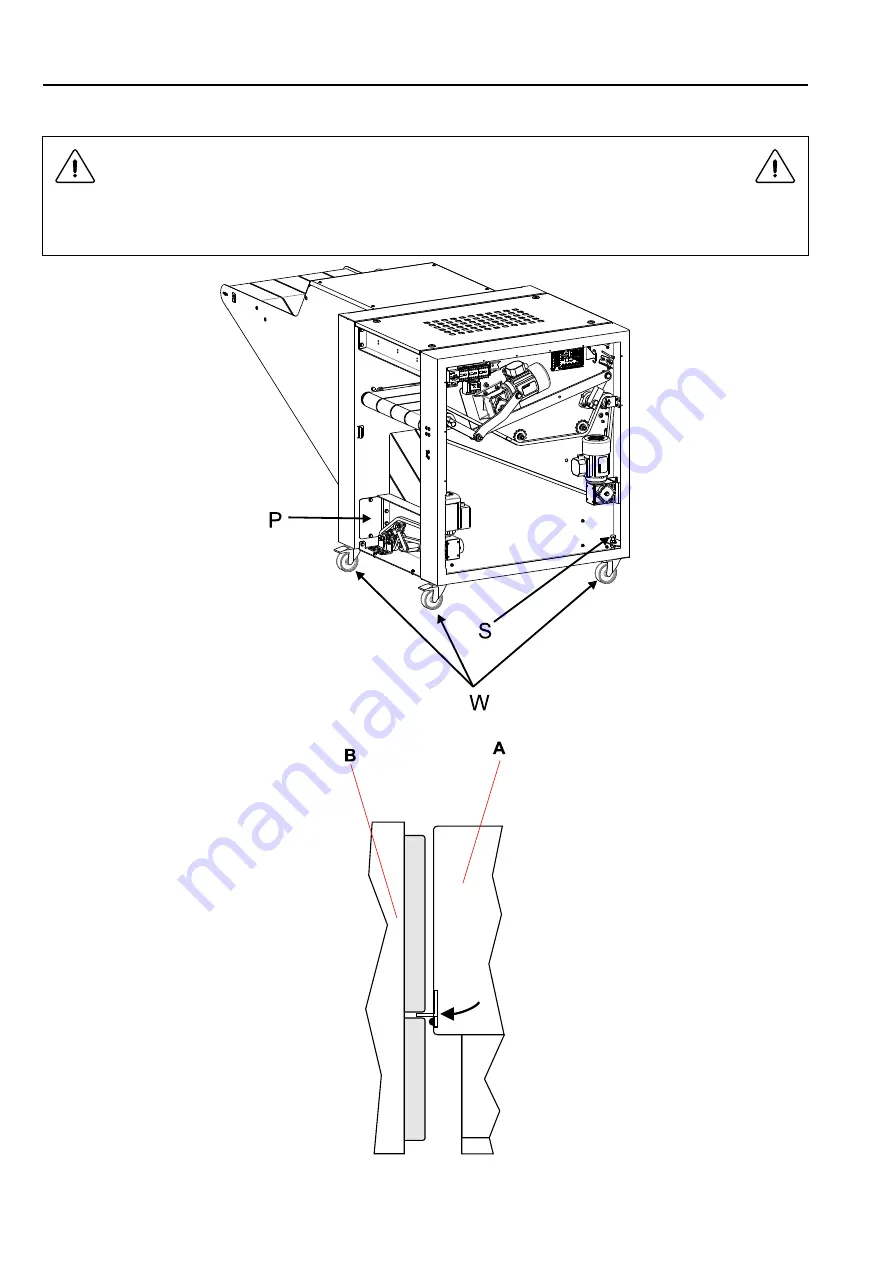
30
Installation manual
3.3
Connection of the stacker
Important
You can adjust the height of the stacker with the ironer by adjusting the screw
(S)
fixing the 4 wheels
(W)
inside
the casing of the stacker. To do this, remove the rear and lateral housings and the plate
(P)
to access to the
screws
(S)
.
Place the stacker (A) on the right of the dryer ironer (B) and centre it with the finger in the slit of the machine.
Lock the stacker in position with the clamping pads.
Summary of Contents for IC6 48 FFS Series
Page 1: ...Installation manual Ironers IC6 48xx FFS Original language 10102059 EN ...
Page 2: ......
Page 15: ...Installation manual 15 ...
Page 29: ...Installation manual 29 Proceed in reverse order in case of transport of the machine ...
Page 34: ...34 Installation manual ...
Page 53: ...Installation manual 53 ...
Page 63: ...Installation manual 63 Important Adjustments should be made by qualified personnel only ...
Page 71: ......