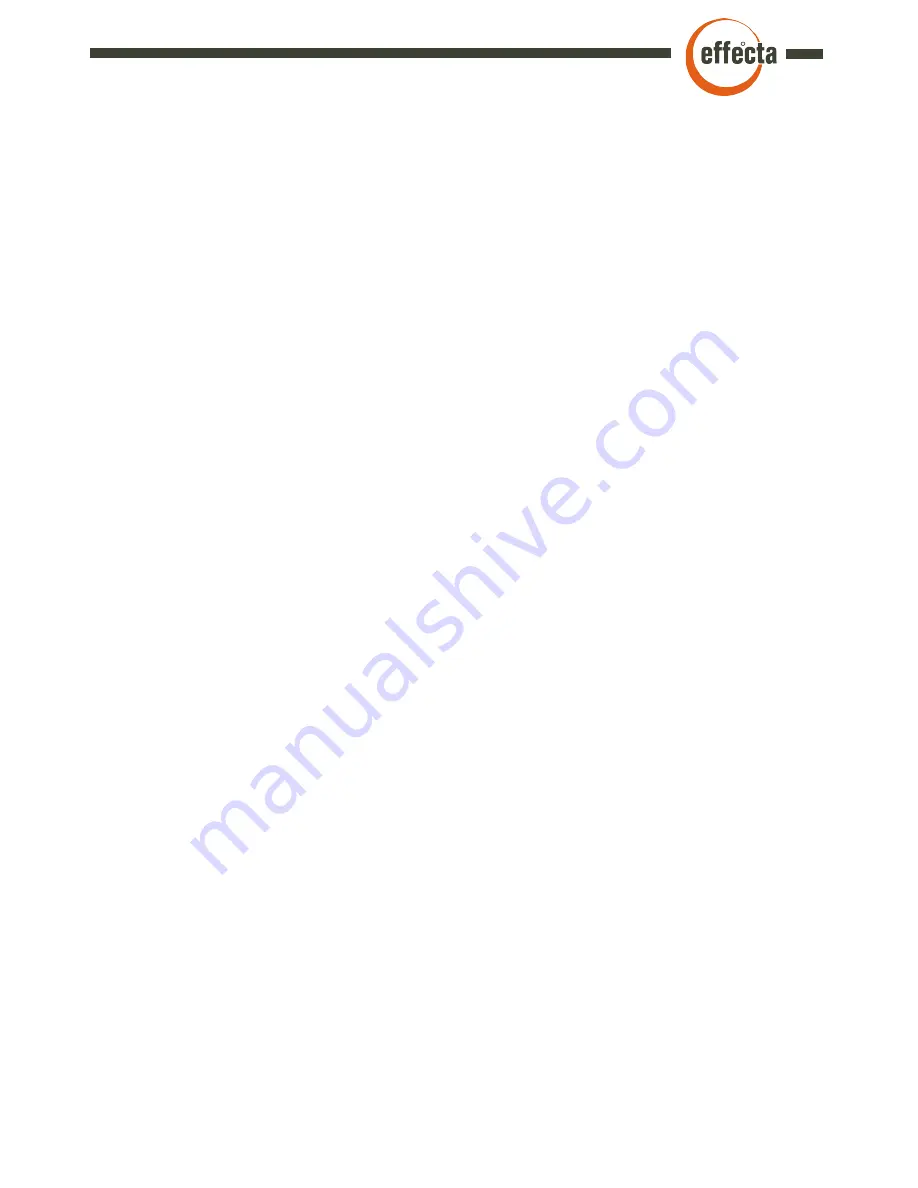
Effecta AB - Västra Rågdalsvägen 21 - 434 99 Kungsbacka - 0300 - 22320 - [email protected]
4
Water content
Before powering up the system with electrical mains please ensure that all the boiler is filled with
water. All pumps controlled by the boiler needs to be in water filled heating circuits where there is
no blockages from circulation.
Doors
All doors and cleaning accesses needs to be closed and sealed before powering up.
Flue / chimney
The boiler must be connected to a approved flue system to evacuate smoke gasses before powe-
ring up the boiler.
Fuel feeding
Depending on what fuel feed option the boiler is equipped with the fuel feed system needs to be
completed before power up as well as the storage filled with pellets.
When above is confirmed please allow electrical mains to the boiler.
▀
Check list before electrical power feed