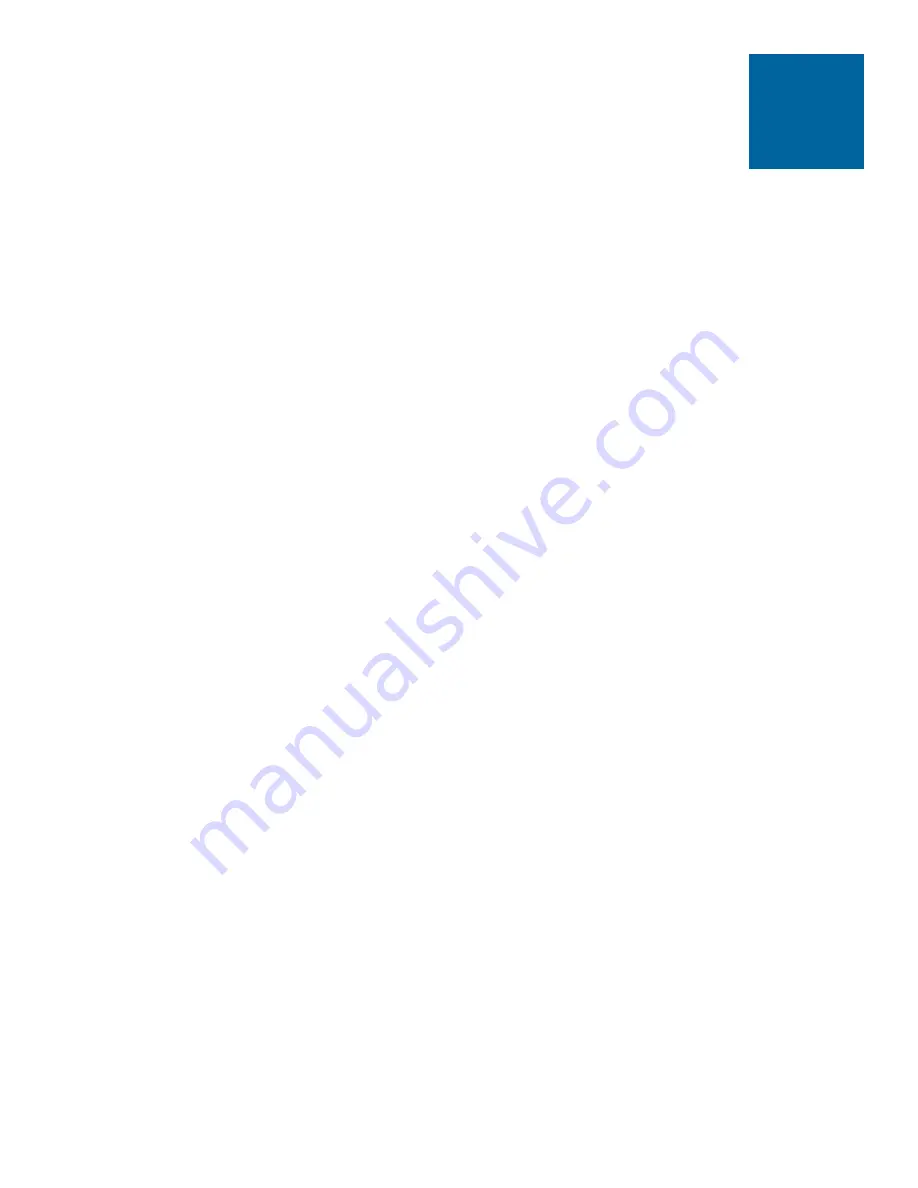
Testing in Timed Mode
• Follow steps in “Testing in Steady Mode” to purge your dispensing tip with fluid.
• Change
to
TIMED
mode.
• Set time to 000.0250 seconds.
• Rest the dispense tip on the Dot Standards sheet.
• Press the foot pedal (or finger switch) to activate the dispense cycle.
Note:
the pedal only needs
to be pressed for a moment. The complete time will run once you activate the dispense cycle.
•
Changing the time changes the deposit size.
If your dot is too small, increase the dispense
time to increase the deposit size. If your dot is too large, decrease the dispense time to
decrease your deposit size.
Testing in Teach Mode
• Follow steps in “Testing in Steady Mode” to purge your dispensing tip with fluid.
• Change
to
TEACH
mode.
• Rest the dispense tip on the Dot Standards sheet.
• Press the foot pedal to establish your dot size. Tapping the foot pedal repeatedly will have a
cumulative effect on the dot size and dispense time.
• Continue to press the foot pedal until you achieve the correct deposit size.
• Save the dispense time setting you just created by pressing
SAVE
. This automatically exits
TEACH
mode and returns you to
TIMED
mode.
• If needed, press
CLEAR
to start over.
If you have any questions at this point, please call us now.
In the USA, call 800-556-3484 between 8:30 a.m. and 5:30 p.m. Eastern time.
In Europe, call +44 (0) 1582 666334.
In Asia, call +86 (21) 5854 2345.
In all other areas, call your authorized EFD distributor or +1-401-434-1680.
Initial Test
Procedures
17