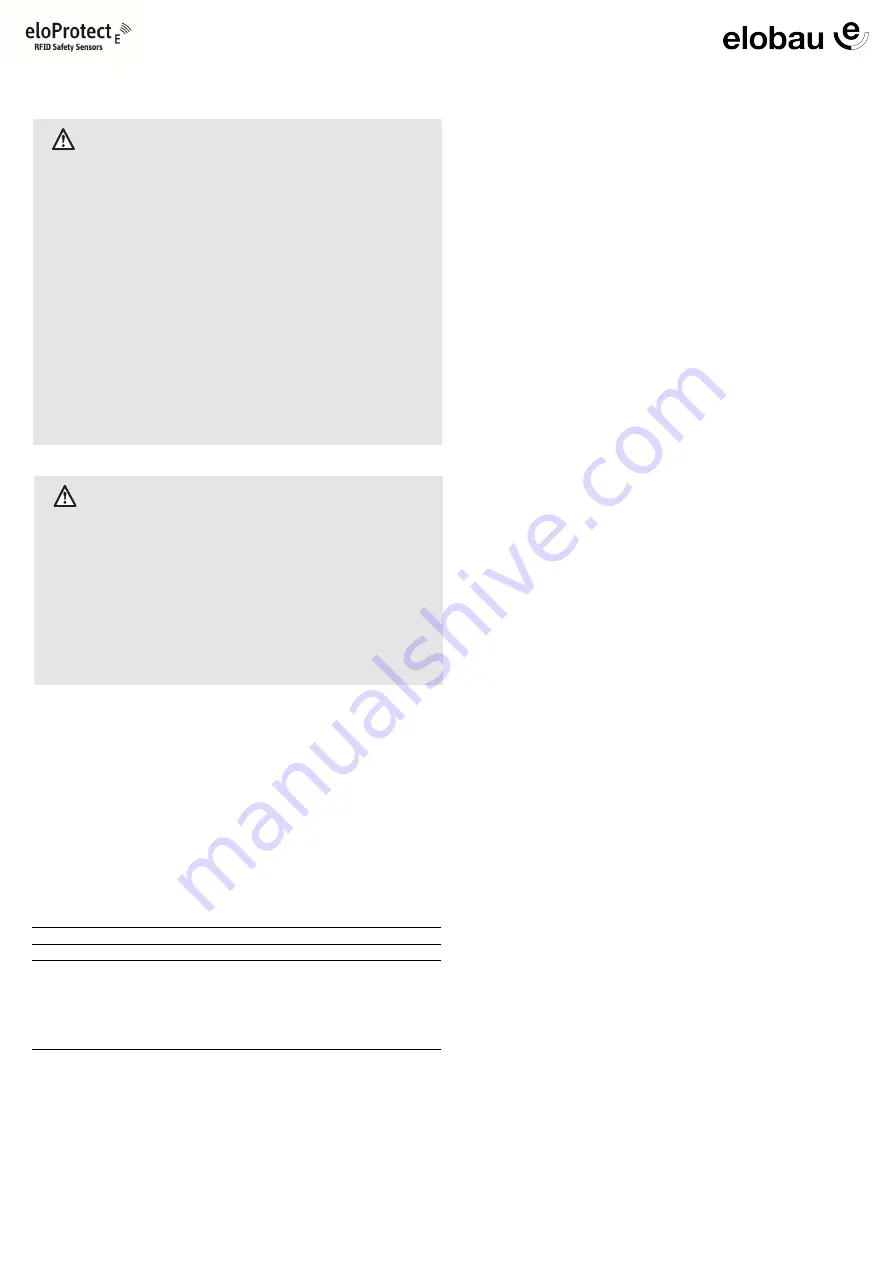
Art.-Nr./Art. No./Réf./N° art/N° art.: 9010017B01M
Ve
rsion
1.0
Date
: 25.05.2016
2/15
165ESK...
5
Warning against misuse
6
Disclaimer
No liability can be accepted for damage or outages resulting from non-compli-
ance with this instruction manual. For damage resulting from the use of spare
parts or accessories unapproved by the manufacturer, any further liability of
the manufacturer is excluded.
