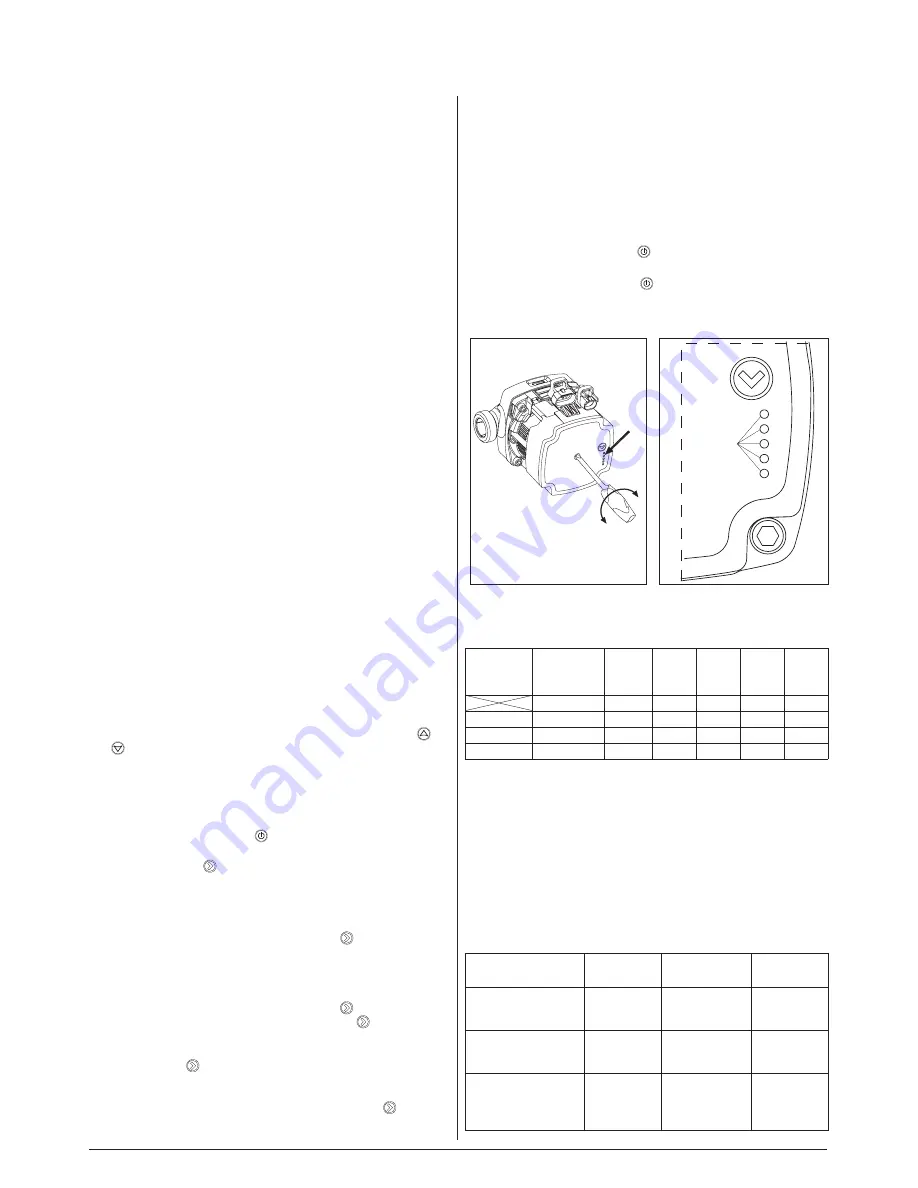
6
GB-031C_f.625
InsTallaTIOn
14. system protection
Failure to protect the system will invalidate the manufacturer’s
warranty.
After the system has been installed the cleansing and inhibiting
procedure must be carried out as follows:
Procedure:
1. Fill the system with cold mains water to the recommended
pressure 1.5 bar and check for leaks, then drain the system
thoroughly making sure all drain cocks are fully open and that
the system is completely drained.
2. Add Fernox Heavy Duty restorer through the header tank or
via filling loop at the recommended dose. One bottle must be
used as a minimum per dwelling. If you are unsure of the cor-
rect dose rate, contact Fernox.
