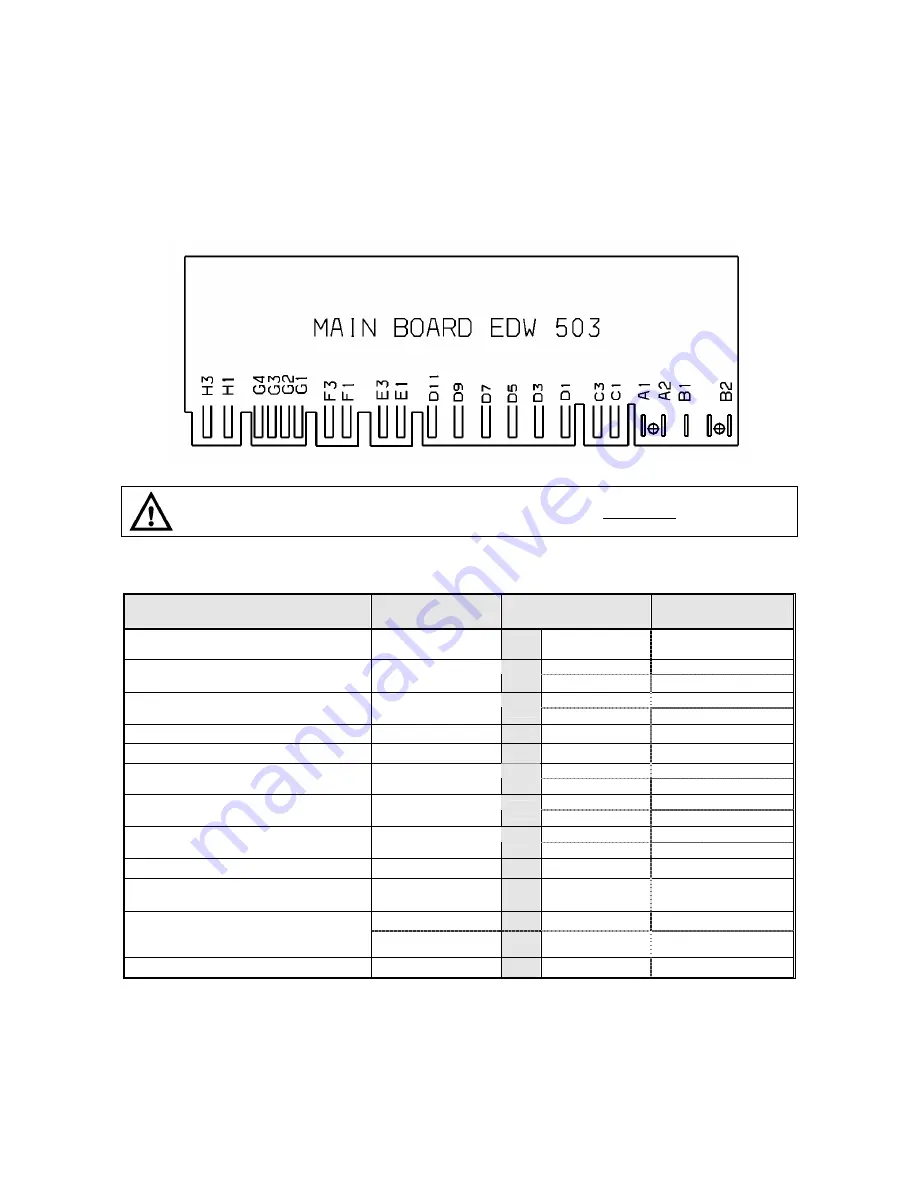
SOI/TD 2005-2 PR
25/26
599 36 83-66
14 CHECKING THE EFFICIENCY OF THE COMPONENTS
In order to facilitate the control procedure for the components to be tested, a TEST PROCEDURE has been
created which indicates the point to which the probes of the tester should be applied and the correct
theoretical value for each component tested.
Remove the door and detach all the connectors from the main board.
Connect the probes of the tester to the appropriate points on the connector. Compare the ohmic reading
with the theoretical value
.
Care should be taken relative to the position of connector "
B1
" - "
B2
": if this connector is
replaced in the incorrect position (back-to-front), the appliance will not function since the power
supply will be disconnected.
14.1 Measurement points on the board wiring connectors
LIST OF COMPONENTS
PROBE
CONTACTS
CORRECT VALUES
NOTES
(RR) - HEATING ELEMENT
+
(TS) - SAFETY THERMOSTAT
A1 D5
25
Ω
±
8%
connected in series
(2100W)
INFINITE
on "EMPTY” (1-2)
(PR) - LEVEL PRESSURE SWITCH
D5 instead of A1
A2
0
Ω
on "FULL" (1-3)
INFINITE
on "EMPTY (1-2)
(PA) - ANTI-FLOODING PRESSURE
SWITCH
D1 B2
0
Ω
on "FULL" (1-3)
(IP) - DOOR MICROSWITCH
C1 C3
0
Ω
Door closed
(DD/DB) - INTEGRATED DISPENSER
E1 E3
1.500
Ω
± 8%
OK
INFINITE
with Rinse-aid
(SB) - RINSE-AID SENSOR
G3 G4
0
Ω
without Rinse-aid
INFINITE
with salt
(SS) - SALT SENSOR
G1 G2
0
Ω
without salt
4850
Ω
± 5%
(at
25ºC)
(ST) - TEMPERATURE SENSOR
H1 H3
1205
Ω
± 5%
(at
60ºC)
(ER) - REGENERATION SOLENOID
C1 D9
6 K
Ω
± 8%
OK
(EC) - FILL SOLENOID
+
(AA) - ANTI-FLOODING DEVICE
D7
C1 instead of D11
3.800
Ω
± 8%
connected in series
D3 D11
50
Ω
± 8%
start-up winding
(PL) - WASH MOTOR
To the 2 motor wires
(bl) / (ro)
180
Ω
± 8%
auxiliary winding
(PS) - DRAIN MOTOR
D1 C1
180
Ω
± 8%
OK