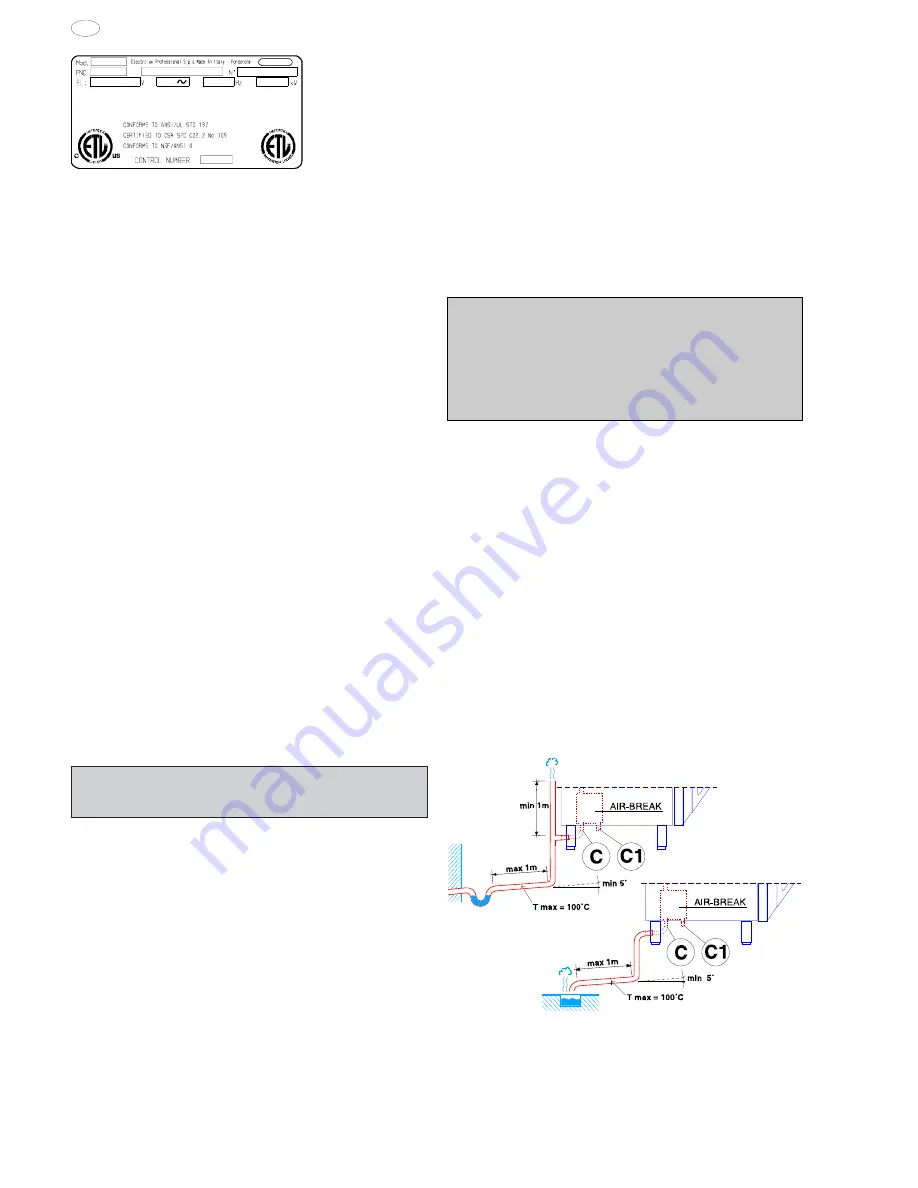
14
USA
5938 035 01
RATING PLATE
3.1 INSTALLING THE POWER SUPPLY CABLE
To access the power supply cable connection terminal board,
proceed as follows:
Model 6 - 10 - 20 GN
• Remove the left side panel.
• Connect the power supply cable to the terminal board accord-
ing to the instructions given in the wiring diagram and fasten the
power supply cable by means of strain-relief fitting (not furnished
with the oven).
Failure to comply with safety rules and regulations relieves
the manufacturer of all liability.
The manufacturer requires when stacking units each appliance
have its own branch circuit protection. An air-o-steam® unit stacked
with an air-o-chill® unit should have a separate protection for the
upper and lower units.
