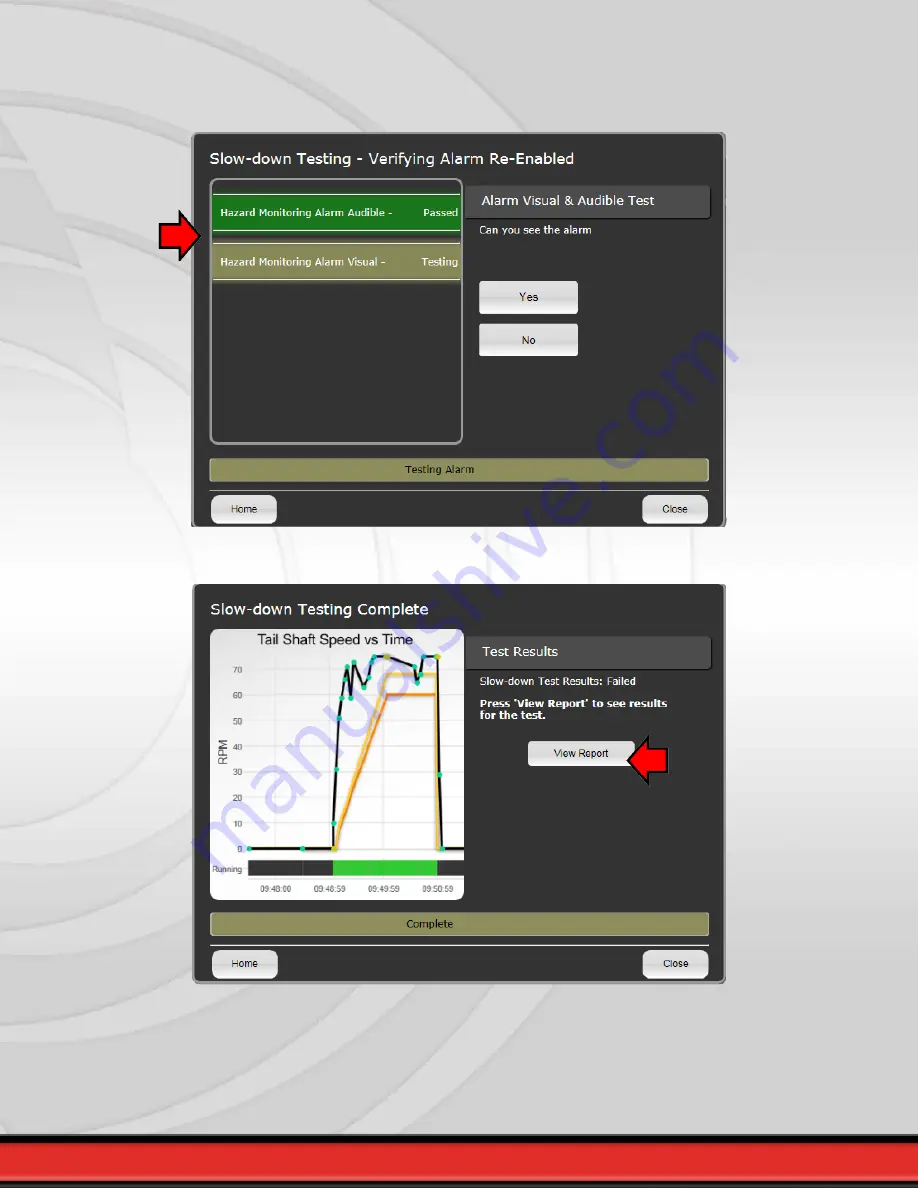
2
Slow-Down Testing: Alarm Re-Enableing
Slow-Down Testing Completion Screen
1.
This screen shows a second alarm condition to confirm correct operation.
2. When you see the page showing the speed plotted on the graph it means that
your test is complete. A Testing Report will automatically be generated showing
the results of your Slow-Down Test. To view your Testing Report click the “View
Report” button.
Note:
To view an example refer to (Page 39).
1
2
Figure 38
Figure 39
Page 37