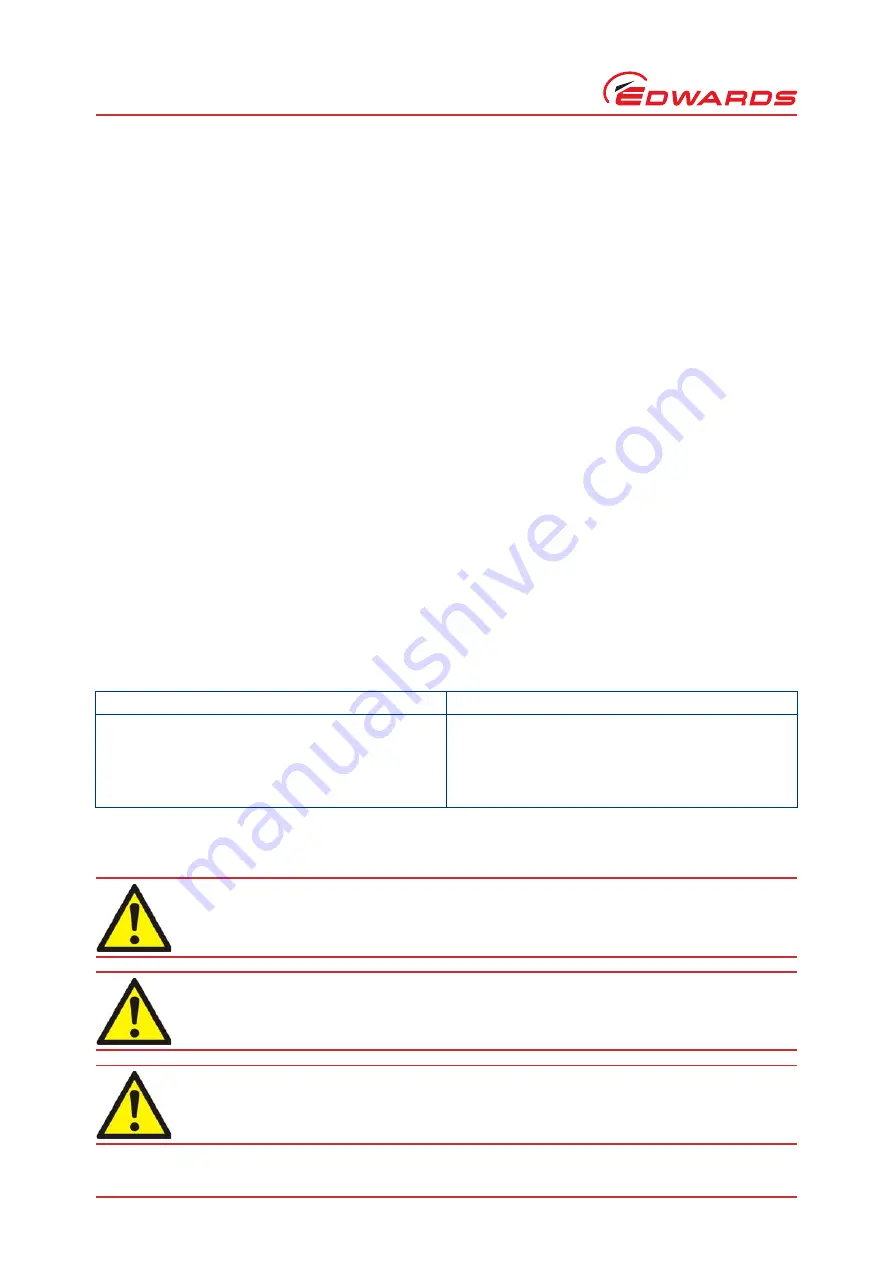
B756-01-880 Issue K
Page 18
© Edwards Limited 2013. All rights reserved.
Edwards and the Edwards logo are trademarks of Edwards Limited.
Installation
3.3.5
Interstage connection (Hi pump variants only)
Use suitable vacuum tube and connectors to connect the interstage port to the vacuum system or to the outlet flange
of another turbo molecular pump. Leave the inlet strainer in the interstage port, unless there is no possibility that
debris can be drawn into the interstage port.
3.4
Vent options, vent valve connection and control
To maintain the cleanliness of the vacuum system whenever the pump is switched off, Edwards recommends venting
the pump (or vacuum system) when the speed of the EXT Split Flow Pump is between full rotational speed and 50%
of full rotational speed. At and above 50% of full rotational speed, the rotor spins fast enough to suppress any back-
streaming of hydrocarbon oil from the backing pump. Venting may be accomplished by one of the following methods.
Use a TAV5 or TAV6 solenoid vent valve accessory (see
) in place of the manual vent valve.
Use a TAV5 or TAV6 solenoid vent valve connected to a convenient flange on the vacuum system.
Use an alternate valve, with an appropriate restriction, connected to the vacuum system. For further
details, contact Edwards.
However, if the pump is manually vented when it is at full rotational speed and the rate of pressure rise is too high,
the pump life may be reduced. When using the manual vent valve supplied, Edwards recommends either limiting the
vent or only opening the vent valve after the EXT Split Flow Pump speed has fallen to 50% of full rotational speed.
Do not vent from the backing line as this may lead to contamination. If venting into the vacuum system, select a point
upstream of the pump to prevent oil back-streaming from the backing line.
If using the TAV5 or TAV6 vent valve, it can be controlled using an EXC Controller or other methods.
gives an
indication of the appropriate orifice size to be fitted to the vent valve for given vacuum system volumes in order that
the vent rate is kept within the limits given in
.
3.5
Electrical installation
Table 6 - Vent restrictor orifice diameter (with atmospheric pressure at the inlet of the vent valve)
Vacuum system volume (l)
Orifice diameter (mm)
< 20
< 1.0
< 10
< 0.7
< 5
< 0.5
< 2
< 0.35
WARNING
The customer must ensure that any electrical circuits are protected from dripping water caused
by condensation on cold surfaces.
WARNING
It is the responsibility of the customer to ensure that the power supply used is correctly rated/
protected.
WARNING
This product requires a separate power supply (not included). The power supply should be
adequately protected against a hazardous live condition (e.g. in case of a short circuit).