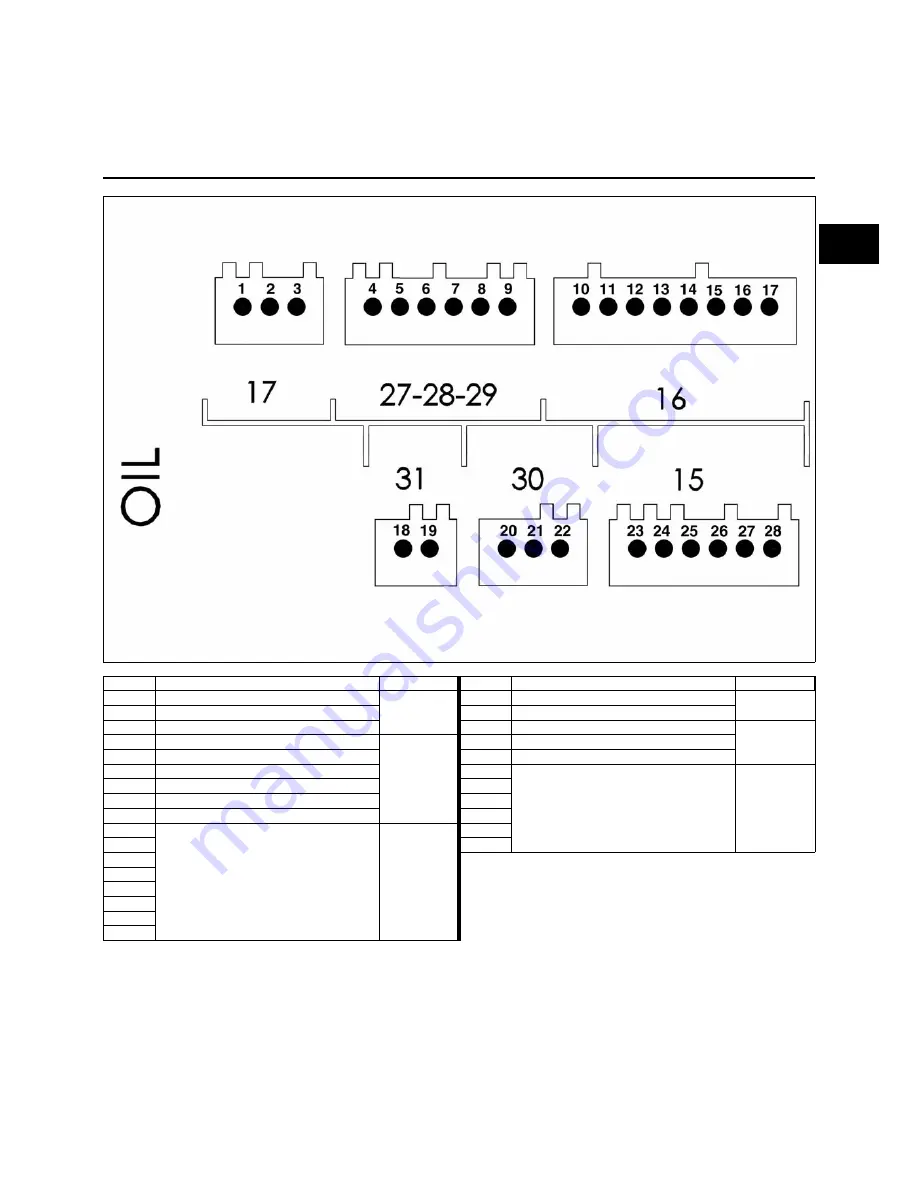
11/2010 - Art. Nr. 4200 1029 8600A
9
Display-PC interface
Air flap servomotor
Connector
Terminal
Terminal
Connector
Terminal
Description
Connector
Terminal
Description
Connector
1
Not used
17
18
Not used
31
2
Not used
19
Not used
3
Not used
20
Not used
30
4
Not used
27
28
29
21
Not used
5
Not used
22
Not used
6
Not used
23
Air flap servomotor
15
7
Not used
24
8
Not used
25
9
Not used
26
10
Display-PC interface
16
27
11
28
12
13
14
15
16
17
Operation
Terminal allocation chart
Low voltage connections
en