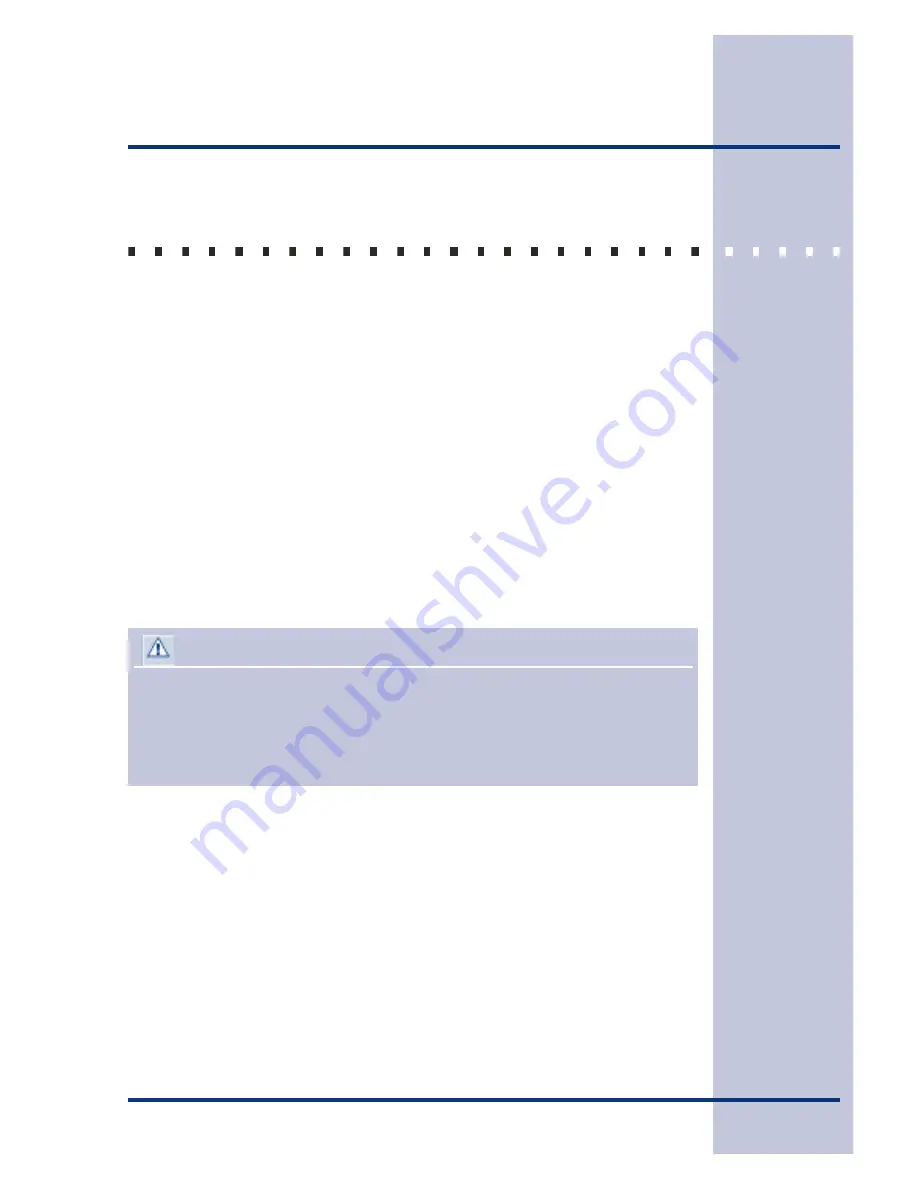
6 5
Section E- Refrigeration System
CONDENSER REPLACEMENT
1.
Disconnect electrical supply to refrigerator.
2.
Remove compressor access panel.
3.
Recover refrigerant by using EPA approved recovery system.
4.
Remove condenser fan mounting screws.
5.
Unplug fan motor harness located in back of fan motor.
6.
Remove fan motor, fan blade, and water valve assembly.
7.
After refrigerant is completely recovered, disconnect inlet and discharge lines
from condenser.
8.
Remove white condenser retainer clip from fan bracket and condenser.
9.
Lift front of condenser and the two rubber groments out of retainer in base
plate.
10. Remove old condenser out the back of cabinet.
11. Install replacement condenser.
12. Remove original filter-drier.
13. Install new filter-drier at end of hot tube.
14. Evacuate and charge the system using recom mended procedure described
under Evacuating and Recharging on pages 27-28.
15. Reassemble unit.
CAUTION
DO NOT unbraze the old filter-drier from the system. This will vaporize and drive
moisture from the desiccant back into the system. The old filter-drier should be cut out
of the system.
Use a Heat Shield to protect plastic tubing when brazing connections.
Summary of Contents for Side by Side Refrigerator
Page 1: ...5995393583 0311 Dishwasher Service Manual Side by Side Refrigerator ...
Page 39: ...32 Section C Diagrams Diagram A Control System ...
Page 41: ...34 SectionC WiringDiagrams ...
Page 42: ...35 Section C Wiring Diagrams ...
Page 55: ...THIS IS A BLANK PAGE ...
Page 112: ...105 Section F Ice Maker ...
Page 113: ......
Page 129: ...THIS PAGE IS BLANK ...
Page 132: ...125 Section H Water System Figure H6 Rear Filter System Front Filter System Figure H5 ...