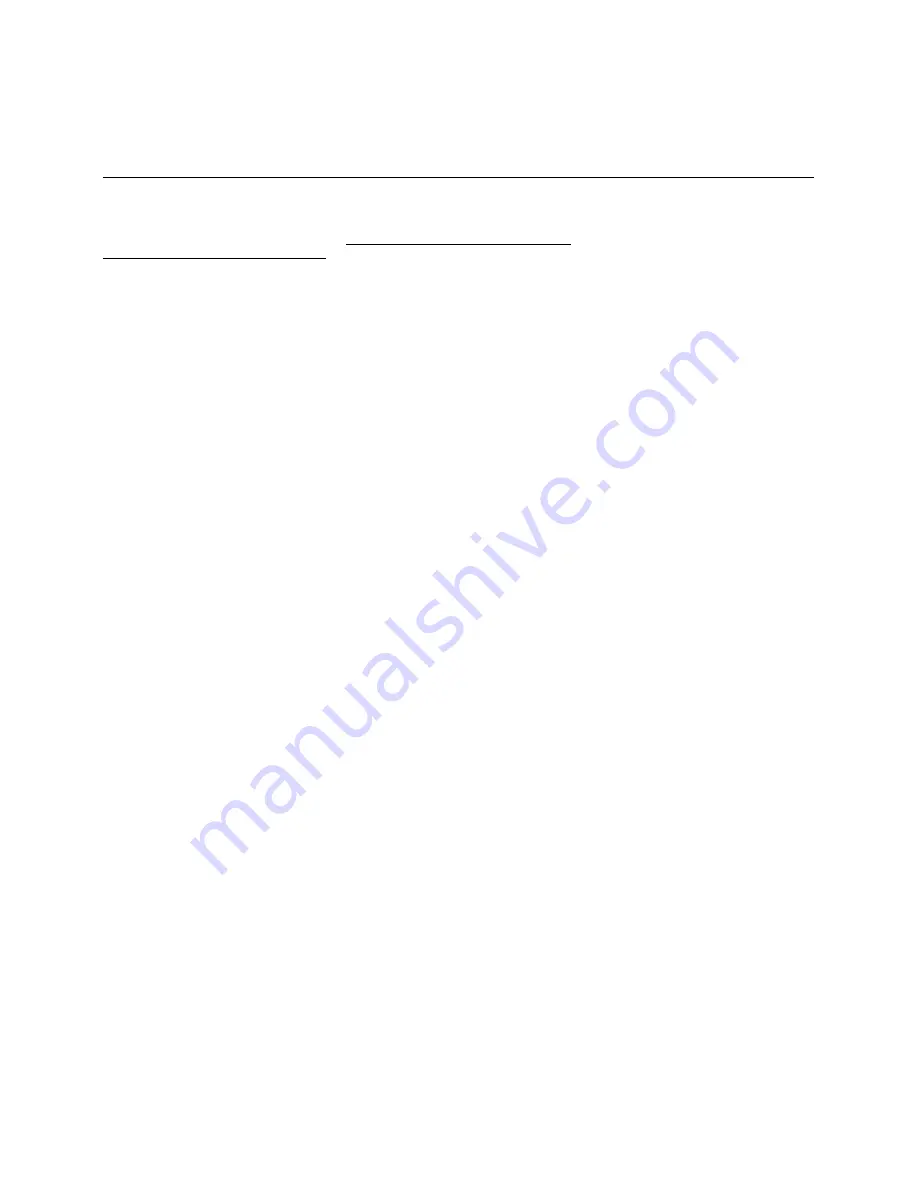
10/2010 - Art. Nr. 4200 1030 6900A
24
Servicing
Exhaust gas test
Trouble shooting instructions
6. Cleaning and lubricating
instructions
Depending on the amount of dirt
introduced by the combustion air it will
be necessary to clean the fan impeller,
ignition electrodes, flame sensors and
air dampers as required.
For burner with mechanical compound
controller:
Lubricate the compound controller
setting screws with grease.
The bearing points of the burner moving
parts require no maintenance. Damages
of ball bearings should be detected and
eliminated at an early stage to avoid
greater subsequent trouble. Listen to the
motor bearing noise to identify possible
irregularities.
4. Mixing unit gives poor
combustion data
Cause
Remedy
Incorrect
settings.
Correct settings.
Incorrect mixture
ignition unit.
Replace unit.
High or low
combustion air
flow rate.
Readjust burner.
Furnace
chamber not
sufficiently
ventilated.
Furnace
chamber to be
ventilated
through a non-
closed opening
with a cross
section of min.
50 % of all
chimney cross
sections of the
furnace system.
Take care to
observe the
application
regulations.
5. Solenoid valve fails to open
Cause
Remedy
Defective coil or
SKP actuator.
Replace coil or
SKP actuator.
Defective
automatic
furnace
controller.
Replace
automatic
furnace
controller.
Valve does not
close tightly; dirt
accumulated on
sealing surfaces.
Open valve;
remove foreign
matter; replace
valve if required.