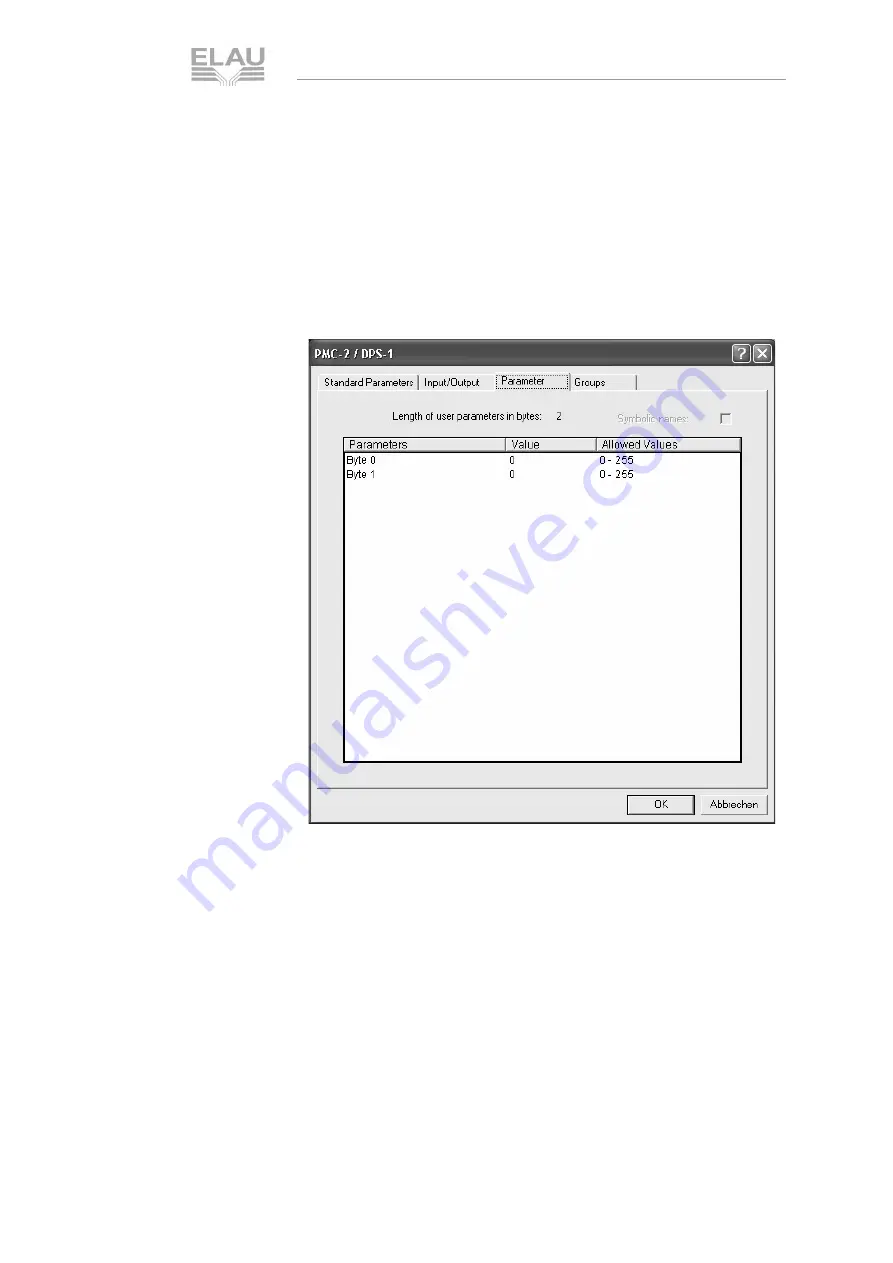
P
D
M
_
OpM
a
P
rof
i_06_us
.f
m
PacDrive™ M
field bus PROFIBUS-DP
page 33
6.3 PROFIBUS-DP Master
Ko
rr
ek
tu
ra
us
dr
uc
k
In some modules a “symbolic name“ is saved for the value. This
display of this symbolic name can be activated by a tick behind
Symbolic name.
Parameters described in plain text can be modified by a double
click or a by single click and the right mouse button.
Numerical parameters can be entered by selecting them and then
clicking with the left mouse button.
Parameters
Fig. 6-16: Configuring the PROFIBUS-DP slave / Parameters / Without plain-text
description
The parameters can be entered numerically in decimal code, by
selecting them and then clicking again (no double click).
Summary of Contents for PacDrive M
Page 8: ...PDM_VerwendStd_us FM page 8 PacDrive M 2 Use of This Operating Manual Korrekturausdruck...
Page 84: ...PDM_OpMaProfiAen_us FM page 84 field bus PROFIBUS DP PacDrive M Korrekturausdruck...
Page 86: ...PDM_OpMaProfibus_usSIX fm Seite 86 field bus PROFIBUS DP PacDrive M Index Korrekturausdruck...