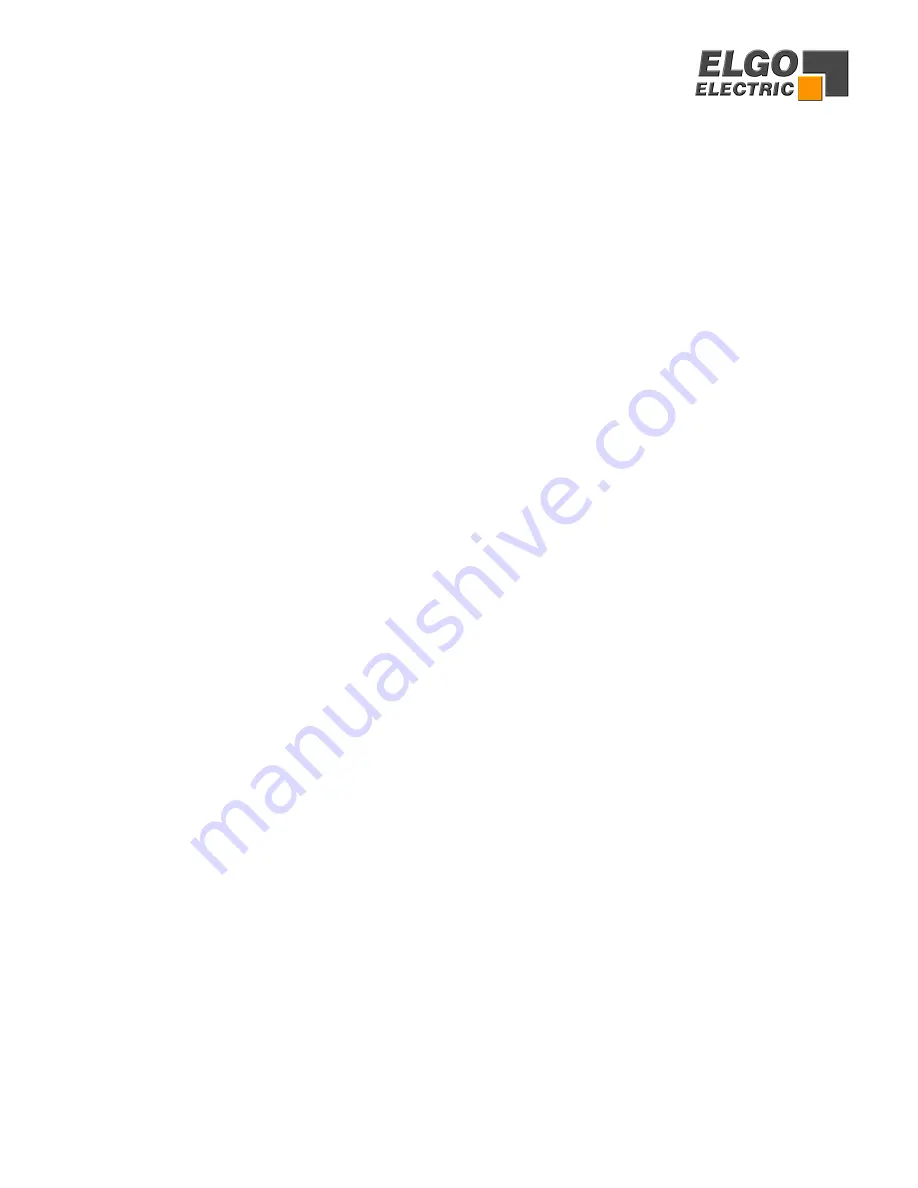
3
1. Short Description
Whilst the P8511-000-P with option Analogue-output is specifically designed to provide closed
loop (Proportional, Integral, Differential) analogue control of 4 quadrant drives, it also serves
the purpose of operating as a 2 or 3 speed controller, as the P8511-000-R.
When used as a closed loop controller, it is essential that: -
1. A 4 quadrant drive – usually a high dynamic servo drive, is used.
2. The drive is capable of accepting a +/- reference signal for direction, without a dead-
band.
3. The Encoder is torsional rigidly coupled to motor.
4. The mechanics of the machine are backlash-free.
Whilst it is possible to use lower specification drives and mechanics, it may then not always
be possible to achieve the performance and accuracy which is commonly expected of a
closed loop system. When using a simple Inverter driven AC motor, it is essential to use the
drive in F/V or FCC mode, rather than the full Flux Vector (which tends to fight the position
controller at low speeds).
•
2 or 3 speed positioning
•
Absolute and incremental positioning modes
•
Operation in Single positioning mode
•
Operation in manual, slow and fast mode
•
Quantity counting with completed output
•
Flexible multiplier for Display calibration
•
Datum setting routines
•
Tool offset compensation in incremental mode
•
Incremental error compensation
•
Backlash compensation
•
Tolerance window blanking
•
Encoder and drive failure detection
•
Maximum Encoder frequency 20 kHz
The unit is suitable for operation with any type of 2 or 3 speed bi-directional drive or any
variable speed drive with 1, 2 or 4 quadrant of control. The performance and accuracy
obtained is dependent on the type of drive chosen. The outputs for stepped speed drives are
transistors.
These outputs can be configured in a number of ways to suit all types of control circuits.
The actual position is monitored by an incremental encoder. The power supply unit can be
integrated. The controller can be used to position machinery to any desired absolute position.
Alternatively, the controller can be used to feed material through a process.
As an Analogue closed loop controller, it has the additional features of :
•
Analogue /- 10 VDC
•
Top speed setting
•
Acceleration/Deceleration rate settings
•
PID term optimisation
•
Go to Datum routines