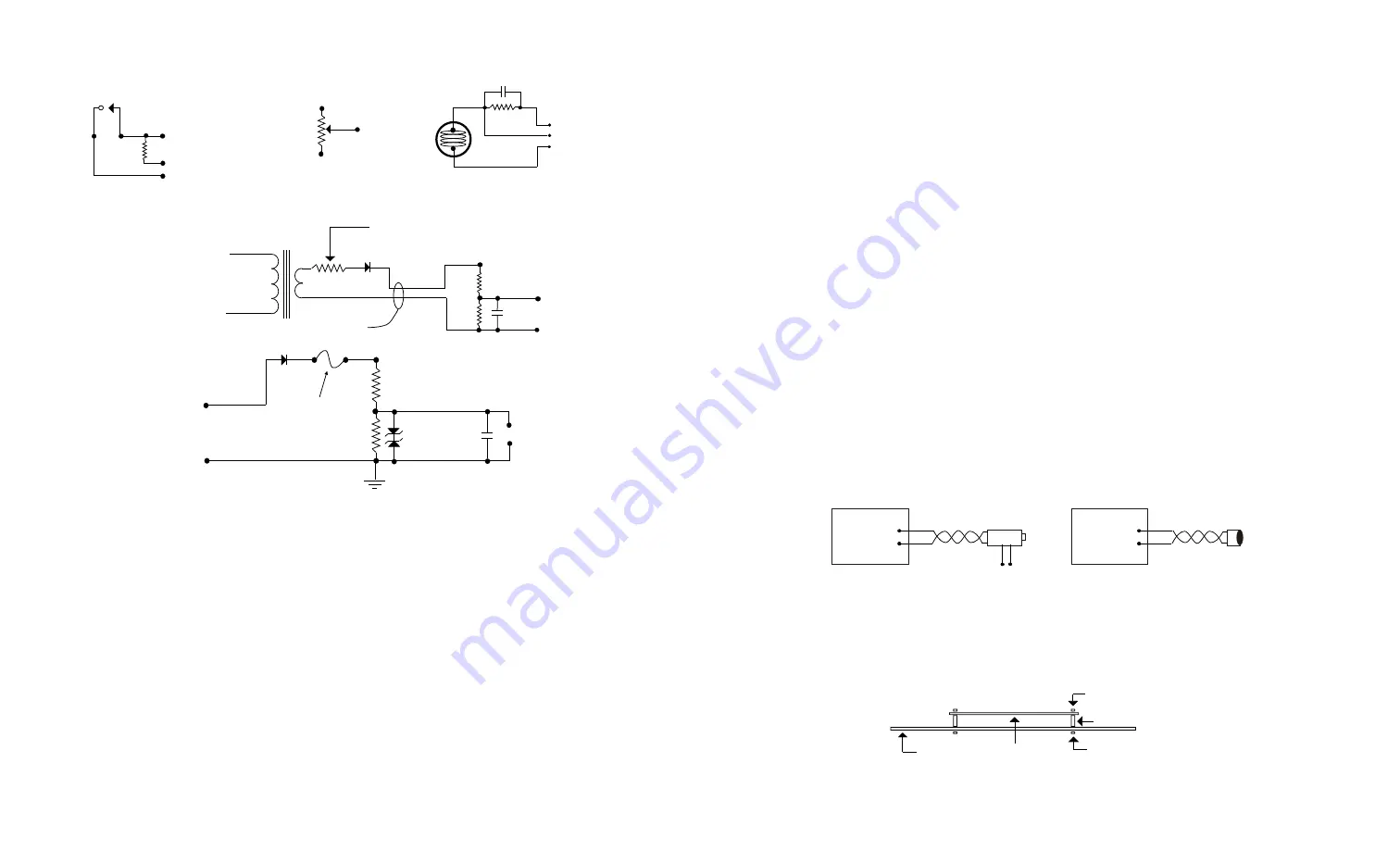
HIGH VOLTAGE INTERFACING
CAUTION: When working with high voltages, the potential for fire, explosion, electrocution, eye injury or blindness
and life threatening injuries or death exists. If you are not familiar with the precautions needed when working with
high voltages, do not attempt to connect high voltage up to these circuits. To prevent the danger of a high voltage
feeding back to the ADC and the fire/injury/electrocution hazard caused by an open or short circuit, 10 volt 2 watt
zener diodes and a 1/4 amp fuse should be connected as shown in figure E. Wire used to interconnect a high voltage
input must be rated for use with the higher voltage. When connecting the ADC to high voltage AC equipment the
method shown in figure D above is recommended.
The following method is used to divide a high voltage down to the 5 volt range needed for input into the ADC. This
method involves the use of two resistors (R1 and R2) which together add up to Rt (total resistance). The total
resistance is determined by using the Ohms Law to compute the resistance needed for a 1 milliamp current flow
through the resistors. EXAMPLE: If your full scale voltage is 100 volts (R = E divided by I) 100 volts divided by .001
amp = 100,000 ohms (100K ohm). To determine the proper ratio, divide 5 volts by the full scale voltage. 5 divided by
100 volts = .05. Multiple this ratio by the total resistance to determine the value of R2. R1 is then equal to the
difference between the total resistance and R2. EXAMPLE: ratio .05 times total resistance 100,000 ohms = 5,000
ohms (the value of R2). Total resistance 100,000 ohms less R2 5,000 ohms = 95,000 ohms (the value of R1). To
determine the power rating needed for the resistor, use the following formula: P = I squared times R. EXAMPLE: .001
squared = .000001 times R1 95,000 ohms = .095 watts. A 1/8 or 1/4 watt resistor would be sufficient.
