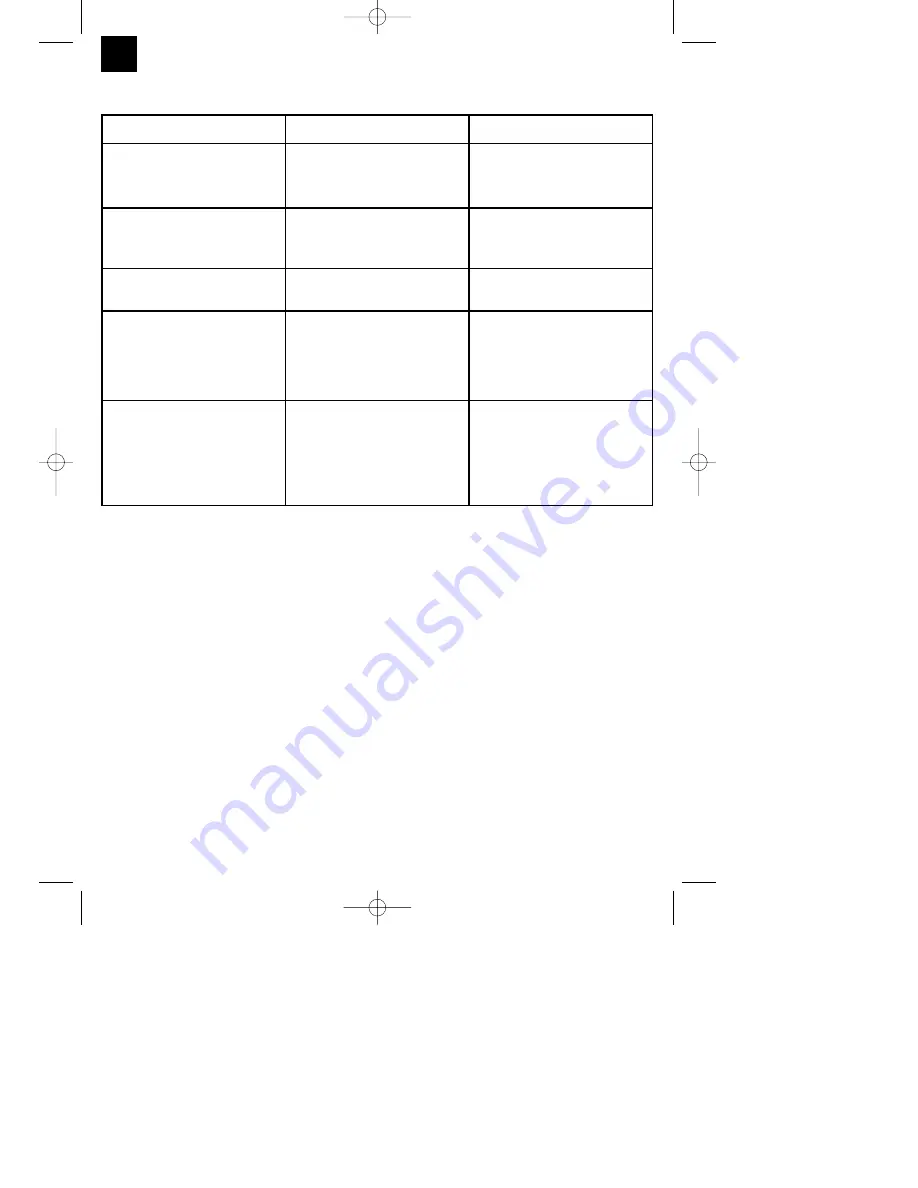
8
GB
Faults
Cause
Remedy
The equipment does not start
-
Power supply not connected
-
Floating switch does trigger
-
Check power supply
-
Raise position of floating switch
The equipment does not pump
-
Intake sieve clogged
-
Discharge hose kinked
-
Clean intake sieve with water jet
-
Unkink the hose
The equipment does not cut out
-
Floating switch cannot sink
-
Place equipment correctly on
shaft bottom
Insufficient pumping rate
-
Intake sieve clogged
-
Performance reduced due to
heavily contaminated and
abrasive water impurities
-
Clean intake sieve
-
Clean equipment and replace
wear parts
The equipment switches off after
briefly running
-
Motor circuit-breaker switches
the equipment off due to
excessive water contamination
-
Water temperature too high;
motor circuit-breaker switches
the equipment off
-
Unplug power plug and clean
equipment and shaft
-
Ensure that maximum
permissible water temperature
(35 °C) is not exceeded
10.
Troubleshooting guide
Anleitung_BG_SP_400_RB_SPK1:_ 04.07.2008 11:04 Uhr Seite 12
Summary of Contents for 400 RB
Page 4: ...4 8 7 5 A B 5 Anleitung_BG_SP_400_RB_SPK1 _ 04 07 2008 11 04 Uhr Seite 4...
Page 10: ...EH 04 2012 02...
Page 11: ...EH 04 2012 02...
Page 12: ...EH 04 2012 02...