Any unauthorized repairs, modifications and additions are not permitted for
safety reasons and the manufacturer is also not liable for any resulting damage.
- Make sure that the safety sensors are mounted only by specially
trained, authorized, qualified personnel and put into service
safely.
- Only install and commission the device if you have read and
understood the operating instructions and are familiar with the
applicable regulations on occupational safety and accident
prevention.
- The safety sensor may only be operated exclusively by the
actuator which is properly mounted on the guard. Actuation
when not mounted on the guard is prohibited.
- Operate the safety sensors only if they are in undamaged
condition.
- Make sure that the safety sensors are used exclusively to
protect against hazards.
- Make sure that all applicable safety requirements for the respec-
tive machine are complied with.
- Make sure that all applicable laws and regulations are complied
with.
- Residual risks are not known when the instructions in this man-
ual are adhered to.
- Inexpert or improper use or tampering in combination with the
use of safety sensors can lead to hazards for personnel or
damage to machine or system parts.
Also observe the relevant notes relating to EN ISO 14119.
- Make sure that no external component causes current or
voltage peaks which are higher than the specified electrical data
of the safety relay. Current or voltage peaks are produced for
example by capacitive or inductive loads.
- Exceeding the electrical data of the safety sensor (e.g. in case
of faulty wiring or shorts) can damage it irreparably.
- Operation of the safety sensor is only allowed with the
appropriate actuator and with the approved control options (see
Technical specifications).
7
Function
Coded, electronic safety sensor, which is operated by a non-contact coded
actuator.
Safety sensors are suitable for the following elobau safety relays:
eloFlex
470EFR...
eloFlex
471EFR...
eloProg
485EPB
485EPE08A02
485EPE08
4854EPE12
485EPE16
7.1
Coding variants
The various versions of the safety sensors arise from the different encodings
designated as type keys under point 1.2. Depending on the variant, a corre-
sponding manipulation protection is achieved.
Coded
The safety sensor accepts any eloProtectE actuator of type 165EBK001.
Type 4; low level coding level according to EN ISO 14119
Individual
The safety sensor accepts one eloProtectE actuator of type 165EBK001. This
actuator is configured individually to the safety sensor. A non-matching actu-
ator in the sensor range will result in an error.
The process for teaching-in a new actuator can be carried out unlimited times
and is descried in detail under "Commissioning" on page
4
.
Type 4; high level coding level according to EN ISO 14119.
Unique
The safety sensor only accepts the eloProtectE actuator supplied. The pair,
consisting of sensor and actuator cannot be separated. If a component should
be lost and is no longer functional, both components must be replaced.
Type 4; high level coding level according to EN ISO 14119.
7.2
Safety outputs
The safety sensor has 2 short-circuit proof PNP safety outputs (OSSD), which
have a max. load of 400 mA per channel.
The safety outputs switch on under the following conditions:
- the correct actuator is detected in the operating range (safety guard closed)
- a high signal is present at both safety inputs
- the EDM input is set correctly
- no error is detected
The safety outputs switch off under the following conditions:
- There is no actuator or the wrong actuator in the detection zone
- Signal is low at one of the two inputs
- An error is detected
The two safety outputs can be connected under the following conditions to the
inputs of a safety controller:
- the input must be appropriate (OSSD signals) for clocked safety signals; the
controller must tolerate test pulses on the inputs (see Technical specifications
on page
7
). Please refer to the instructions of the controller manufacturer.
-
Wiring examples can be found on page
12
.
7.3
Safety inputs
The safety sensor has 2 safety inputs.
- Connect the safety inputs of +24 V DC for single use of the sensor
When using the sensor in a series connection, the safety inputs of the first
sensor can be connected to +24 V DC. The safety inputs of the following
sensors are connected to the safety outputs of the previous sensor. Please
also refer to point 11.1 "Series connection" on page 8.
- Pulses with a duration of max. 900
μ
s are tolerated on the safety inputs.