Page 10
Fuse or Limiting Resistor (330 ohm 1 watt)
1 Amp Diode (50 volt)
AC Primary Voltage
120, 277, 480 etc.
(-)
6 or 12 Volt
Secondary
100 mf
35 volt
24 ga Communication Cable
To Analog
Input
To Analog
Input
(+
)
(-)
1/4 Amp Fuse
Diode
(+
)
High Voltage
AC/D C Input
(-)
Ground for
Safety
R1
R2
(1 ma maximum current
through resistors)
(+
)
R1
R2
100 mf
35 volt
+
FIGURE C
FIGURE D
Switch or Relay
Contacts etc.
(Ref)
To Analog Input
(+
)
10 K ohm
(Reference -/Analog Ground)
DIGITAL INPUT
(0=OFF)
(255=ON)
FIGURE A
(Ref)
(Reference -
/Analog Ground)
To Analog
Input
POTENTIOMETER
MOVEMENT SENSING
FIGURE B
Ref (-)/Analog Ground
To Analog Input
Ref (+)
27K Ohm
Cadmium Sulfide
Photo Cell
+
10 mf Tantalum Capacitor
USING AN ANALOG INPUT
FOR ON/OFF STATUS
MEASURING LIGHT LEVELS
FIGURE E
10K OHM
TYPICAL
IMPORTANT:
The full scale voltage used should be the highest possible voltage that could be present at the high
voltage input.
AC voltages may be applied to the high voltage input if a diode is connected in series and a filter capacitor (100 mf,
35 volt typical) is connected between the ADC analog input and the ADC reference (-). AC voltages over 24 volts or
great enough to create an electrical shock hazard or fire should be connected to the ADC analog input using a step-
down transformer to reduce the high voltage down to the 5 volt range as shown in figure D. A diode and filter
capacitor must be connected on the secondary side of the transformer (a common low current power transformer
may be used).
VOLTAGE INPUT AMPLIFICATION AND SIGNAL CONDITIONING
The ADC-4U11 defaults to a 0 to 4.096 volt input range (setup allows input ranges as low as 0 to .25 volts). When the
input voltage range is required to be lower, (such as with a watt transducer or load cell) an external instrumentation
amplifier must be used to amplify the input signal to the 0 to 4 volt input range of the ADC.
Several general purpose instrumentation amplifiers are available to amplify lower signal levels to the 0 to 4 volt range
required by the ADC (for use with 8, 10 and 12 bit inputs). The VA-1 is a single channel amplifier for connection to
the ADC-4U11, ADC-8U or ADC-12U. The VA-2, VA-4 and VA-8 amplifiers are two, four and eight channel versions of
the VA-1. The VA-1, VA-2, VA-4 and VA-8 all provide 15 turn potentiometer(s) for gain adjustment (amplification
level). The amplification level is adjusted for a 0 to 100 millivolt input at the factory. The amplification level may
adjusted for signal inputs as low as 0 to 5 millivolts or as high as 0 to 5 volts. Lower signal levels (such as the output
signal from a watt transducer, pressure transducer, load cell, etc.) with typical full scale voltages of only 20 to 100
millivolts will require the addition of the VA-1 instrumentation amplifier when connecting to the ADC. Signal levels this
low may require shielded twisted pair wire. The shield should be left disconnected at the source and grounded to an
earth electrical ground at the VA-1.
CONNECTING SENSORS TO THE ADC-4U11
A large variety of sensors, transducers, load cells and other devices that provide an analog output may be connected
to the ADC-4U11. Most types of sensors may be located up to 1,000 feet from the ADC-4U11. Pull up resistors may
be installed on the underside of the ADC-4U11 for 2 wire sensors that receive power from the USB port. The cable
used to connect sensors to the ADC-4U11 should be twisted pair or shielded twisted pair to suppress environmental
noise. Low cost CAT 5 cable works well when multiple sensors are in the same location.
MOUNTING
The ADC-4U11 Analog to Digital card may be mounted in an enclosure (part # EN-C or EN-D) or on a metal mounting
panel using the MT-1 stand-off mounting hardware as shown below. The ADC-4U11 will attach to the 4 stand-off
spacers using 4-40 machine screws (4 mounting holes are provided on the ADC-4U11). Contact technical support for
more information on mounting panels and various mounting layouts.
Page 11
ADC-4U11
+
-
+
-
Twisted Pair
Pressure
Transducer
Power
-
+
ADC-4U11
+
-
+
-
Twisted Pair
2 wire
temperature
sensor
ADC-4U11
SIDE
VIEW
1/2" Stand-Off
1/4" 4-40 Machine Bolt
1/4" 4-40 Machine Bolt
MP-C
Mounting Panel
with MT-1
Stand-Off Kit
10 Volt 5 Watt
Zener Diodes