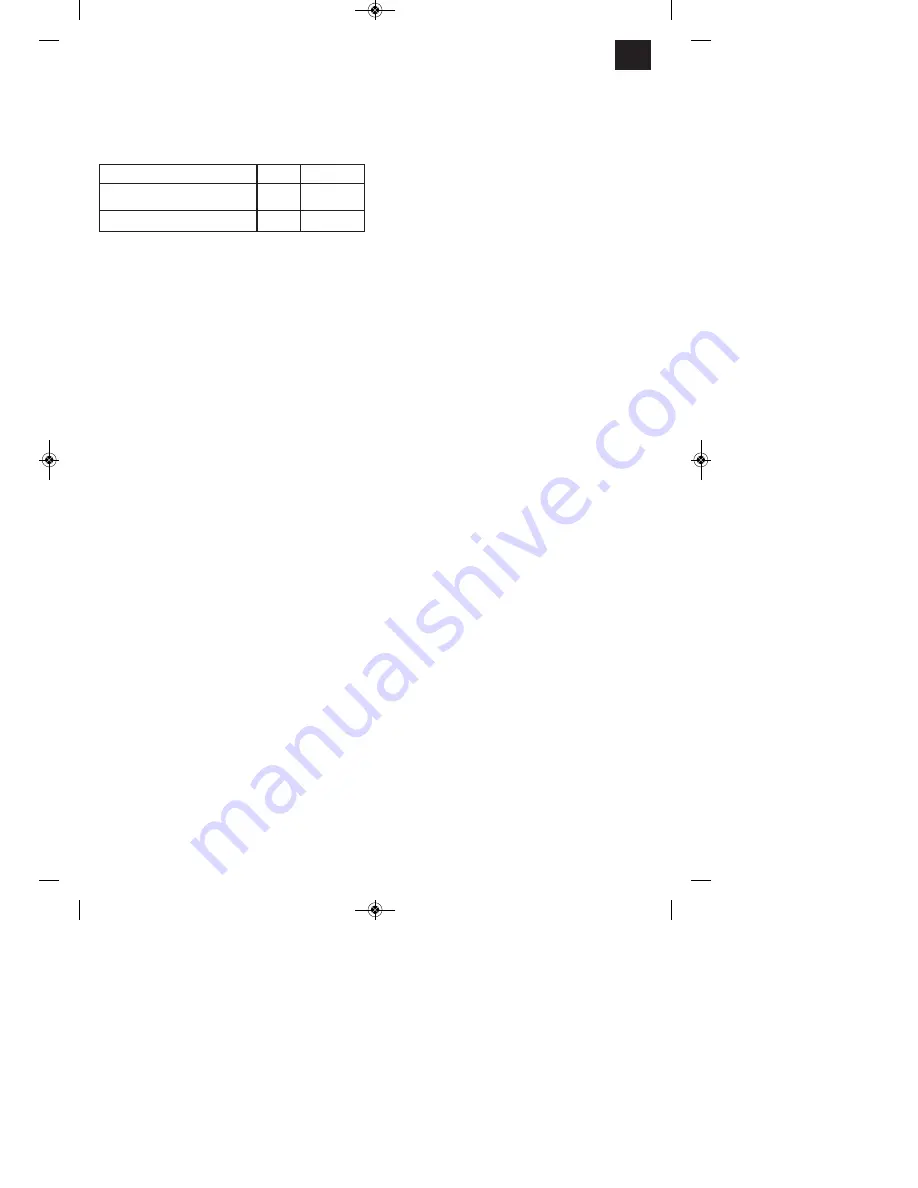
21
GB
5.2 Gas connection (Fig. 4, 5, 22-27)
5.2.1 Gas types
Gas shielding is required for welding with continuous
wire, the composition of the shielding gas depends on
the welding method you wish to use.
5.2.2 Fitting the gas bottle on the unit (Fig. 22-23)
The gas bottle is not supplied.
Fit the gas bottle as shown in Figures 22 – 23. Ensure
that the belt strap (15) is secure and that the welding
set cannot tip over.
Important. Only gas bottles with a maximum capacity
of 10 liters may be fitted on the gas bottle support
area (Fig. 23/5). If you wish to use larger gas bottles,
there is a risk that they will tip over and therefore they
may only be placed next to the unit. In this case the
gas bottle must be secured to prevent it tipping over.
5.2.3 Connecting the gas bottle (Fig. 7, 24-27)
After removing the protective cap (Fig. 24/A), open
the bottle valve (Fig. 24/B) briefly, ensuring it is
pointing away from your body.
Clean any dirt off the connecting thread (Fig. 24/C) if
necessary using a dry cloth without adding any
cleaning products. Check whether there is a seal on
the pressure reducer (19) and that it is in perfect
condition. Turn the pressure reducer (19) clockwise
on to the connection thread (Fig. 25/C) on the gas
bottle (Fig. 25). Place the two hose clips (j) over the
shielding gas hose (18). Connect the shielding gas
hose (18) to the shielding gas hose connection (23)
on the pressure reducer (19) and gas supply
connector (16) on the welding set and secure it to
both connectors using the hose clips (j). (Fig. 26-27)
Important. Check all gas and other connection for
leaks. Check the connections using leak spray or
soap suds.
5.2.4 Information about the pressure reducer
(Fig. 4/19)
The gas delivery rate can be adjusted using the rotary
knob (24). The set gas delivery rate can be read off
the pressure gage (20) in liters per minute (l/min). The
gas is discharged at the shielding gas hose connector
(23) and is then forwarded to the welding set through
the shielding gas hose (Fig. 3/18). (see 5.2.3)
Important. Always proceed as described in point 6.1.3
for setting the gas delivery rate.
The pressure reducer is fitted on the gas bottle using
the screw connector (21) (see 5.2.3).
Important. The pressure reducer may only be
adjusted and repaired by trained personnel. Send
defective pressure reducers to the service address if
necessary.
5.3 Mains connection
Before you connect the equipment to the mains
supply make sure that the data on the rating plate
are identical to the mains data.
The equipment may only be operated from
properly earthed and fused shock-proof sockets.
5.4 Fitting the wire spool (Fig. 1, 5, 6, 28 – 36)
The wire spool is not supplied.
5.4.1 Wire types
Various welding wires are required for different
applications. The welding set can be used with
welding wires with a diameter of 0.6 and 0.8 mm. The
appropriate feed rollers and contact tubes are
supplied with the set. The feed roller, contact tube and
wire cross-section must always match each other.
5.4.2 Wire spool capacity
Wire spools with a maximum weight of 5 kg can be
fitted in the welding set.
5.4.3 Inserting the wire spool
Open the housing cover (Fig. 1/4)
Check that the windings on the spool do not
overlap so as to ensure that the wire can be
unwound evenly.
Description of the wire guide unit (Fig. 28-36)
A Spool
lock
B Spool
holder
C Cam
pin
D Adjusting screw for roller brake
E Screws for feed roller holder
F Fee roller holder
G Feed
roller
H Hose package mounting
I Pressure
roller
J
Pressure roller holder
K Pressure roller spring
L
Adjusting screw for counter-pressure
M Guide
tube
N Wire
spool
O Cam opening in wire spool
Shielding gas
CO2
Argon/CO2
Metal to be welded
Non-alloyed steel
X
X
Anleitung_BT_GW_150_SPK1__ 23.01.13 07:26 Seite 21