3. Re-fill the system and circulate the Heavy-Duty Restorer prior
to the boiler being fired up, then commission the system in
the normal way. The cleansing agent must be in the system
for a minimum 1 hour with the system at normal operating
temperature. A longer period of time would be more beneficial
to the cleansing process especially if excess flux was used.
4. Drain and flush the system thoroughly to remove the cleaning
agent and any debris or contaminant. This is a critical part of
the cleaning process and must be carried out correctly. Use a
rinse test meter (TDS), such as the Fernox CTM. The reading
must be within 10% of the mains ppm value.
5. Then add the Fernox Protector (Copal MB1 or Super concen-
trate). This will protect against the formation of scale, corrosion
and microbiological growths. It is crucial however, that for
the protector to work correctly, the system must be properly
cleansed and flushed.
6. The label included within the Fernox Protector carton should
be completed and attached adjacent to the boiler.
7. We recommend inhibitor levels are checked on an annual basis
(usually during the service) or sooner if the system content is
lost. This should be carried out using a Fernox inhibitor Test
Kit.
8. Fernox Technical Service Helpline on 0870 870 0362 for further
assistance.
15. start-up / Commissioning
1. Ensure the system is filled with water and correctly vented.
2. Check if the appropriate system installation pressure is
reached(see the “TECHNICAL DATA” section). By using or
but-tons whilst the control panel is off, the pressure value
will be displayed. When the installation pressure is too low The
“A’’indicator flickers (see “Operating’’ section). This doesn’t
concern open vented system installations.
3. Set the external controls to call for heat. Disconnect the flow
sensor wiring plug on the control panel.
4. Switch the boiler on (press button).
5. Check the pump is set to the correct mode (see table below).
Todo this, press button for no more than 2 seconds. The
LED’sshould signal an operating mode at the place pointed by
arrow.
6. If the LEDs are signaling a different operating mode than rec-
ommended in the table below, set the appropriate mode ac-
cording to the following instructions: press button for longer
than 2 seconds, but less than 10 seconds (LED’s will start to
flash),the pump then switches to the settings mode. LEDs glows
to indicate the current settings. To change the settings of the
pump in accordance with the table below, you can set the right
combination of glowing LEDs by pressing
the button. Once
LED combination is set correct, by not pressing
the button for
10 seconds the pump will remember this setting and will exit
from setting mode back to performance view.
note: holding
button for more than 10 seconds will enter the
pump into key lock mode. this prevents the user from altering
the pump settings. To remove the key lock the pump settings and
allow the pump settings to be changed, hold button
again for
more than 10 seconds.
7. Ensure adequate flow through the boiler is reached (the
„H”indicator is on with a constant light). The pump should
self vent after a short period of running. if necessary assist the
venting process in the following way;
Warning the screw head
in the centre of the pump is not intended to be used to assist
venting of the pump, Damage to the pump internals may oc-
cur!
• close the isolation valve on the outlet,
• leave boiler running for 15 sec.
• open the isolation valve.
8. Switch the boiler off (hold button for 3 seconds).
9. Reconnect the flow sensor plug to the control panel.
10. Switch the boiler on (press button).
11. Set the boiler to the required system temperature, see the “Op-
erating” section.
Figure 2
Figure 3
LED
1
2
3
4
5
LED
Rated
power
[kW]
Pump lifting
height [m]
LED 1
red
LED 2
yellow
LED 3
yellow
LED 4
yellow
LED 5
yellow
4
●
●
6-9
5
●
●
●
9-12
6
●
●
●
●
14 - 24
7
●
●
●
alarm status
If the pump has detected one or more alarms, the bicolored LED 1
switches from green to red. When an alarm is active, the LEDs indi-
cate the alarm type as defined in the table below. If multiple alarms
are active at the same time, the LEDs only show the error with the
highest priority. The priority is defined by the sequence of the table.
When there is no active alarm anymore, the user interface switches
back to operation mode.
Display
Indication
Pump
operation
Counter
action
One red LED + one
yellow LED (LED 5)
Rotor is
blocked.
Trying to start
again every 1,5
seconds
Wait or
deblock the
shaft.
One red LED + one
yellow LED (LED 4)
Supply volt-
age too low
Only warning
pump runs
Control the
supply volt-
age
One red LED + one
yellow LED (LED 3)
Electrical
error
Pump is stopped
because of low
supply voltage or
serious failure
Control the
supply voltage
/Exchange the
pump