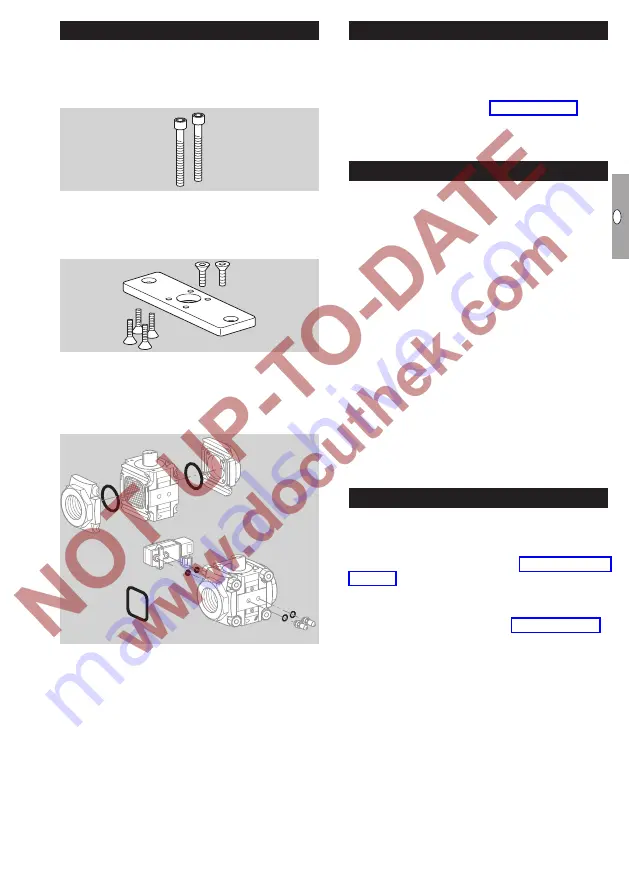
GB-5
D
GB
F
NL
I
E
Accessories
Fastening set IC-BVG../VFC
For the assembly of VFC and IC 20 or IC 40. The
fastening set is fitted at the factory or delivered en-
closed as an additional item.
Order No.: 74921082
Adapter set IC 0/VFC
For the assembly of VFC and IC 30. The adapter set
is delivered enclosed as an additional item.
Order No.: 74340194
Seal set for sizes and
▷
When retrofitting accessories or a second
valVario control or when servicing, we recom-
mend replacing the seals.
A
C
B
A
D
▷
Order No. for
size 1: 74921988,
size 3: 74921990.
▷
Scope of delivery:
A
2 x O-rings (flange),
B
2 x O-rings (pressure switch),
for test point/screw plug:
C
2 x sealing rings (flat sealing), 2 x profiled seal-
ing rings,
D
1 x double block seal; this is not required for
VFC.
Maintenance
In order to ensure smooth operation, check the tight-
ness and function of the VFC every year, or every six
months if operated with biogas.
▷
After carrying out the maintenance work, check
for tightness, see page 4 (Tightness test).
▷
The VFC suffers little wear and requires little
servicing.
Technical data
Gas type: natural gas, LPG (gaseous), biogas
(max. 0.1 %-by-vol. H
2
S) or clean air; other types
of gas on request. The gas must be dry in all
temperature conditions and must not contain
condensate.
Control ratio: 25:1.
Leakage rate: < 2% of k
VS
value.
Max. inlet pressure p
u
max.
: 500 mbar (7.25 psi).
Running times:
IC 20: 7.5 s, 15 s, 30 s, 60 s
IC 30: 30 s, 60 s
IC 40: 4.5 s – 76.5 s.
Connection flanges: Rp internal thread pursuant
to ISO 7-1.
Housing material: aluminium,
control cylinder: aluminium,
flow restricting cylinder: POM/aluminium,
seal: HNBR/NBR.
Ambient temperature: -20 to +60°C (-4 to +140°F).
Storage temperature: -20 to +40°C (-4 to +104°F).
Logistics
Transport
Protect the unit from external forces (blows, shocks,
vibration). On receipt of the product, check that the
delivery is complete, see page 2 (VFC part des-
ignations). Report any transport damage immediately.
Storage
Store the product in a dry and clean place.
Storage temperature: see page 5 (Technical data).
Storage time: 6 months in the original packaging
before using for the first time. If stored for longer
than this, the overall service life will be reduced by
the corresponding amount of extra storage time.
Packaging
The packaging material is to be disposed of in ac-
cordance with local regulations.
Disposal
Components are to be disposed of separately in
accordance with local regulations.