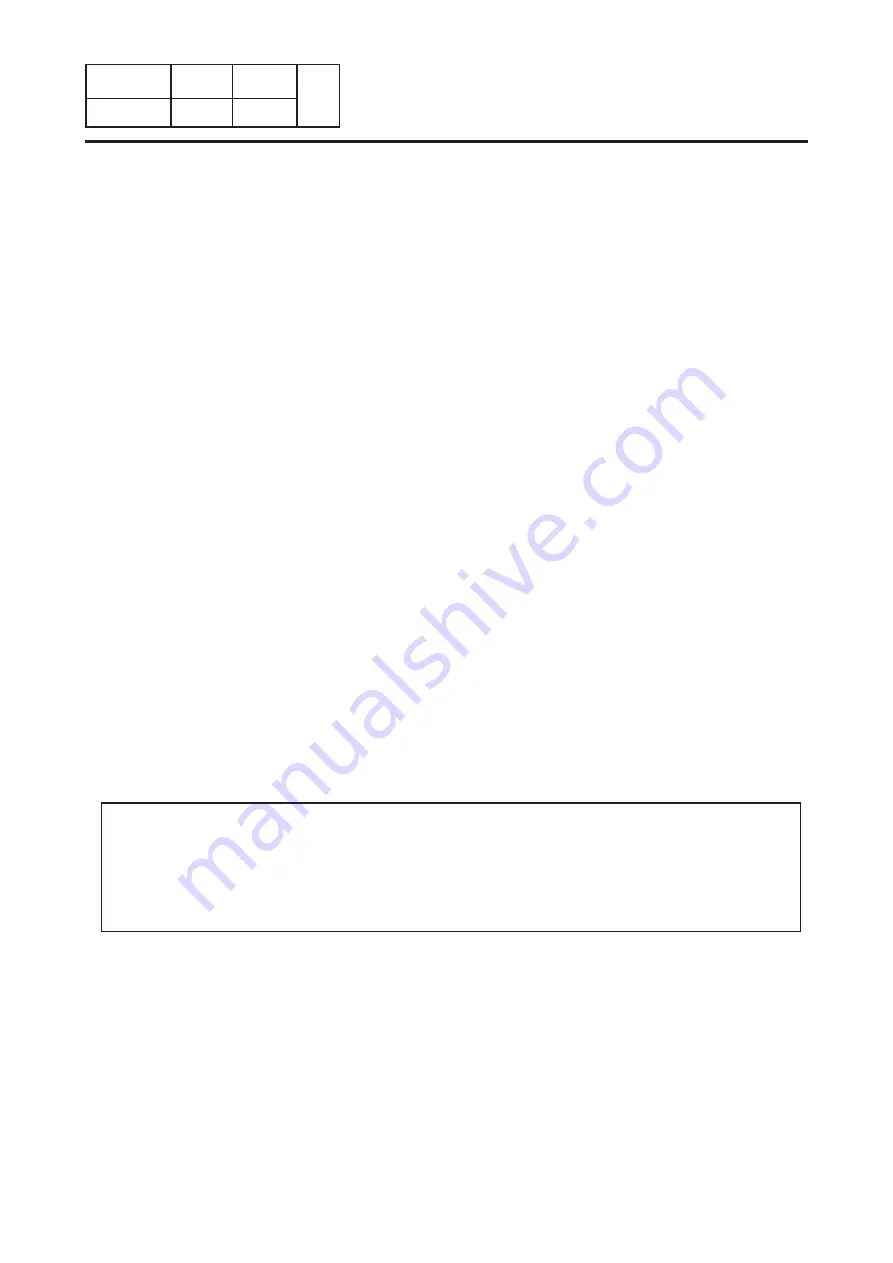
14
6
1511
05306004
Page
Notice
Date
INSTALLATION
MANUAL
Vaporization steam connection (option)
(lettre T on the layout drawing)
Steam supply (¼" BSP) male
Admissible steam pressure 1000 kPa maxi.
This option is to be quoted when the customer already has a steam supply for the laundry. It
then just require to connect the machine to the main steam supply.
The customer must install prior to the machine, a flexible (recommended) steam pipe, and a
stop valve lockable in closed position (1/4 turn valve to be banished).
Autonomous internal steam boiler connection (option)
Water supply connection for the autonomous steam boiler, DN10 (3/8") female
(lettre V on the layout drawing)
This option is to be quoted when the customer is not equipped with a main steam supply for
the laundry.
The customer must install prior to the boiler, a flexible pipe, a filter, and a tap onto the cold
soft water, or hot soft water supply of the laundry.
It is vital that softened water is used to prevent tartar building up around heating equipment.
The hardness of soft water must be 7 and 15 TH (°f).
The water hardness, or total hardness (TH), is expressed in French degrees (°f) or ppm.
One °f is equivalent to 4 mg of calcium per litre and 2.4 mg of magnesium per litre.
Caution: it is not enough to just know the TH to know water’s tartar capacity. This requires
knowledge of all the characteristic parameters of water and complex calculations.
Autonomous boiler purge connection, DN10 (3/8") female
(lettre W on the layout drawing)
The customer must connect the boiler to the waste water collector of the laundry using a tube
and in respect to the local legislation on waste waters.
6. Installation/
Putting into service
Summary of Contents for FC48
Page 1: ...05306004 GB 26 2019 Installation manual Finishing cabinet FC48 Translated from french ...
Page 2: ......
Page 34: ... ...
Page 35: ... ...
Page 36: ...Share more of our thinking at www electroluxprofessional com ...