4. WATER MAINS CONNECTION
(Refer to the installation diagrams at the beginning of this booklet).
This equipment is to be installed to comply with the applicable
Federal, State, Local plumbing codes, or the Basic Plumbing
Code of the Building Officials and Code Administrators
International Inc. (BOCA) and Food Service Sanitation Manual
of the Food and Drug Administration (FDA).
When connecting the appliance to the water system with
flexible tubes they must be new and not used.
The appliance is fitted with two separate water inlets ("B" and "N").
The water lines supplying both inlets must be fitted with a
mechanical filter and shut-off valve (keeping with local plumbing
codes).
Before fitting the filters allow the water to flow out for sufficient time
to flush any solid particles from the piping.
4.1 WATER SUPPLY CONNECTIONS
4.1.1 WATER INLET "N".
Attention
The water supply pipe (supplied) must have a 3/4" dia (20 mm)
pipe and must be without elbow fittings.
The steam condensation system must be connected to a cold
quality water supply in keeping with local plumbing codes, with
the following characteristics:
-
total hardness:
total hardness:
up to 400ppm (40°fH); in
ovens equipped with CLEANING SYSTEM it is advisable to use
water of hardness no higher than 50ppm (5°fH).
-
pressure:
22 to 36 psi (150-250 kPa); higher pressure
values result in increased water consumption.
Note:
To check correct water installation, make sure the rotating wash
arm (CLEANING SYSTEM) does not turn below 100 rpm (120
max).
4.1.2 WATER INLET "B".
(water pipe supplied)
The steam production system must be connected to a quality
water supply in keeping with local plumbing codes, with the
following characteristics:
-
total hardness:
5 - 50ppm (0.5 - 5
°fH)
to reduce the build-
up of lime-scale inside the boiler.
On request the oven is supplied with an optional water softener
with automatic regeneration which must be installed on inlet line
"B". This device can also be fitted with an optional resin sanitizer
kit.
-
pressure:
22 to 36 psi (150-250 kPa); higher pressure
values result in increased water consumption.
-
chlorine ion concentration (Cl -)
: not more than ~10 ppm
(acceptable value) to avoid damaging the oven's internal steel
parts.
-
pH:
over 7.
The oven can be equipped with an optional special filtration unit
which is installed on inlet line "B". This unit also acts as a water
softener, reducing water hardness to less than
50ppm (5
°fH)
(optimum value).
-
electrical conductivity:
50 to 2000 µS/cm (68°F)(20°C).
Important
: The use of water treatment systems featuring
technology that differs from that of the systems supplied by the
manufacturer is prohibited and will automatically invalidate the
warranty.
The use of dosing systems designed to prevent the build-
up of lime-scale in pipes (i.e. polyphosphate dosing
systems) is also prohibited since such systems may impair
the performance of the appliance.
4.2 WATER DRAIN SYSTEM
- OVEN level A -
The oven is supplied with an air-break system to prevent any
backflow from the drainage system from reaching the oven’s inter-
nal circuits and the cooking chamber. The presence of this system
means that the drain pipe can be connected directly to the mains
drainage system or routed to a floor gulley with grating.
The flexible drainage hose or rigid pipe can be directed to the
side or rear of the appliance if the oven is not positioned against
a wall; this line must not be directed towards the front of the
appliance to prevent interference with roll-in grid racks. The drain-
age pipe internal diameter must be no smaller than the oven
drain outlet (1 1/4"),
no longer than 3 feet (1 metre)
and must
resist temperatures of up to at least 212°F (100°C). Avoid re-
strictions in the case of flexible hose pipes, do not fit elbows on
metal pipes anywhere along the drainage line. Also avoid
horizontal sections in which water might collect (minimum gra-
dient 5%).
WARING: BLOCKING THE DRAIN IS HAZARDOUS.
C
-
Oven drain
C1
-
Safety outlet
Important:
-
Do not obstruct the safety outlet
C1
.
- Do not connect the safety outlet
C1
to the drainage system.
Note:
If water comes out of the AIR-BREAK (safety outlet C1) this means
the drain C is blocked. Any elimination of the obstruction
must
be carried out by specialised technical personnel.