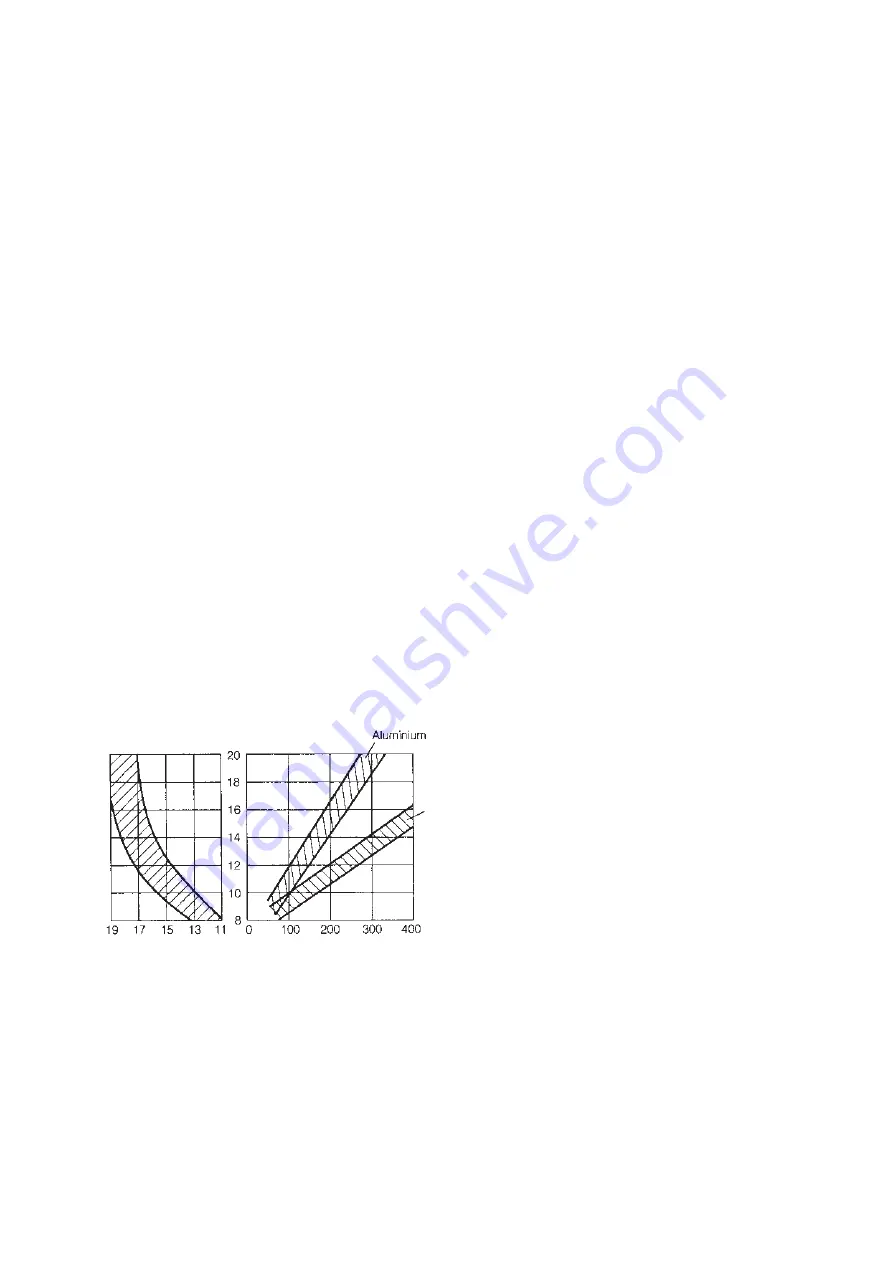
6
Practical Hints for MIG Welding
This distance required between the torch and the workpiece is directly related to the welding current:
●
small current
=
small distance
●
high current
=
greater distance
Too little distance causes excessive wear of the contact tip and gas shroud. Too much distance will not provide
enough gas protection of the welding seam, it becomes porous.
Move the welding gun along the seam in a steady motion, always keeping the same distance between the torch
and workpiece.
Welding may be done either forehand or backhand, in a straight line or, with larger gaps, in a pendulum motion.
MIG welding is suitable for thin plate welding, as well as for welding thicker materials of up to 12 mm.
For thin plate welding we recommend the use of electrode wire of 0.6 mm diameter and a mixed shielding gas.
Welding Preparations
Attach earth clamp to work piece as close as possible to the welding seam (remove rust, paint etc. to ensure good
conducting). Set welding current and wire feed speed with welding step selector and wire feed speed regulator as
required. Make trial runs on scrap material to find correct setting.
6.1 Earth Cable
Connect earth cable plug to Earth Cable Socket on the machine's front panel. Use only genuine Elektra Beckum
parts with recommended cross sections. Structural components, beams, pipes or rails should not be used for earth
conducting, if they are not the actual workpiece. When using welding tables or jigs ensure proper conducting.
6.2 Gas Flow Setting
The correct amount of shielding gas and a steady gas flow at the welding seam are essential to provide sufficient
shielding of the weld pool. Insufficient shielding causes porous welding seams.
Rule of thumb to calculate the shielding gas flow rate required:
Amount of gas in ltr/min = 10 x the electrode wire diameter in mm
Example: Wire diameter 1.0 mm requires a gas flow rate of 10 ltr/min.
Diagram showing the exact gas flow rate required, accounting for different welding current settings
Gas flow rate
in ltr/min
Gas shroud
diameter in mm
Welding current in A
Steel
7
Maintenance
The contact tip and gas shroud are the parts most exposed to the radiant heat of the arc and thus are normal
wearing parts. They have to be cleaned regularly of spatters and sprayed with anti-clogging spray.
Execessive built-up of spatters can short-circuit contact tip and gas shroud, ruining both. Spatter built-up inside
the gas shroud also affects the gas flow to the welding seam.
The machine has to be checked in regular intervals for visible damages.
Dust built-up inside the machine can reduce the duty cycle considerably and may even cause a short circuit. Check
regularly and clean if necessary.
Before removing side panel be sure that machine is disconnected from power supply to prevent injury from electric
shock.