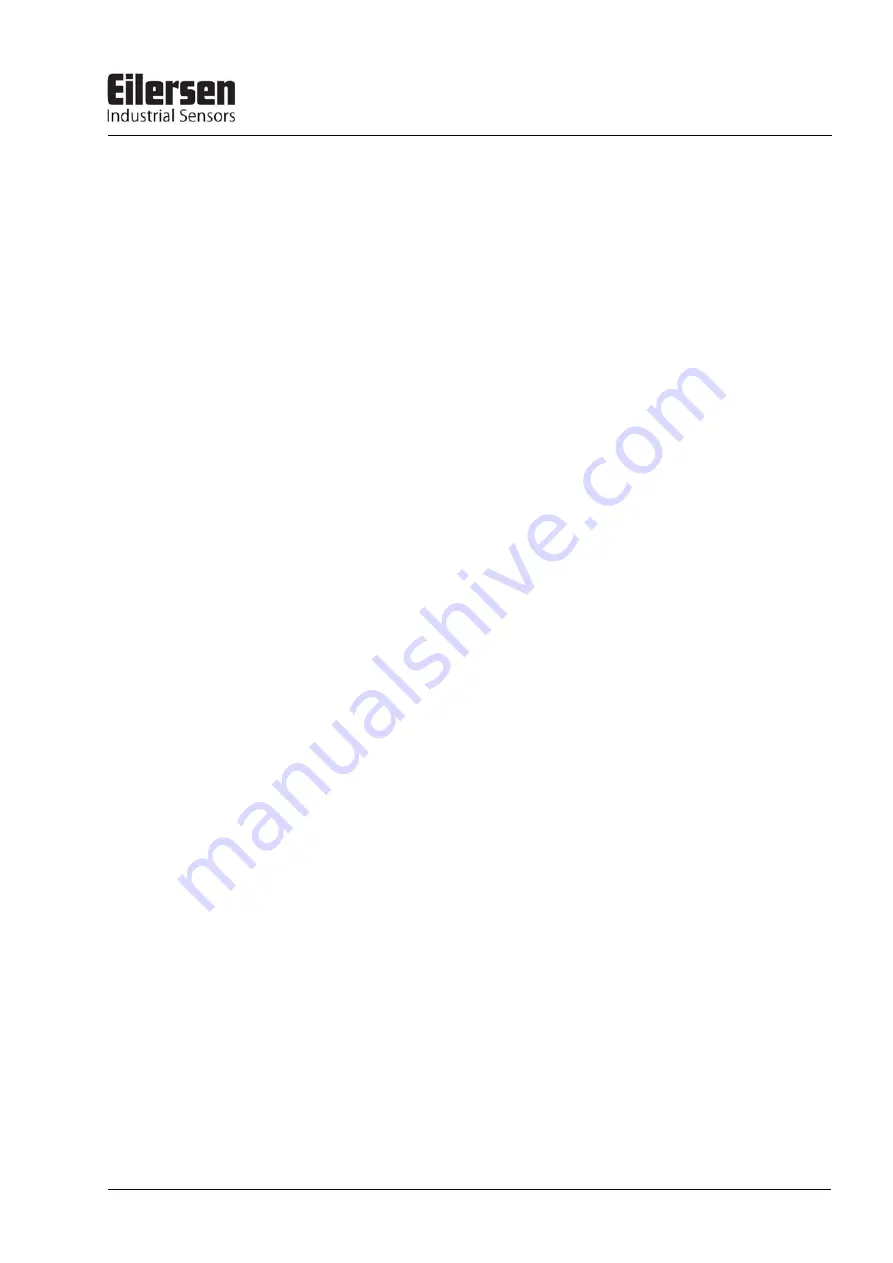
MCE2035: User manual
Version: 2011-05-17, rev.: 0a
Page: 13
6.1.3 Calculation of uncalibrated system weight
Based on the load cell gross values (
LcGross[x]
or
LcGrossCal[x]
), whether they are
corner calibrated or not, a uncalibrated system weight can be calculated as either:
Gross = LcGross[X1] + LcGross[X2] + …
or:
Gross = LcGrossCal[X1] + LcGrossCal[X2] + …
6.1.4 System
calibration of weighing system
Based on the uncalibrated system weight a system calibration can be made as follows:
1)
Check that the weighing arrangement is empty. Zero the weighing system.
2)
Place a known load (
CalLoad
) on the weighing arrangement.
NOTE:
In order to
achieve a correct calibration of the system it is recommended, that the used cali-
bration load is at least 50% of the system capacity.
3)
Calculate the calibration factor that should be multiplied on the uncalibrated sys-
tem weight in order to achieve correct showing as:
CalFactor = (CalLoad)/(Actual Gross)
After this the determined calibration factor is used to calculate the calibrated sys-
tem weight as follows:
GrossCal = CalFactor * Gross
If the determined calibration factor falls outside the interval 0.9 to 1.1 it is very
likely that there is something wrong with the mechanical part of the system. This
does not however apply to systems, which do not have a load cell under each sup-
porting point. For example on a three legged tank with only one load cell, you
should get a calibration factor of approximately 3 because of the two “dummy”
legs.