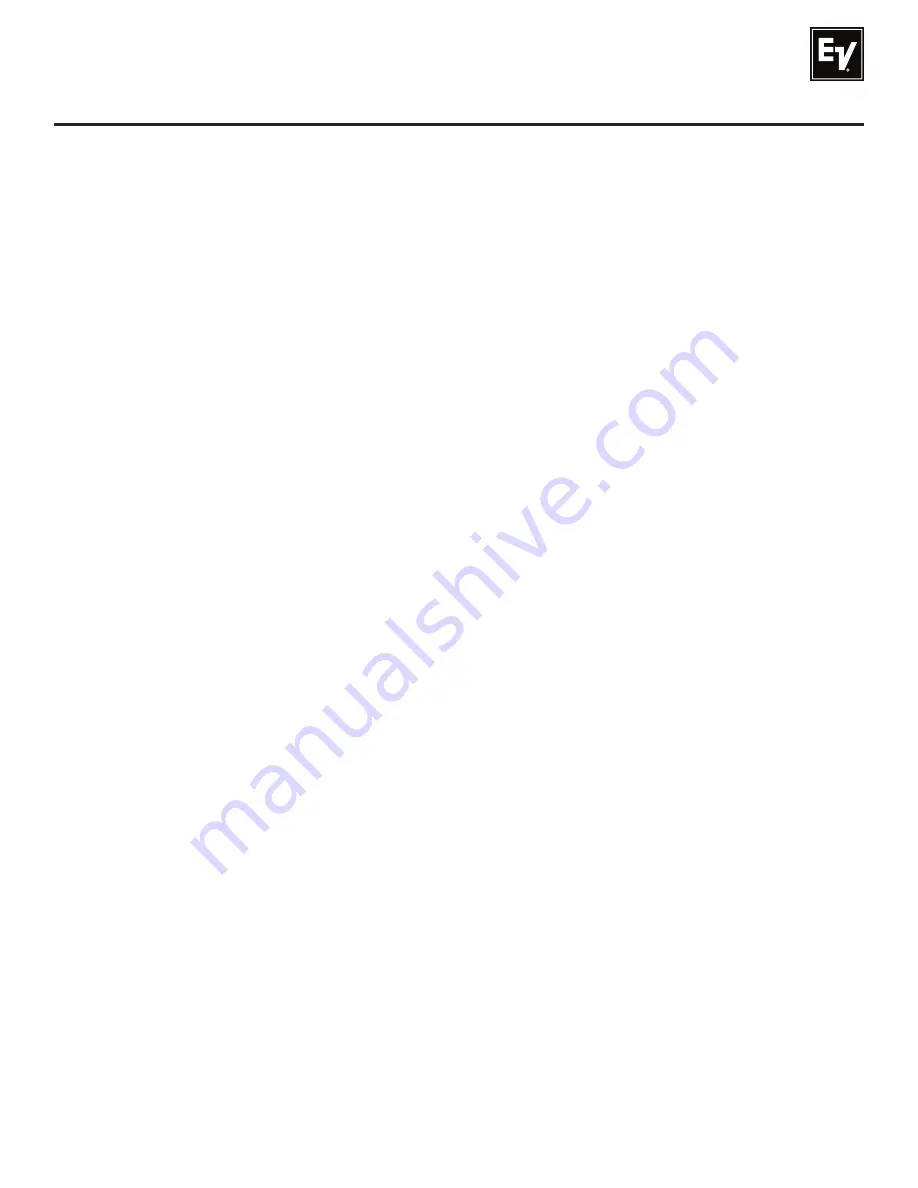
Electro-Voice XLC Touring Addendum
25
4. Rigging Inspection and Precautions
Extender Beam Assembly:
Prior to each use, inspect the XLC-EB assemblies for any cracks, burrs,
deformations, corrosion or missing or damaged components that could reduce the XLC-EB assembly
strength. Replace any XLC-EB assemblies that are damaged or missing hardware. Always double check
that each XLC-EB assembly is securely locked to the spreader bar(s) on the grids below. Always double
check that that each quick-release pin in the frame and yoke assemblies are securely locked into place.
Never exceed the limitations or maximum recommended load for the XLC-EB assemblies.
Chain Hoists:
Prior to each use, inspect the chain hoist and associated hardware (including motor, if
applicable) for any cracks, deformation, broken welds, corrosion, missing or damaged components that
could reduce the hoist strength. Replace any damaged chain hoists. Never exceed the limitations or
maximum recommended load specified by the hoist manufacturer. Always follow manufacturers’ recom-
mendations for operation, inspection, and certification. Always raise and lower the load slowly and evenly,
avoiding any rapid changes in speed or shifting loads that could result in a sudden jolt to the suspended
system.
Building, Tower or Scaffold Supports:
Prior to each use, the strength and load-bearing capabilities
of the building, tower or scaffold structural supports should be evaluated and certified by a professional
engineer as being adequate for supporting the intended rigging system (including the loudspeakers, grids,
chain hoists and all associated hardware). Prior to each use, inspect the building, tower or scaffold struc-
tural supports for any cracks, deformation, broken welds, corrosion, missing or damaged components that
could reduce the structural strength. Damaged structural supports should be replaced or repaired and
recertified by a professional engineer. Never exceed the limitations or maximum recommended load for the
supports.
Miscellaneous Mechanical Components:
Prior to each use, inspect all mechanical components
(chain, wire ropes, slings, shackles, hooks, fittings, ratchet straps, etc.) for any cracks, deformation, broken
welds, slipping crimps, fraying, abrasion, knots, corrosion, chemical damage, loose screws, missing or
damaged components that could reduce the maximum strength specified by the component manufacturer.
Replace any damaged mechanical components. Never exceed the limitations or maximum recommended
load for the mechanical components.