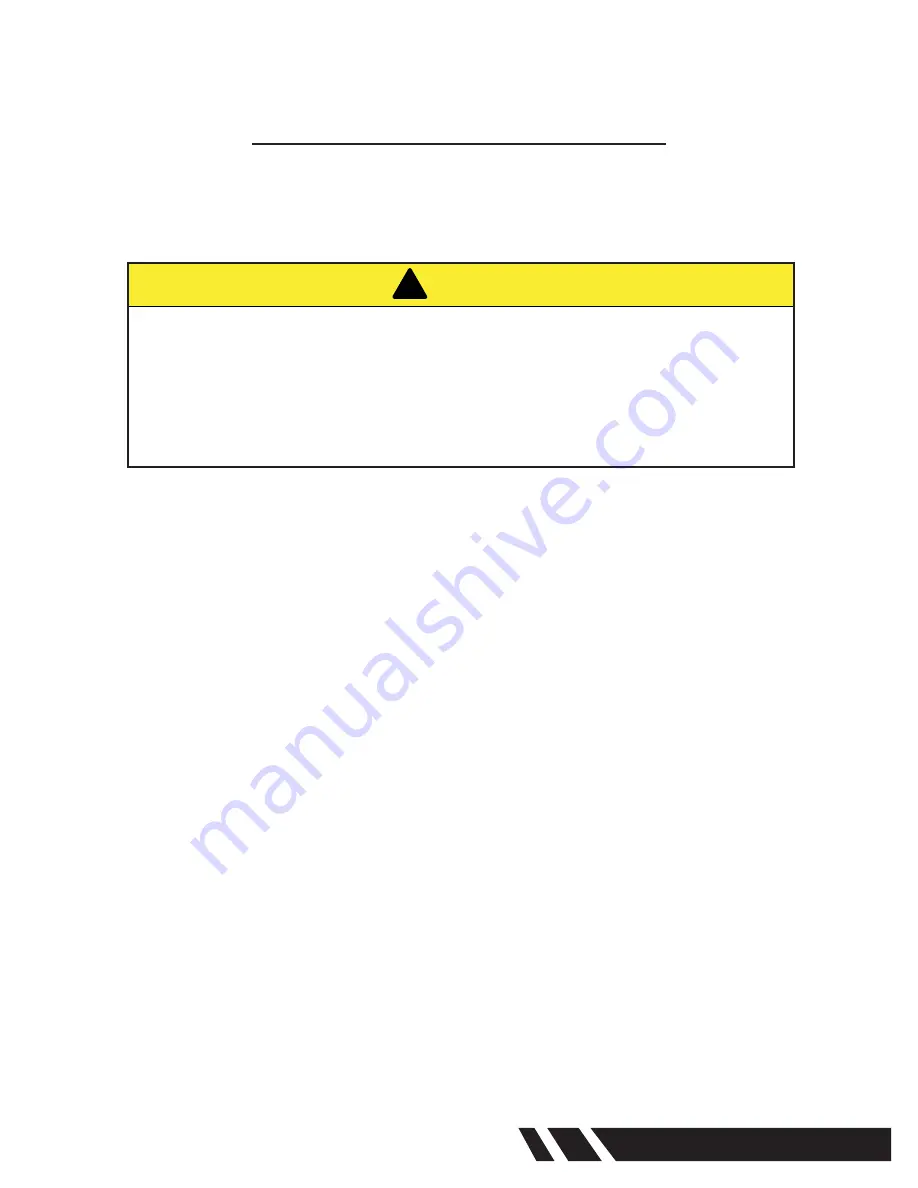
ET850 Pneumatic Rolling Motors
7
OPERATION INSTRUCTIONS
The ET850 is a push-pull type torque controlled rolling motor. It is designed for use with regulated,
filtered and lubricated 90 psig air (measured at the tool inlet). The tool expands to a preset torque, and
then stops. The handle is then pulled away from the tubesheet, operating the motor in reverse and
allowing tool removal from the tubesheet. Any time the operator releases the handle, the motor stops.
Air Supply
The tool is designed to operate on 90-125 psig maximum air pressure. Optimal range is 90-100 psig.
Using 100-125 psig will increase speed but may result in faster wear of expander consumables. The
air pressure should be checked at the tool’s inlet when the tool is running. An automatic in-line filter-
lubricator is required. This will supply tool with clean, lubricated air for optimal performance and tool
life.
The air hose should be cleared of accumulated dirt and moisture. Then pour one half (1/2) teaspoon of
10W machine oil into the tool’s air inlet before connecting the hose to the tool. A new hose should be
similarly lubricated before placing in service. The tool should be cycled several times to disperse the
oil before rolling tubes.
Lubricating The Motor
The in-line lubricator should be regularly checked and kept filled with a good grade of SAE 10W
machine oil. Application of the tool should govern how frequently it is greased.
The gear assembly can be lubricated through an external grease fitting. Using a hand-held grease
gun, apply two shots of NLGI No. 2 Moly grease roughly every four weeks. CAUTION: DO NOT OVER-
LUBRICATE. If too much grease is applied, excess grease will be forced into the motor section and
cause poor operation.
Tube Rolling Procedure
NOTE: Always clean the tube sheet hole before inserting the tubes. Use a proper size expander to
ensure that all tubes are expanded to the same wall reduction.
Set the torque setting ring of the control to the correct torque setting for the type and size of tubes
to be rolled. Insert the expander into the quick change chuck on the motor. The motor is turned on
or off by the means of a quick operating sleeve type valve. The direction of rotation of the spindle
is controlled by the position of the lever handle at the rear of the tool. Pushing forward on the lever
handle causes the spindle to turn in a clockwise direction, and pulling back on the lever handle causes
it to run in reverse. The lever handle also acts as a torque reaction handle to assist in absorbing the
torque of the tool.
CAUTION
!
Caution: If the torque control is adjusted over the maximum power output of the tool,
the torque controlled shut off will not function and the tool will operate like a stall
type tool. Also, if the tool is being operated at its upper torque limits, a drop in air
pressure could cause the torque controlled shut off not to function due to a loss of
motor power and the tool will function like a stall type tool. Operational Check: Grip
tool securely and be prepared to counteract stall torque in case the torque control is
improperly adjusted.
Summary of Contents for ET850 Series
Page 2: ......
Page 20: ...This page intentionally left blank...